Induction Melting at Eagle Alloy
At Eagle Alloy, we recently expanded our capabilities by investing in three new Inductotherm induction melting furnaces. Since opening in 1979, we’ve always used induction for melting because of its efficiency and flexibility in comparison to other heating methods. These new furnaces allow us to increase our melting capacity both now and in the future.
It's easy to agree with Inductotherm when they say that "watching a piece of metal in a coil turn cherry red in a matter of seconds can be surprising to those unfamiliar with induction heating." The process of induction heating is as fascinating as it is useful. Here, we explore the origins of induction heating and its applications in metalcasting.
Brief History of Induction Melting
Induction heating is a scientifically advanced process, and designing induction heating equipment requires knowledge of physics, electromagnetism, power electronics and process control. For hundreds, even thousands of years, metalcasters had to use simpler, less efficient methods. The first principles of induction heating were discovered in 1831 by British scientist, Michael Faraday. Then, in the early 1900s, engineers started looking for ways to use induction to melt steel. By the late 1920s, induction ovens were melting steel in both England and Ohio. Through World War II, the technology was widely in use in the automotive and defense industries in Europe and the United States. Today, induction heating and induction melting are mainstays of industrial manufacturing.
How Induction Melting Works
Other heating methods work by transferring heat through convection, conduction or radiation to the surface of an object. From the surface, the heat then transfers inward toward the core of the object. Conduction works by transferring heat through physical contact. In an electric stovetop, the hot burner transfers heat to the cookware through conduction, which in turn transfers heat to the food. A simple example of radiation heat transfer occurs when you warm your hands over a fire. In cooking, and industrial heating, multiple heat transfer methods are often at work simultaneously.
Induction heating works differently: induction involves surrounding an electrically conductive object (like metal, for instance) with an electromagnetic field. The electromagnetic field penetrates the surface of the object, and the object's electrical resistance opposes the current of the field, creating heat. The metal's magnetic properties lead to internal friction, generating even more heat.
One key difference between induction and other heating methods is that the induction coils that create the electromagnetic field do not have to touch the object being heated. Even more interestingly, the coils themselves do not emanate heat. The air inside an induction furnace running full blast is still room temperature unless there's a metal object inside it to produce heat.
Beyond the basic principles of induction, there are many variables that determine how an object should be heated. For example, thin objects can be heated with higher frequency currents, while thicker objects work better with lower frequencies. Magnetic materials heat more easily through induction because they create more internal friction. Better conductors are more difficult to heat through induction, because they offer less resistance to the inductive current.
Steel works especially well with induction, because it has a high resistivity factor and is magnetic. Aluminum and copper, on the other hand, can still be heated through induction but require more energy inputs.
Why Metalcasting Facilities Use Induction
Because of steel's high resistivity, it's the perfect material for induction melting. Steel casting facilities like Eagle Alloy and Eagle Precision utilize induction heating for everything from melting to heat treating. The process is not only highly efficient, but also allows us to carefully control the amount of energy used for heating.
When we melt an alloy for casting, we fill our Inductotherm Heavy Steel Shell Furnaces (pictured, top) with a charge and flip the proverbial switch on our VIP Multi-Outlet Power Supply Unit. From there, up to 1750 kilowatts of energy flow into one or both of the two crucibles attached to the power supply. Each crucible has a melting capacity of 2.5 tons, but we can also melt small amounts of metal when needed.
As you may know from reading this blog, we are a lean manufacturing company. In terms of melting, that means we only melt the exact amount of metal we need for a job. We also cast a wide variety of alloys. Inductive melting's flexibility allows us precisely adjust the amount of energy used to melt a charge.
Another advantage of induction melting is a phenomenon called "inductive stirring." Once the metal in the crucible is molten, inductive currents cause the material to move and mix. This improves alloying properties and results in a more homogenous casting material.
To learn more about induction heating and industrial induction heating equipment, visit Inductotherm's Resources page.
Tags: Capabilities, Melting, Induction
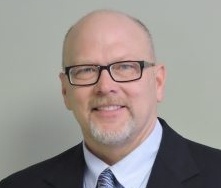
Written by Dave Fazakerley
Dave is Vice President of Manufacturing at Eagle Alloy in Muskegon, MI. He has been with Eagle since its inception in 1979.