Metal Properties: Ductility
Ductility describes a metal’s amenability to being drawn or stretched without breaking. It is one of the crowning mechanical properties of a metal. Without a sound understanding of the science of ductility, manufacturers would be unable to guarantee the safety of their machinery.
In this blog, we’ll explain why manufacturers rely on ductility to guide them in casting parts that uphold integrity in service while protecting machinery against catastrophic failure.
Some of the practical engineering questions we’ll be exploring in this blog are:
- How far can a piece of material be stretched before it fractures?
- What metallurgical techniques are used to make a metal more or less ductile?
- How is ductility related to other mechanical properties?
- Why is ductility an important property for metal castings?
When Ductility Is Important for Metal Parts
Before we begin, it's useful to break down the industrial importance of ductility into two cases.
- Taking a lump of metal and extruding it to create wire
- Leveraging ductility to build parts that can withstand significant stress before fracturing
For wire manufacturers, the first category is relevant: think broadband cables, electronics, or the copper wires running through your walls. In these cases, ductility is the property that determines which metals are best suited to making wire. The second category concerns design safety and performance for metal parts made through casting and machining. For manufacturers like the Eagle Group, understanding ductility allows us to produce parts as they are needed in the real world.
If you’re working with the Eagle Group to bring a new product design to life, you’ll want to start the ductility discussion as soon as the onboarding process begins.
Why Is Ductility a Critical Property for Cast Parts?
Ductility is one of the most important properties in metalcasting. It tells us how the material will perform in service, and what level of deformation the product can handle before it fails.
Specifically, we want to know whether each part’s failure mode will be brittle or ductile. In a brittle mode, the part breaks almost immediately following an outsized or unexpected stress. But when the failure mode is ductile, the part will deform before breaking. In fact, if a part’s failure mode is sufficiently ductile, it can withstand a certain amount of deformation, and even cracks on the surface, and still perform as expected within a given set of parameters. In this way, ductility is a property that determines the safety of pushing a part beyond its intended stress level.
Let’s look at some real-life scenarios that call for significant ductility. Structural beams are a good example: imagine an earthquake or a hurricane striking a building. A high level of ductility ensures that the building will absorb significant forces before its frame collapses. Another common case-in-point of high ductility is a valve body. Valve bodies’ operating environments expose parts to a wide range of pressures and temperatures, but they still maintain their minimum mechanical properties thanks to their ductility. In the event of a pressure leak, the valve's failure mode should be ductile instead of brittle in order to prevent a potentially catastrophic leakage event.
How Do We Measure Ductility?
Unlike physical properties like conductivity and density, which are observable without having to alter the physical state of a material, mechanical properties can only be measured by performing stress tests and observing behavior. Two tests are used to determine a material’s ductility: 1) percent elongation, and 2) percent reduction in area.
In the percent elongation test (1), a line is drawn on the specimen in its machine state (i.e., before the test begins). Then the test begins pulling the specimen by both ends until it fractures. After the fracture we take a measurement: how far did the bar stretch between the line we drew and the failure point (the exact spot of the fracture)? We convert that measurement into a percentage and, voilà, we have our percent elongation. And from this very same test, we can record the second key measurement in understanding a specimen’s ductility.
Percent reduction in area (2) describes what happens at the neck of a test specimen after a tensile test. Test materials with sufficient ductility will develop what is called a ‘neck’ around the point of failure. Imagine the shape of a bowtie: the narrowed middle section, the thicker edges. This is a little what a ‘neck’ looks like in a tensile test. And when we measure the outside edge of the specimen to the inside point of failure, we get the reduction of area: it effectively tells us how much the metal sucked in close to the break point.
Ductility, Strength and Hardness
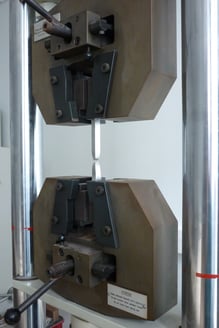
A tensile test is one of the most important assessments in metallurgical testing in order to clear a material for use. Using a tensile test, we can ascertain both strength and ductility measurements. For strength, we are recording the yield strength and ultimate tensile strength (which we’ve covered in another blog). For ductility, we are making note of the percent elongation and the reduction in area. All four of these measurements are determined from a tensile test (pictured right).
However, we can utilize mechanical tests other than the tensile test to measure a material’s strength and, by inverse relation, ductility. Over the years, metallurgists have learned to use correlations between mechanical properties to find less destructive ways to determine a material’s properties. The most common shortcut to identify strength and ductility is through a hardness test.
Hardness is a mechanical property that measures a material’s resistance to localized deformation induced by mechanical indentation. In other words, hardness is a measure of how well a material can take a localized pounding from a sharp object. In a hardness test, we put pressure on a metal’s surface with an indenter and measure the resistance.
When it comes to typical cast parts, the Brinell hardness test is best suited to the typical part size we produce at Eagle Alloy. There is a well-established mathematical correlation between hardness and strength; by taking the results of a Brinell hardness test, we can calculate material strength. And with a precise knowledge of the desired strength/ductility profile, we can use Brinell hardness numbers to deduce ductility. At the Eagle Group, we have a two-step system: with each of our alloy grades, we send samples out for 3rd party tensile testing and provide the accompanying certification that confirms each alloy as the grade advertised. The second step is a Brinell test after every batch for every customer. This two-step system ensures our material mixtures are exactly what our customers are expecting.
Stainless vs Carbon Steel: Is There a Difference in Ductility?
Despite sharing the same primary raw material (Fe = iron), the ductile behaviors of carbon steel and stainless steel are quite different. Stainless steel’s ductility is almost entirely dependent on the batch’s chemical composition. Part of the reason is that alloying ingredients used in stainless steel, such as nickel (Ni) and manganese (Mn), are ductile metals and therefore add to the overall ductile character of the melt. The other key ingredient in most austenitic stainless steel, chromium (Cr), is in fact a brittle metal, but because it’s joined in rank by manganese and nickel, it doesn’t impact a melt’s ductility to any significant degree.
In general, it’s easier to achieve a state of higher ductility with a low-to-medium strength profile in stainless steels. Austenitic grades of stainless steels are great candidates in that they combine a high degree of ductility with a strong resistance to heat and corrosion. As mentioned above, these properties are the result of chemistry.
But if you’re looking for a very high strength material, such as some carbon steels, you’ll have to give a little on the ductility front. Unlike stainless steels, carbon steels depend on heat treatment to determine the final level of ductility. Heat treatment is the process of controlled heating and cooling of a metal in order to bring out the mechanical properties that make a material fit for its intended application. It is a predictable and precise way to achieve the desired set of mechanical and physical properties that a customer requires.
The Science Behind a Metal’s Ductility
There’s an important atomic ingredient in metals that is responsible for their ductility: in metallic bonds, some of an atom’s electrons become detached from the rest of the atom and are free to move around the entire material field. This action creates a special environment in the metal’s structure called a ‘slip plane.’ Slip planes allow areas packed with atoms to move past each other without colliding. On a molecular level the atoms slip right past each other and continue on their way instead of colliding and forcing a fracture.
From this atomic viewpoint, it’s easy to distinguish more ductile metals from the less ductile: with a few exceptions, the most ductile metals have more electron shells. Electron shells are the orbits followed by electrons around an atom’s nucleus. Each shell has a physical maximum of electrons it can accommodate. Once a shell is full, the electrons find space by forming and following another orbit outside the previous shell. In this respect, there is a relationship between the total number of electrons in a metal and its ductility.
The Most Ductile Metals
Gold (Au) tops the charts, and even earns itself a spot in the Guinness Book of World Records: a single gram of gold can be strung out into a wire 2.4 kilometers/1.5 miles long! Platinum (Pt), silver (Ag), and copper (Cu) are next in the list, with copper outpacing the others by an order of magnitude in terms of annual tonnage mined, refined, and manufactured into finished product. In the world of wire manufacturing, copper is king.
Iron (Fe) products like steel and stainless steel are much stronger and harder than the aforementioned metals, and that higher strength translates into lower relative ductility. But steel and stainless steel products are often used for their strength. What’s needed to complement their strength is just sufficient ductility, not maximum ductility.
Other Factors Affecting Ductility
Environmental variables can also have significant bearing on a metal’s ductility. The general rule is that the warmer the temperature, the more ductile the material becomes – just imagine molten metal stretching like bubble gum. The reason for this is that when the metal is heated, there is more thermal energy on the move, which greases the dislocations along the slip planes we mentioned earlier. This allows the metal to undergo much more deformation than it would at colder temperatures. A measurement called the Ductile to Brittle Transition Temperature (DBTT) pinpoints the temperature below which the metal will enter a brittle failure mode. In other words, DBTT marks a temperature range in which metals that would ordinarily extrude simply snap instead. That’s one of the reasons the Eagle Group carries out an extensive APQP for every new part: it’s very important to have a firm understanding of the temperature range in each part’s operational environment.
With a firm understanding of the operating environment and desired mechanical properties, a controlled process of heat treating the metal will ensure the resulting part possesses adequate strength and ductility to perform under the required conditions. Heat treating actually changes the molecular profile of a material, without having to change an alloy’s chemical formula.
Choosing an Alloy for Ductility: What To Expect When Working with Eagle Alloy
Given the plethora of tradeoffs in mechanical properties, it is important for manufacturers to have a realistic idea of what is metallurgically feasible. The inverse relationship between strength and ductility for carbon steels means expectations must match the capabilities of a material. If a customer comes to us with a clear idea of how much strength they require, we can work forward from there to present realistic strength/ductility scenarios. We’ve been doing this for decades, and with dozens of alloy grades in our recipe book, it won’t be difficult to find a material that works. The key is communication: the more you know about your part’s intended use environment and how you want it to perform in the field, the easier it is to advise you on the best alloy to use.
To learn more about metals' mechanical and physical properties, check out our Metal Properties ebook. Fill out the form below to download:
Photo credits: Sigmund419, no changes made. Cdang, no changes made.
https://commons.wikimedia.org/wiki/Commons:GNU_Free_Documentation_License,_version_1.2
Tags: Metallurgy, Metal Properties, Mechanical Properties
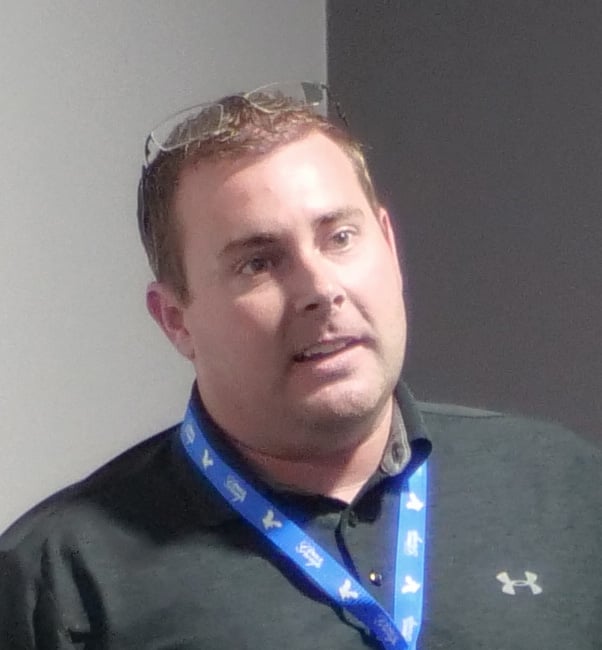
Written by Nic Tarzwell
Nic Tarzwell is Chief Technical Officer at Eagle Alloy, Inc. He has been with the company since 2007.