Deb Pipoly
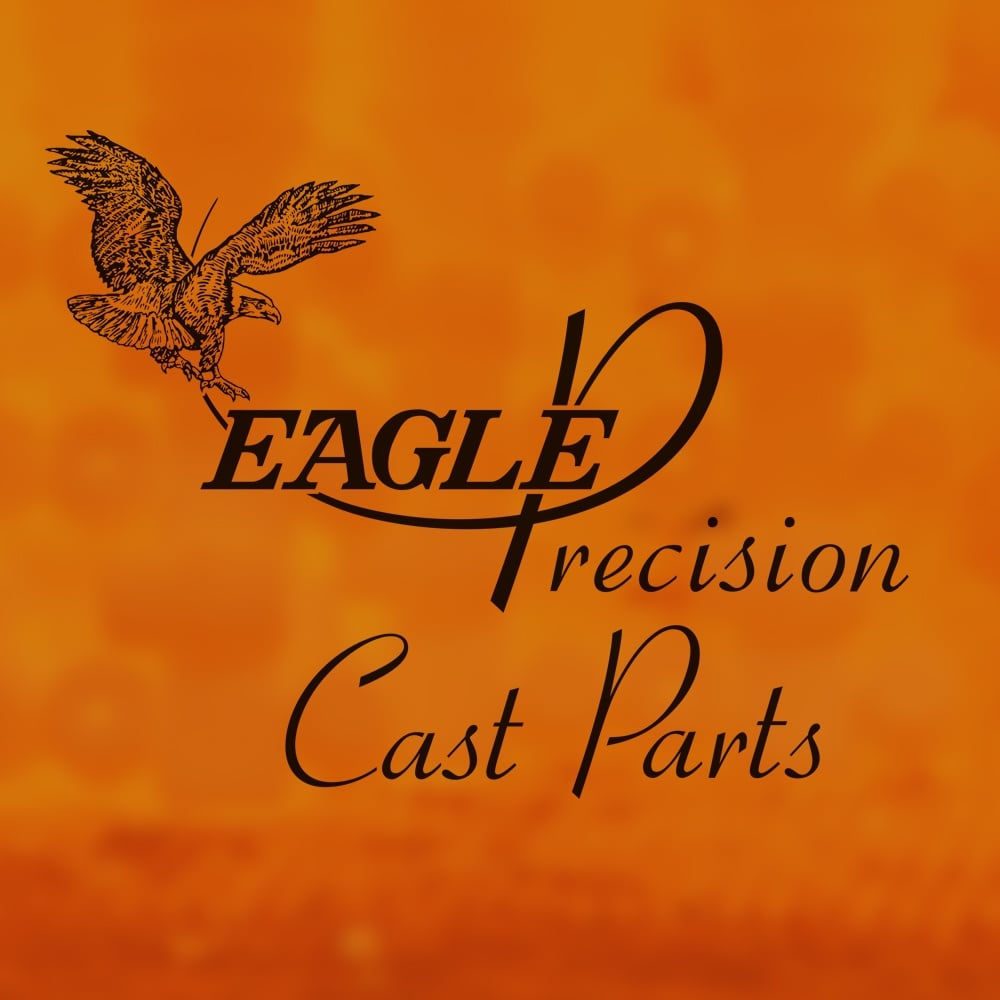
Recent Posts
Continuous Improvement at Eagle Precision: Optimizing the Investment Casting Wax Room
This article is part of our series: Continuous Improvement at Eagle Precision
The wax room is at the heart (and start) of our investment castings. By injecting the wax room with fresh ideas, we’ve been able to greatly improve our pouring efficiency, leading to higher production yields, less downtime, reduced remelting rates, and faster delivery times.
Tags: Lean Manufacturing, Investment Casting, Eagle Precision, Continuous Improvement
Continuous Improvement in Investment Casting
This article is part of our series: Continuous Improvement at Eagle Precision
Continuous improvement is an ongoing effort to make incremental changes in a company’s processes that improve efficiency and quality. While the concept is fairly simple, many businesses find it challenging to sustain continuous improvement over the long term.
Continuous improvement is one facet of Lean Manufacturing, which is a set of tools used to maximize output and minimize waste. The meaning of ‘minimizing waste’ in manufacturing is a far-reaching term. Some examples include:
- Unused material reclamation and recycling
- Cutting down on energy and transportation costs
- Reducing wait times
- Minimizing product defects and returns
Tags: Lean Manufacturing, Eagle Precision, Robotics, Continuous Improvement
Case Study: Converting a Fully Machined Part to an Investment Casting
Manufacturers are aware of the benefits of machining: trained machine shops can produce complex parts with tight tolerances and all critical surfaces to spec. However, many manufacturers are learning that investment casting can produce cast parts to near-net shape, resulting in a host of benefits.
The machining process is often seen as the only way to manufacture a part with highly demanding specifications. Operating under this assumption, manufacturers sometimes choose to machine default without exploring other options. It’s also common for parts to be ‘over-toleranced,’ meaning they’ve been designed with tighter tolerances than the application actually calls for.
Robotics in Investment Casting
Our investment casting foundry, Eagle Precision, makes use of robotics in two steps of the casting process. We started with a robotic dipping cell and expanded into two, followed by a third robotic cell that specializes in after-cast grinding. While robotic cells like these do require a large up-front investment, we’re already seeing company-wide benefits resulting from our use of robotics in investment casting.
Robots are becoming more and more common throughout the manufacturing industry, and investment casting is no exception. According to John Scott, VP of Sales at Buntrock Industries, the investment casting industry is seeing increased demand for robotics for three reasons: “lack of workforce availability, desire for increased process control and productivity, and improved health and safety.”
Tags: Investment Casting, Eagle Precision, Robotics, grinding
Our Experience with ISO Re-Certification
In order to maintain efficient and successful operations in the manufacturing industry, quality control is extremely important. At Eagle Precision, we have developed a thorough quality policy that governs how we do business, from customer onboarding to product delivery. A big part of our dedication to quality is our adherence to ISO standards. Eagle Precision has been ISO certified since 2006, and we recently went through a re-certification process–and passed with flying colors.
Tags: ISO Certification, Eagle Precision
Learn to Speak Our Language: Metalcasting & CNC Machining Jargon
Metal manufacturing professionals are a close-knit community, and just like any specialized group, we've developed our own way of speaking. To outsiders, many of whom are our friends, family and customers, metalcasting & machining lingo might seem like another language entirely. Here, we aim to demystify metalcasting & machining jargon so anyone can join the conversation.
Tags: Metalcasting, Glossary, CNC Machining
Ebook for Manufacturers: Metalcasting & CNC Machining Process Guide
Tags: Metalcasting, Machining, CNC Machining
5 Ways to Tell if Casting Is the Right Manufacturing Process for Your Products
Modern metal manufacturing offers a wide range of choices to bring designs into reality. Metalcasting has been around for millennia, and it's undergone its fair share of innovation over the years. Casting facilities can now handle almost any alloy, and can cast intricate designs with complex inner cavities that wouldn't have been possible even a few decades ago.
Tags: Metalcasting, Manufacturing, Fabrication to Casting, Fab-Casting
CAST IN STEEL: Student Teams Compete to Cast the Best Steel Viking Axe
This year the Steel Founders' Society of America (SFSA) introduced a national competition to engage students with steel casting and help foundries connect with the next generation of manufacturing professionals. Inspired by History Channel's Forged in Fire, the Cast in Steel competition brings teams of engineering students from around the country together to find out who can cast the best Viking axe. Testing, judging and awards took place prior to CastExpo in Atlanta, GA.
Tags: Investment Casting, Eagle Precision, Airset Casting, Event, Student Metalcasting Competition, CastExpo, Trade Associations
Designing Cast Products: 3D Modeling and Solidification Simulation Software
The rise of CAD/CAM software largely defines the current era of manufacturing. While blueprints and dimensional charts are still widely used as reference guides, modern manufacturers rely on software to design prototypes and simulate casting processes. One of the first steps in the cast part development process is to create a 3D model. From there, engineers can improve the part shape, simulate a variety of casting processes and materials, and troubleshoot difficult manufacturing scenarios.
When done right, CAD/CAM software enables foundries to solve all the problems of casting in the virtual world, before pouring any metal. The results are cost savings for the customer, time savings for everyone, and reduction of overall waste.
Tags: Product Design, Development, Capabilities, Inspection, Product Development, Technology, CAD/CAM