Nic Tarzwell
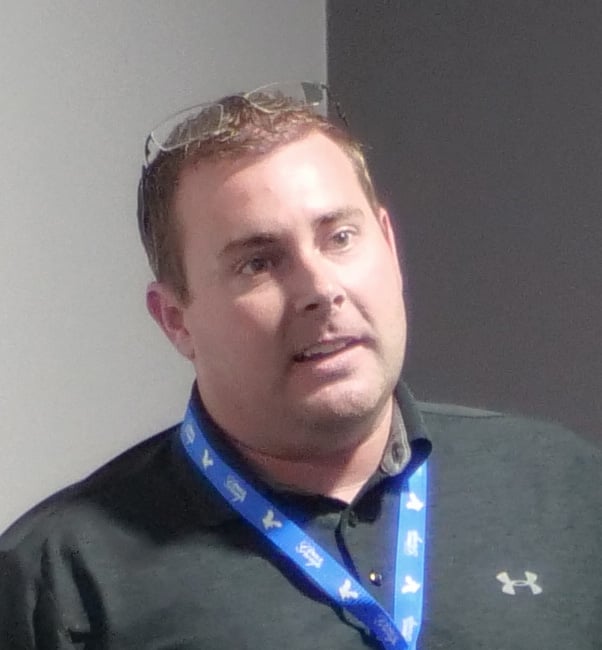
Recent Posts
Metal Properties: Fatigue Resistance
Metal fatigue is the cracking and eventual failure of a metal workpiece under the stress of perpetual loading, a type of continual loading known in the industry as cyclic loading. Fatigue resistance in metal parts is the other side of the coin: it represents a part’s ability to avoid cracking and failure under cyclic loading. Not surprisingly, scientists and manufacturers alike have honed the processes necessary to produce components that resist failure from fatigue as efficiently as possible. Manufacturing parts with the aim of resisting failure from perpetual loading is vital for a part’s longevity in service, and for ensuring that our customers are receiving parts that meet a minimum of expected performance life.
Heat Treatment for Cast Products at Eagle Alloy
Eagle Alloy provides a wide range of metalcasting services. In addition to casting hundreds of alloy grades that can be formed into virtually any castable shape, our foundry is fully equipped to heat treat the majority of parts we manufacture. In this blog, we’ll be opening the doors to our heat treatment facilities. You’ll get to know what kind of heat treat equipment we utilize to deliver superior products that consistently meet performance expectations.
Casting a part into its required shape does not fully prepare it for a life of service – only heat treatment can ensure a part performs exactly how it should. With the exception of a handful of nickel-based specialty alloys, Eagle Alloy heat treats just about every part that is cast in our facilities. From annealing and normalizing to stress relieving and quenching, we have the furnaces, quench tanks, data and expertise to take a product from inception to delivery.
Tags: Eagle Alloy, Metallurgy, Heat Treatment
Introduction to Heat Treatment for Cast Parts
Metal manufacturers utilize a number of tools to control the mechanical and physical properties of raw materials. An alloy’s chemistry is only one part of the equation: obtaining the final properties can only be achieved through heat treatment. In this introduction, we'll cover the following topics:
- Why heat treatment is important for metalcasting
- Heat treatment for carbon steel vs heat treatment for stainless steel
- The importance of using ASTM standards
- Key heat treatment processes used by foundries and machine shops
Heat treatment is a broad term describing a range of thermal processes used to control an alloy’s properties. These processes ensure a finished product carries the mechanical and physical properties demanded by its application. Encompassing both heating and cooling, heat treatment incorporates a few distinct and equally important phases:
- Ramp-up: heating the metal;
- Soak: maintaining the metal at a desired temperature for a specified amount of time;
- Cooling: cooling to a specified temperature at a controlled rate and in a controlled environment.
Tags: Metallurgy, Heat Treatment
Metal Properties: Ductility
Ductility describes a metal’s amenability to being drawn or stretched without breaking. It is one of the crowning mechanical properties of a metal. Without a sound understanding of the science of ductility, manufacturers would be unable to guarantee the safety of their machinery.
In this blog, we’ll explain why manufacturers rely on ductility to guide them in casting parts that uphold integrity in service while protecting machinery against catastrophic failure.
State-of-the-Art 3D Scanning for Cast Products
The Eagle Group Blog previously wrote about our handheld laser scanner, capable of processing 1-2 million individual location points to accurately measure any surface. We recently built on that capability and purchased a Keyence VL-550 3D scanner CMM. The intuitive user interface, proprietary software and raw scanning power of the new equipment means we can process samples faster than ever before. By reducing measurement time and improving ease of use, we also open up a number of opportunities for advanced quality control.
Tags: Product Design, Development, Product Development, Measurement, 3D Scanning
Tooling for Shell Mold Casting
Every metalcasting process has unique tooling requirements. In sand casting, actual molds and cores are expendable, but tooling elements are more permanent. Shell mold casting tooling includes pattern plates, coreboxes, cavities, ejection systems and gating. All of these separate parts come together to allow precise formation of shell molded parts, whether the foundry is doing a run of 100 or 100,000 parts. A variety of metalforming techniques can be used to create tooling for shell mold casting, and the ideal process should strike a balance between quality, longevity and price.