8 Key Metals Used in Casting
We're here to talk about METAL
No, not that kind of metal–actual metal, like the kind that your car is made out of, that replaced your uncle's bad knee, that holds up the skyscrapers downtown, that keeps cruise ships afloat, that built the rocket that catapulted the telecom satellite into space so you can have an internet connection, that makes up that satellite...
A lot of things are made out of metal. You get the idea.
What Is Metal?
Good question! The answer is fairly simple, even if you don't know much about chemistry. Any substance that meets the definition of metal exhibits four distinct properties:
- Metals have a shiny appearance (unless they're dirty or rusty)
- Metals conduct both electricity and heat
- Metals are malleable, meaning they can bend without breaking
- Metals can combine with other metals to create alloys
Here, we're going to discuss some of the most common metals used in metalcasting and machining. Different cast parts have different requirements. For example, some need to be as strong as possible, while others need to be as light as possible. The right metal for one part might not be the right metal for another, so it's important to know your options before buying cast parts. Once you choose a metal casting supplier, they can work with you to further determine the optimal material to use in your casting.
To get started, here is an overview of the eight most common metals used in manufacturing today.
- Gray Iron
- White Iron
- Ductile Iron
- Stainless Steel
- Carbon Steel
- Copper-Based Alloy
- Nickel-Based Alloy
- Aluminum Alloy
Gray Iron
Depending on the class of gray iron, different levels of machinability and strength can be achieved. Softer, more machinable gray iron can have tensile strengths as low as 20,000 psi. Tougher, less machinable iron can have tensile strengths three times higher.
White Iron
White Iron is known for its excellent wear resistance. Certain types of white iron have high levels of chromium or other alloys to enhance performance in high-temperature environments, or to provide corrosion resistance.
Ductile Iron
Ductile iron also ranges in strength and possesses a higher tensile strength than gray iron. This wide range of strengths allows ductile iron to serve a wide variety of markets.
Stainless Steel
Stainless steel is the classification of steel that contains a chromium content of 10.5% or higher. It’s best known for its corrosion resistance and also offers a high level of toughness. Higher levels of corrosion resistance can be reached using higher levels of chromium and molybdenum. Drawbacks to stainless steel include its lower level of machinability and medium tensile strength. These properties make stainless steel a great option for parts in oxidizing or corrosive environments.
Carbon Steel
Carbon steel has virtually no alloying elements. As a result, carbon steel offers very high level of machinability and weldability, while maintaining a high level of toughness.
Alloy steel is created by adding elements to carbon steel. These elements can include: manganese, nickel, molybdenum, silicon, vanadium, chromium, boron and titanium. Generally speaking, alloy steels have improved tensile strength, hardness and wear resistance, but sacrifice some weldability and toughness. |
Copper-Based Alloy
Copper-based alloys, in general, have a high level of corrosion resistance which can make these metals a great choice for long-term cost efficiency. Apart from that, the properties are dependent on what other elements are in the end combination. One of the most popular copper-based alloys is brass, which is a made up of copper and zinc as well as bronze–which is itself an alloy, generally made up of copper and tin and/or lead.
Nickel-Based Alloy
Nickel-based alloys have excellent corrosion resistance. Nickel is often coupled with copper, chromium, zinc, iron, and manganese to achieve different properties. The right combinations can have the tensile strength of carbon steel with good ductility and wear resistance. Alloys containing high levels of nickel are often used in chemical handling equipment.
Aluminum
Aluminum alloy, a popular choice in die casting, is a very castable alloy. Other great qualities of aluminum are its high level of machinability, which can reduce costs, and its high level of corrosion resistance, which allows aluminum to have a wide range of applications.
Metal Comparison Chart
The below chart provides a comparison of various alloy characteristics, including corrosion resistance, machinability, price, tensile strength, hardness, weldability, wear resistance and toughness.
Getting ready to purchase cast parts can be a complicated experience. That's why we offer plenty of resources to help you through the process, from our Shell Molding Process paper to our Buyer's Guide for Cast Parts. If you have further questions about any of the topics we cover, feel free to contact us for a free consultation.
To dive even deeper into the technical details of metalcasting and CNC machining, be sure to download our free ebook. It covers essential processes and considerations to help you make confident, informed decisions when choosing the right metal for your cast product.
Tags: Materials, Metals, Metal Properties
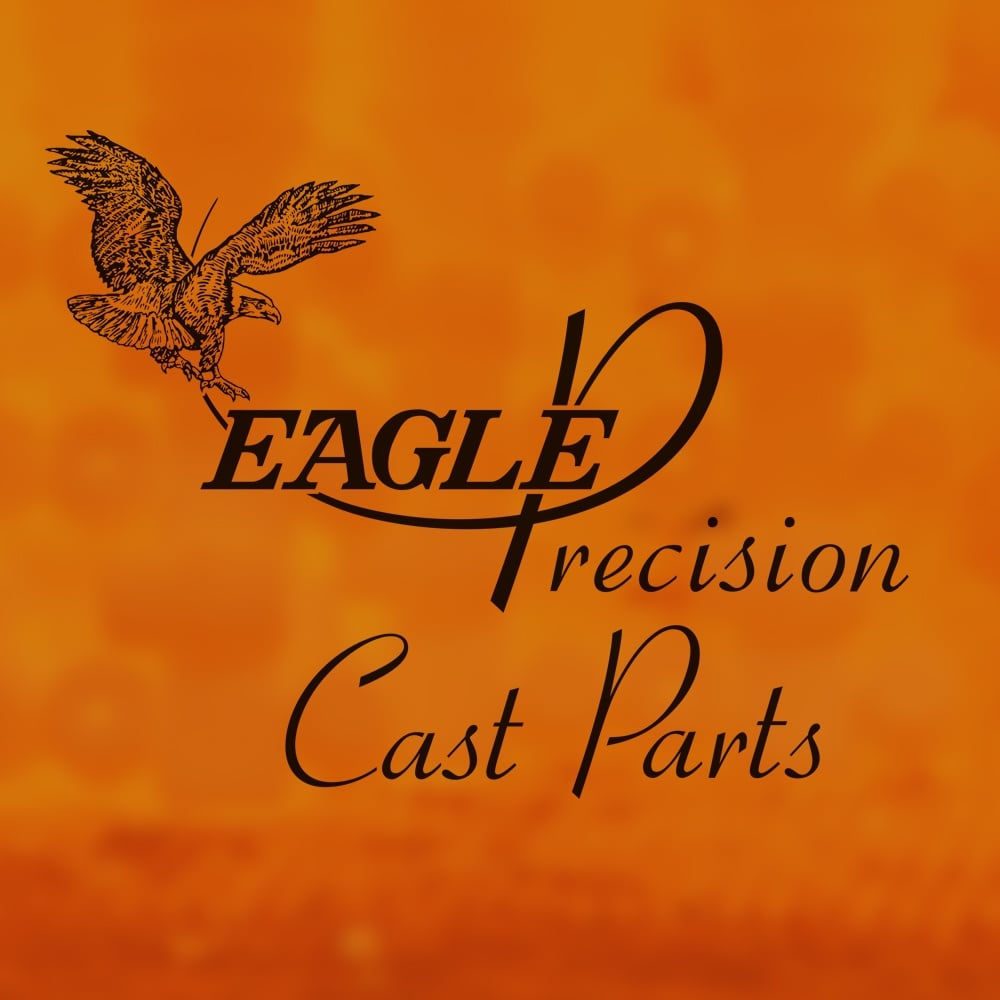
Written by Deb Pipoly
Deb Pipoly is President of Eagle Precision Cast Parts, an investment casting company located in Muskegon, MI.