Introduction to Heat Treatment for Cast Parts
Metal manufacturers utilize a number of tools to control the mechanical and physical properties of raw materials. An alloy’s chemistry is only one part of the equation: obtaining the final properties can only be achieved through heat treatment. In this introduction, we'll cover the following topics:
- Why heat treatment is important for metalcasting
- Heat treatment for carbon steel vs heat treatment for stainless steel
- The importance of using ASTM standards
- Key heat treatment processes used by foundries and machine shops
Heat treatment is a broad term describing a range of thermal processes used to control an alloy’s properties. These processes ensure a finished product carries the mechanical and physical properties demanded by its application. Encompassing both heating and cooling, heat treatment incorporates a few distinct and equally important phases:
- Ramp-up: heating the metal;
- Soak: maintaining the metal at a desired temperature for a specified amount of time;
- Cooling: cooling to a specified temperature at a controlled rate and in a controlled environment.
An expert understanding of heat treatment is essential for metalcasting foundries. You can have a chemistry with all the right elements, but if you don’t heat and cool the alloy properly, you’ll end up with undesirable material properties. Through heat treatment, foundries create products carrying the desired combination of properties. For many materials, strength (yield and ultimate tensile strength) ductility, hardness, toughness, corrosion resistance and wear resistance are all strongly influenced by heat treatment.
In this blog series, we will be discussing the most common types encountered in foundries and how the Eagle Group draws on modern standards, in-house experience, and a world of collective casting knowledge to deliver the outcomes customers require.
Looking for an in-depth guide on essential heat treatment processes for metalcasting and CNC machining?
We've created a 40-page ebook on heat treatment for cast and machined steel parts – based on our blog series – to help purchasers procure the highest possible quality steel parts. Click below to fill out a short form and claim your free copy.
Why is Heat Treatment Important in Metalcasting?
Metalcasting is a highly specialized and customizable form of metalworking. Foundries like Eagle Alloy and Eagle Precision cast hundreds of ferrous and nonferrous alloys. But manufacturers are more concerned with grades than alloys. Grading systems, like those developed by ASTM and SAE, take chemistry, heat treatment and properties into consideration. Often, the differences between two distinct grades comes down to how they have been heat treated. Different grades require specific targets for mechanical properties, and only heat treatment can produce the desired outcomes. A successful product is one that meets a customer’s specifications in terms of both shape and material properties. This is achieved by following a carefully planned sequence of casting, heat treatment and, sometimes, machining.
All steels are alloys, meaning they are metals created by melting and combining multiple elements. When melted, metals come together in different ways. The result of each elemental combination is a unique microstructure. A microstructure is a microscopic look at a given material’s physical makeup, which reveals to us exactly how an alloy’s constituents have come together to form an internal structure.
Microstructures can contain distinctive phases that are identified when we zoom in on a material. Phases and microstructures are very closely related: phases are distinct crystal structures in a material, whereas microstructures are close-ups of these phases, or combinations of these phases. Steel only has three phases: ferrite, cementite, and austenite. But it has more microstructures than phases because any given microstructure can contain components of each phase, sometimes mixed together. All unique microstructures have their own associated physical properties that collectively contribute to the material performance. As such, understanding and controlling microstructures is critical because they determine an alloy’s physical and mechanical properties. Heat treating is how we achieve the desired microstructures appropriate for a given part.
Zooming in on Microstructures
Imagine trying to build a house with wood where there should be concrete, and concrete where there should be wood. You might have all the right materials, but using them incorrectly means it wouldn’t hold up very long. Microstructures follow the same logic as larger structures: intentionally controlling how and where the elements combine is key to structural integrity.
The image below shows steel microstructures after (left) and before (right) heat treatment.
Heat treatment requires bringing metals above certain critical temperatures. Over a given critical temperature, an alloy’s microstructure will begin to change – the individual constituents will start to move around and bind to each other in new ways. An important characteristic of these critical temperatures is that they are located below the aggregate melting points of alloy mixtures. As such, we can heat treat parts after they have been cast because we are only targeting properties and not geometry.
Therefore, the ultimate goal of heat treating parts in a metalcasting foundry is, at a minimum, to alter their as-cast microstructures to improve performance. As-cast microstructures are the internal structures that result from cooling directly from a liquid to a solid in the mold or media as part of the casting process. After molds are made, we are first concerned with melt chemistry and quality. After castings are poured and solidified, we drill down on heat treatment.
Thermal cycling and heat treatment can be done while the part is still covered in cast material, or after the excess cast material has been removed. When done properly, both methods will get parts to their finished geometry. Without heat treatment, workpieces might look the part (pun intended), but they won’t have the properties to ensure proper performance. This is where an expert foundry partner can help perfect the heat treatment cycles required to produce a superior product.
Heat Treating Carbon Steel vs Heat Treating Stainless Steel
The chemistry of a stainless steel is very different from carbon steel because of the high amount of chromium needed to form the protective oxide layer that makes the product ‘stainless’. Carbon steels typically have much lower amounts of common alloying elements like chromium (Cr), manganese (Mn), nickel (Ni), molybdenum (Mo), vanadium (V), and silicon (Si).
The rule of thumb with stainless steel is that the chemistry and resulting microstructure are the most important factors in achieving the correct final properties. For example, the high amount of chromium (Cr) in stainless steel increases resistance to corrosion and also helps reduce oxidation at high temperatures. The additions of nickel (Ni) and molybdenum (Mo) contribute to a different phase formation which influences strength and corrosion resistance in different environments.
When it comes to thermal treatment on stainless steels, the punchline is: superior corrosion resistance is the reason why many stainless steels are heat treated. When we heat stainless above a critical temperature then cool it rapidly, the natural impurities get locked in closer to the center of the material’s grains, an action that protects the alloy steel from corrosive attacks.
On the other hand, carbon steels are much amenable to and influenced by heat treatment, because: heat treatment drives the totality of carbon steel’s end mechanical properties. In this sense, heat treatment is a much larger part of the formula in the manufacture of carbon steel parts.
Although carbon steel’s primary ingredients are iron (Fe) and carbon (C), common alloying elements found in stainless steels can also be present in carbon grades (often in smaller quantities). The following table outlines the impact of 5 common alloying elements on the mechanical properties of carbon steels:
Following ASTM Heat Treatment Standards
Mixing physical and mechanical properties is a dynamic process: take away a little of one, gain a little of another. Each unique alloy grade is the outcome of tradeoffs. Because there are so many possible combinations, there is a need for broad consensus on what constitutes an appropriate set of properties for a given application. Luckily, centuries of measuring metallic behavior has provided the empirical basis for just such a consensus.
ASTM International is a standard-setting organization that provides the metals industry with voluntary consensus technical standards for many different applications, alloys, and grades. Founded in 1902 under the name American Society for Testing and Materials, their standards allow customers to understand what to expect from a selected grade. Likewise, foundries and other manufacturers can follow formulas that are internationally trusted and updated.
The ASTM International handbook keeps an encyclopedic catalog of thousands of grades of ferrous and nonferrous alloys, complete with tables outlining required mechanical properties and heat treatment protocols. The handbook also outlines the scope of each alloy (purpose and environment it is designed for), general conditions for delivery (conditions that would qualify a part as either conforming or non-conforming), terminology specific to the part in question (useful vocabulary for both suppliers and customers), and more. The ASTM International compendium allows all parties to stay informed and accountable.
When working with a trusted foundry partner, it’s essential to do things by the book. At the Eagle Group we take ASTM standards very seriously because the specifications are contract-binding and bring trust and transparency into our customer relationships. However, ASTM standards are often very general, requiring the expertise of an experienced foundry to zero in on the fractions, and narrow down the necessary conditions to produce a consistent product. The Eagle Group is proud to have a metallurgist and a team of seasoned engineers, who can leverage experience and creativity to deliver superior results. In the words of Eagle Alloy’s Quality Manager and Metallurgist, Jason Bergman: “Many customers come to us thinking there is only one way to do things. We help them see new paths and possibilities by narrowing down the guidelines to something very specific that works for the customer’s unique specs.”
Essential Heat Treatment Processes for Foundries and Machine Shops
In our Heat Treatment series, we’ll be diving deep on the most important heat treatment processes encountered in foundries and machine shops around the world. Below is an introduction to essential heat treatment processes.
Austenitization
Austenitization is the process of heating steel to a temperature high enough to produce austenite, which is the phase structure produced when you heat iron above its austenitization temperature. Above this temperature, the steel’s microstructure will have fully transformed to austenite, which has a unique microstructure that’s able to absorb a significant amount of carbon. Correctly manipulating cooling rates from above the upper transition temperature can produce steel products with superior properties.
Normalizing and Annealing
Normalizing and annealing enhance a steel’s mechanical properties by refining the grains that make up its microstructure.
The thermal process of normalizing a steel is an essential tool for foundries: these are typically the first heat treatment completed for cast carbon steel products. The reason for the name ‘normalizing’ is because this heat treatment results in a much more uniform microstructure across a workpiece. Normalizing produces smaller and more consistent grains across a material, compared to as-cast, mold-cooled structures. A normalizing recipe calls for heating the metal above the upper transition temperature then cooling the metal at room or ambient temperature. This process balances the structural irregularities that result from cooling in the mold, thereby making it more homogenous.
Similar to normalizing, annealing is used to make a part more workable by increasing its ductility and, by correlation, reducing its hardness. The main differences between normalizing and annealing are the cooling rates involved. Normalizing calls for cooling steels at room temperature, while annealing requires the steel to cool inside the furnace as the furance temperature gets methodically ramped down: naturally, this means the steel takes longer to cool.
The result of annealed steel is a more ductile and workable part than a tempered steel. Annealed steel can often become soft enough that it can be cold worked (manipulated into new shapes at room temperature). Increasing the conductive and magnetic properties of a material can also be achieved through annealing.
Quenching
Quenching is defined by ASTM International as rapid cooling (of steel, in our case) at a rate sufficient to preserve or produce desired material characteristics. Steel will be cooled much faster in a liquid than in air. Quenching is one of the methods to manipulate the cooling rate to tailor the microstructure and resulting properties.
Quenching can be conducted with many different quenching mediums; water, brine, polymers, oils and gases are all popular quenchants that produce different cooling rates and outcomes. Because of this diversity in choice, quenching is a separate area of study in its own right.
Hardening
Quenching is also an essential step in hardening many grades of steel. Quenching is often performed after austenitization in a process known as phase transformation hardening - a very common method to strengthen and harden carbon steel.
Hardening steel is an important outcome of a few different heat treatment processes. Often referred to more specifically by the type of hardening – such as quench hardening, case hardening, or precipitation hardening – all these methods target the same goal: to harden and strengthen a steel in different ways.
Tempering
A drawback of hardening is that it also causes steel to become very brittle and prone to breaking. As such, hardened steel usually must be tempered for any practical applications.
Tempering is a form of stress relief that targets an alloy’s ductility. Tempering is a natural follow-on after hardening a steel because it makes brittle steel more ductile and more machinable. After hardening, often a metal will carry internal stresses by virtue of its new hardness. Hard metal often means brittle metal, and brittle workpieces crack more easily (interestingly, cracking is itself a form of natural stress relief). Tempering reduces hardness and brittleness and increases ductility, but it still maintains a hardness sufficient enough that a piece can be used in many applications requiring high-strength steel.
Stress Relieving
Stress relieving describes the general heat treating practice of removing a workpiece’s internal stresses. There are several ways to reduce internal stresses, and some of them are used to simultaneously achieve other desired mechanical properties such as increased ductility. Stress relieving, strictly speaking, should be understood as a method to reduce internal stresses that arise after machining or welding: in other words, tensions that result from applying manufacturing processes to a part. In CNC machining, stress relief is commonly used to remove mechanical deformations and weak spots in the newly machined material.
As a casting-to-completion manufacturing partner, the Eagle Group casts and machines parts to meet dimensional specifications by leveraging decades of casting experience. We also employ modern tools like robotics and 3D scanning to ensure tolerances fall within tight ranges, and orders arrive on time.
As part of our casting facilities, we employ a broad range of tried and tested heat treating practices to ensure parts not only conform to dimensional specifications, but also perform exactly how they should under stress in the field. In our Heat Treatment series, we open the doors on the Eagle Group’s heat treatment facilities and explore the most common practices used to deliver superior cast products.
Because it would be impossible to cover all practical aspects of heat treatment, the examples of processes and products you find across our blog series are meant to help make sense of important concepts. In the real world, each customer’s requirements are different, and the Eagle Group is ready and willing to explore all options.
Learn More About Heat Treatment in Our Dedicated Series
Tags: Metallurgy, Heat Treatment
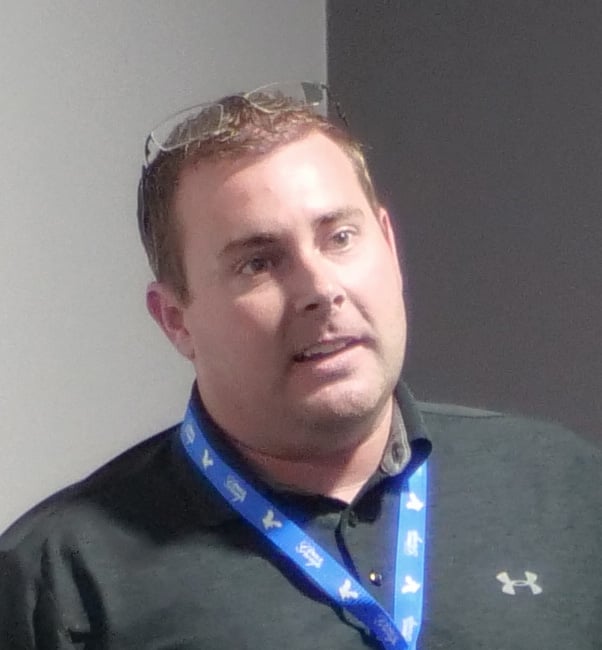
Written by Nic Tarzwell
Nic Tarzwell is Chief Technical Officer at Eagle Alloy, Inc. He has been with the company since 2007.