How Investment Casting Compares to Other Metalcasting Methods
This article was updated on April 15, 2025.
Metalcasting, one of the oldest manufacturing methods, has evolved dramatically from its ancient roots to modern processes capable of casting nearly any alloy into complex designs. While the basic principle—pouring molten material into a pre-shaped mold to create a specific shape—remains unchanged, manufacturers use different casting techniques depending on the part’s design and production requirements.
All metalcasting processes have their own unique characteristics. When designing a new part for casting, selecting the most appropriate process should be determined by several factors, including:
- Tooling costs
- Labor costs
- Design characteristics
- Desired appearance
The goal for both the manufacturer and supplier is to find the optimal balance that produces the lowest per-part cost at a given quantity while meeting or exceeding all quality requirements.
In this blog, we give an overview of investment casting, including its advantages and disadvantages, capabilities and common applications. We then compare investment casting to five other metal casting processes—shell mold casting, greensand casting, airset casting, permanent mold casting and die casting—highlighting how manufacturers select techniques to meet design and production needs.
Understanding Investment Casting
The Investment Casting Process
Investment casting is a molding technique that involves the creation of a wax replica in the shape of the desired final part. The replica is coated with ceramic slurry or another heat-resistant material to create a disposable mold. After the outer material has set, forming an outer shell, heat is applied to melt and drain the wax, leaving a cavity in the shape of the desired component. Molten metal is then poured into the hollow shell. Once the metal cools and hardens, the outer ceramic shell is broken off to reveal the cast part.
Advantages and Disadvantages of Investment Casting
Investment casting is ideal for a broad range of products. It can accommodate nearly any alloy, ensuring an optimal balance of strength, weight, and cost. Perhaps most importantly, investment casting excels in producing intricate shapes and complex inner cavities that cannot be achieved through other casting methods. Investment cast components are highly detailed, precise and accurate, exhibiting smooth finishes that often need little to no post-processing. The use of robotics in investment casting automates processes and enhances control, improving consistency, reducing defects and increasing production efficiency. Many parts that would otherwise have to be fabricated or machined can be efficiently molded through the investment casting process.
There are times when investment casting is not the ideal process. Comparatively high labor costs and setup costs can make other casting processes a better fit in some cases. Furthermore, not every product needs the accurate dimensions, tight tolerances and smooth surface finish offered by investment casting.
Capabilities of Investment Casting
Investment casting is ideal for low to medium production runs of complex parts that require high tolerances and excellent surface finishes. Below is a summary of the characteristics and capabilities offered by Eagle Precision Cast Parts.
Table 1: Characteristics and Capabilities of Eagle Precision Cast Parts
To learn more about Eagle Precision's investment casting capabilities, download our spec sheet:
Other Casting Methods
To make an informed decision about the best manufacturing method for your needs, it’s important to understand how investment casting compares to other casting techniques. In this section, we will compare investment casting to five other metal casting processes. We’ll start by exploring three methods offered by the Eagle Group, which include processes provided by Eagle Alloy (shell mold and airset) and Eagle Aluminum (greensand).
Investment Casting Compared to Other Eagle Group Casting Processes
Investment Casting vs. Shell Mold Casting
Investment casting is known for its ability to hold to tight tolerances and produce parts with intricate inner cavities and excellent surface finishes. Similarly, shell mold casting, which involves heat-bonded sand patterns and cores, offers comparatively high quality in the same categories. However, investment casting can meet much tighter tolerances than shell mold casting and provide even smoother surface finish.
In terms of tooling costs, investment casting is generally more economical, though the process itself requires several steps to create the ceramic molds used in casting. This means that more labor is required, and some phases in the process require skill and experience to execute properly. In contrast, shell mold casting requires fewer steps to make a mold, which often translates to fewer man-hours per part. While lower volume projects may be more economical with investment casting, shell mold casting often has lower part costs for medium- to high-volume production scenarios.
Both shell molding and investment casting can accommodate nearly any alloy, including ferrous and non-ferrous metals.
Investment Casting vs. Greensand Casting
Greensand casting is another sand-based casting method, but unlike shell molding, no heat is applied. Instead, clay-like substances in the sand bind the particles together around patterns to create molds. This method is highly versatile and suitable for both small and large castings. However, when it comes to tolerances and surface finish, greensand casting falls behind both shell molding and investment casting. Greensand casting is generally best suited for larger components where fine detail and tight tolerances are not as critical.
Tooling costs for greensand are lower than those for investment casting, partially because no heat is applied to greensand patterns, making it possible to use plastic or even wood as tooling materials. Within greensand casting, there are two main options that present their own pros and cons: manual greensand casting and automated greensand casting. Manual greensand casting is more labor intensive, requiring similar man-hours per part to investment casting. Automated greensand casting requires less labor but comes with high startup costs. In both cases, precise control over sand composition can be an obstacle for foundries.
Like investment casting and shell mold casting, greensand casting offers high repeatability and can also accommodate a wide variety of alloys.
Investment Casting vs. Airset Casting
Airset casting (or no-bake casting) is another sand-based process that does not require the application of heat, instead using chemically bonded sand molds. This method offers better surface finish, tighter dimensional tolerances and better edge definition compared to shell molding and greensand casting, as it can utilize much finer sand. It is also more capable of handling complex geometries and thicker wall sections compared to other sand casting techniques.
While airset casting is more precise than shell molding and greensand, it offers moderate repeatability compared to investment casting. This is due to the sand molds being typically single-use and manually or semi-automatically prepared, so part-to-part consistency can vary slightly—especially in complex geometries or tight tolerance zones. Airset casting still falls short of investment casting when it comes to achieving extremely fine detail, very thin walls or the highest levels of dimensional accuracy and surface quality.
In terms of size capabilities, airset casting is particularly well-suited for medium to very large components. When it comes to tooling costs, it tends to be more cost-effective for larger parts and low- to medium-volume production compared to investment casting, especially where absolute uniformity is not a critical requirement.
One notable consideration with airset casting is its regulatory and environmental implications. The bonding agents and chemicals used in the process can create additional compliance requirements, often requiring foundries to file documentation with the Environmental Protection Agency to ensure worker safety and environmental protection.
Investment Casting Compared to Other Industry Casting Processes
While the Eagle Group specializes in investment, shell mold, greensand and airset casting, it's also important to understand how investment casting compares to other industry-standard processes. Below are comparisons between investment casting and two popular non-destructive casting methods.
Investment Casting vs. Permanent Mold Casting
Unlike investment casting, shell molding or greensand casting, which use sand or refractory material to form mold walls, molds in permanent mold casting are typically made of steel or cast iron and are reused again and again.
While the steel or cast iron molds are sturdy and reusable, they are less adaptable for large-scale components compared to sand casting techniques, which can accommodate much larger parts. The tolerances and surface finish achieved by permanent mold casting fall between shell molding and greensand casting. The rigidity of the molds makes them less ideal for highly complex, large geometries. Neither permanent mold casting nor sand casting methods can match the precision and fine finish produced by investment casting.
For high volume runs, permanent mold casting is often the most economically viable option, but tooling costs can be prohibitive for low- or medium-volume runs. The upfront investment in creating durable steel or cast iron molds is high, as these molds need to withstand repeated use. Despite the high initial tooling costs, the per-unit cost decreases as the production volume increases, since the molds are used multiple times. Labor costs for permanent mold casting are generally lower than those of other casting methods.
Also, since permanent molds are made from metals, their melting points are critical. The metals being cast in permanent molds must have significantly lower melting points than the metals making up the mold. Therefore, permanent mold casting is often used for aluminum or other non-ferrous alloys.
Investment Casting vs. Die Casting
Die casting is another method that uses reusable molds, typically made of steel. In this process, molten metal is injected under high pressure into the mold, capable of forming precise and thin-walled parts. It offers good dimensional accuracy and smooth surfaces, though not as fine as investment casting. Post-processing of die-cast parts is often required to meet specific finishes and dimensions, while investment casting is more often able to produce “cast to spec” parts.
Similar to permanent mold casting, die casting is suited for high-volume production of non-ferrous metals with low melting points like aluminum, magnesium and zinc. However, its high tooling costs—driven by the need for precision-machined, durable steel molds—can make it less cost-effective for low- or medium-volume runs. Additionally, while die casting is highly automated and efficient in large-scale production, it is generally limited to smaller part sizes due to equipment constraints and the pressures involved.
By contrast, investment casting is more flexible in terms of part geometry and size. Though investment casting can be more labor-intensive due to its multi-step process, it overtakes permanent mold casting for producing intricate designs with tighter tolerances, especially for smaller runs.
Table 2: Investment Casting Compared to Other Metal Casting Methods
Applications of Investment Casting
Investment casting is widely used across industries that require durable, precise parts capable of withstanding high loads, temperatures and pressures. In the aerospace and medical sectors, its ability to produce complex parts with tight tolerances and excellent surface finishes makes it an ideal choice. The oil and gas industry and valve industry rely on investment casting for strong, reliable components that withstand harsh conditions. Other industries like automotive, energy and defense require precise control over the alloys used to meet specific performance needs, whether for strength, corrosion resistance or other critical characteristics. Investment casting offers the flexibility to work with a wide range of alloys, providing precise control over material properties to ensure that parts meet these exacting requirements.
Investment Casting Services at Eagle Precision
Since 1993, Eagle Precision has operated as a full-service manufacturing facility specializing in investment casting. We are a proud member of the Eagle Group family of manufacturers and committed to delivering high-quality casting solutions. Contact us today to learn how we can support your products and manufacturing needs.
This post is an update to the ebook Investment Casting Process Guide. It was prepared by Eagle Precision Cast Parts, Inc. Click below to download the ebook for free:
Tags: Metalcasting, Processes, Investment Casting
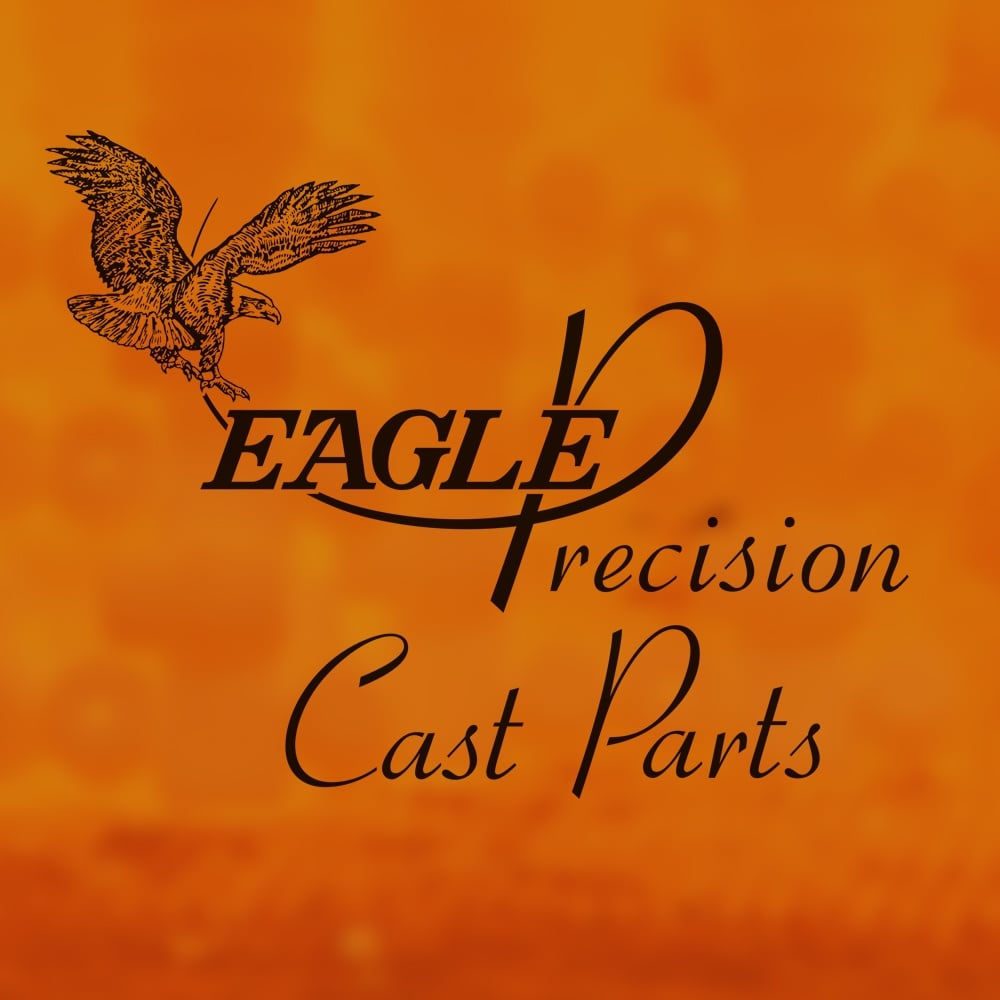
Written by Deb Pipoly
Deb Pipoly is President of Eagle Precision Cast Parts, an investment casting company located in Muskegon, MI.