Metal Properties: Hardness
“Hardness” is a concept we use every day to compare objects: fresh bread vs. stale bread, a baseball vs. a softball. In manufacturing the definition is a bit more specific: hardness is a measure of a material’s ability to resist localized scratching or deformation by indentation at a specific loading location.
Our understanding of hardness and relative hardness between materials is key to manufacturing metal products. The correlation of hardness with other mechanical properties also makes it possible for us to predict, with a high degree of accuracy, the strength and ductility of a material without submitting it to destructive testing.
In the world of manufacturing, there are numerous hardness types and measures. In this blog, we’ll talk about how they differ and what role they play in producing metal products.
Hardness Compared With Strength
Similar to strength as a mechanical property, hardness is a measure of how well a material resists deformation. Whereas the deformations we measure with strength are the result of a tensile test, the deformations we measure for hardness are from localized, mechanical indentations or abrasions. Hardness is a measure of how well a material resists deformation when you indent, pierce, hammer, scratch or drop a heavy ball on the same spot, repeatedly. The emphasis is on ‘same spot’: hardness is about measuring resistance to deformation at a specific spot - it is a performance indicator that predicts how well a part withstands localized pressure or abrasion.
The Importance of Hardness in Metalcasting
Most metals are relatively hard. Even softer metals, like lead, gold, or silver, are still considered hard compared to other materials we handle on a regular basis like wood or rubber. But among metals there’s something special, and therefore useful, about hardness: it's a repeatable measurement that says a lot about a part’s other mechanical properties – namely strength and ductility. Hardness is a useful tool in manufacturing environments to quickly qualify material properties because some materials, like carbon and alloyed steels, have a known direct correlation between tensile strength and hardness. And conversely, there is an inverse correlation between hardness and ductility.
Because of these consistent relationships, we can closely approximate a metal’s strength by conducting a hardness test. Along with the mechanical specifications from a chosen material grade, we use hardness readings to infer a great deal about a material’s resistance to external forces. This testing convenience makes it a reliable method to validate the material response to the designated heat treatment cycles. At Eagle Alloy, a casting foundry specializing in shell molding, hardness testing is commonly performed after casting and heat treatment in order to validate that the prescribed heat treatment was effective to produce material within a specified hardness range.
The Importance of Hardness in CNC Machining
Hardness is also an important measure for CNC machining. When a customer orders a part to be CNC machined, we want to make sure the job gets done as quickly and efficiently as possible. The tools machinists use to cut and shape parts wear down over time, and the higher the material hardness, the faster they wear down. Knowing hardness allows Eagle CNC machinists to predict how long a tool will last and what type of tool to use. Having this information also avoids excessive downtime between tool changes and speeds up order delivery.
The Eagle Group’s “Casting to Completion” service motto means that we take into account every step of the manufacturing process when advising on the optimal alloy, heat treatment, and manufacturing process for each machined part. We utilize Design for Manufacturing (DFM) principles to maximize both quality and production efficiency. For example, a product that requires a high degree of machining may benefit from a re-design that brings the cast part closer to net shape. And, conversely, a product that requires less machining can be cast in a harder alloy without resulting in high machining costs.
Click below to download our 47-page ebook on Metal Properties:
Types of Hardness and How We Measure Them
There are three different types of hardness that are important to metal manufacturing: scratch hardness, indentation hardness, and rebound hardness. Materials can have different values across these types of hardness. Depending on the operating environment, any one of them can be a more or less important factor in the ultimate part design.
Scratch hardness is exactly what it sounds like: how well a material maintains integrity when subjected to repeated scratching from a sharp object. Think of a scratch-off lottery ticket: depending on the softness of the material or how hard you rub, the coated layer will come off more or less quickly. Scratch hardness answers the question: if there is constant surface abrasion happening, how long will the part hold out? The Mohs scale is the definitive test for benchmarking scratch hardness.
Rebound hardness is somewhat analogous to the strength measurement known as yield strength. They both draw on a material’s elasticity. Also known as dynamic hardness, rebound hardness measures a metal’s ability to deform elastically (i.e., non-permanently), before it kicks the indenter (or any other measurement tool) back up to where it came from. It’s like a trampoline: how much energy from a pounding or piercing motion can the material absorb without changing shape, and then how well does it return the indenter to the original dropping height? Often, a diamond-tipped hammer is used for measuring rebound or dynamic hardness. This method, called the Leeb Method, is typically dependent on surface preparation and other factors due to the small size of the testing tip. For that reason, the Leeb method is recommended for reference only. For more accurate hardness readings, the indentation method will be used for most metals.
Indentation hardness is the Eagle Group's go-to for measuring hardness. Specifically, we use the Brinell hardness test - it is the test to quickly and accurately determine a material’s resistance to plastic deformation. The Brinell hardness test is an indentation test: a known load is applied to the surface of a material with an indenter of standardized size for a specific amount of time. After performing a Brinell test, we combine the force used in the test, the diameter of the indenter, and the diameter of the indentation to calculate a Brinell Hardness Number (BHN). The BHN is widely used for benchmarking cast materials in the foundry industry, and it’s the method most common for our cast parts. There are also other hardness methods, like Rockwell and Vickers, that use different sized indenters: these are sometimes better suited for smaller castings, like some of the investment parts manufactured at Eagle Precision.
Understanding Different Hardness Tests
The Eagle Group uses the Brinell hardness test because its measurement spectrum suits our part sizes and surface finishes. However, numerous other tests have been developed over the years. The usual variables are: size of the indenter used, amount of force applied, and material type. Other common indentation tests are Vickers, Knoop, Janka, Mohs, Meyer, and Rockwell. Knoop and Vickers can also be used to measure materials that deform under ‘low applied loads’, e.g. materials on the softer end of the spectrum.
It's important to emphasize that the results from different hardness tests don't readily correlate with each other. You should know which test your foundry is using, and make sure they are using the same test consistently.
Clockwise from top-left: Brinell testing machine; closeup on indenter; reference plate for machine calibration; monitor allowing precise measurement of indentations.
Determining Mechanical Hardness for New Cast Parts
If you come to us with a part that isn’t performing properly, the first thing we do is perform a hardness test. Because of the established relationship between hardness and strength, a simple conversion from a hardness reading will give us a very good estimate of a material’s tensile strength: when a part isn’t performing well, it's often because the material strength isn’t what it’s supposed to be.
But if you’re coming to us with an idea for a new part, you might be asking: do I have to specify hardness characteristics when I come to the Eagle Group for a metalcasting job? At the Eagle Group we carry out an extensive APQP process for every new part, during which time we ask a number of questions about a part’s intended use, service environment and mechanical properties. However, specifying hardness isn’t usually necessary: if you tell us how strong or ductile a part must be, we can determine the target measure of hardness.
It’s hard to imagine running a metal manufacturing facility without hardness testing. Being able to easily assess a part’s hardness and strength helps us avoid material waste from destructive tensile testing and minimize downtime from tool wear in CNC machining – both of which help us keep deliveries on schedule. For new products, bringing hardness into the conversation is important if the intended operating environment exposes the part to frequent rubbing, scratching, abrading, or puncturing. Whether your parts have specific hardness requirements or simply strength and ductility requirements, the Eagle Group will put our knowledge of hardness to work in order to produce cast parts that match your specifications.
To learn more about metals' mechanical and physical properties, check out our Metal Properties ebook. Fill out the form below for a free download:
Tags: Metallurgy, Metal Properties, Measurement, Mechanical Properties
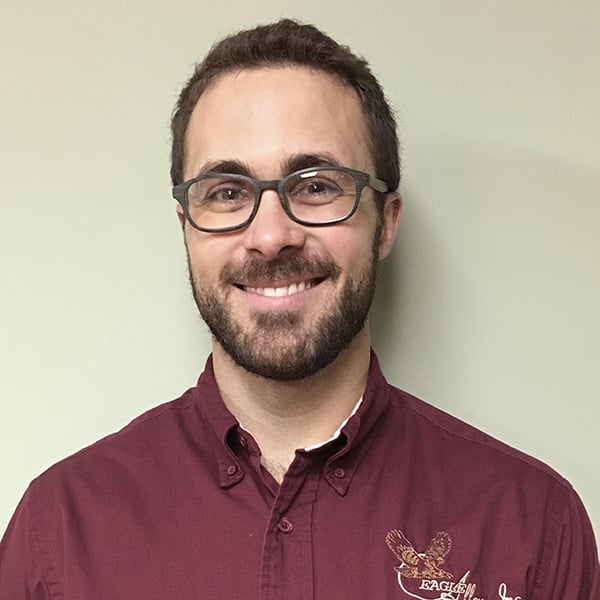
Written by Jason Bergman
Jason Bergman is Senior Quality Engineer and Metallurgist at Eagle Alloy. He has been with the company since 2013.