5 Ways to Tell if Casting Is the Right Manufacturing Process for Your Products
Modern metal manufacturing offers a wide range of choices to bring designs into reality. Metalcasting has been around for millennia, and it's undergone its fair share of innovation over the years. Casting facilities can now handle almost any alloy, and can cast intricate designs with complex inner cavities that wouldn't have been possible even a few decades ago.
Metal Manufacturing Options
Other manufacturing processes have their own sets of advantages and drawbacks, and some parts do work best with non-casting manufacturing processes. 3D printing, forging, stamping and CNC machining are a few options available to modern manufacturers. Still, metalcasting is often the most efficient manufacturing process in terms of material scrap, man-hours and energy expenditure.
If you're thinking of bringing a metal product to market, or you're looking for a more efficient production method for an existing product, casting might be the right path. When casting facilities use smart planning practices like APQP and employ principles of Design for Manufacturability, the casting process can provide huge benefits to both the manufacturer and the end user.
Improving Quality and Cost Through Metalcasting
To find out if your product would be a good candidate for metalcasting, take a look at the following characteristics, excerpted from our Fabrication to Casting Checklist.
1. The product is composed of multiple components. The more components you need to connect, the more time and money you could save through casting. In cases where multiple pieces need to be welded or fastened together and remain stationary during operation, casting can often provide a single component. Consolidation not only improves aesthetics, but it also improves durability, performance and corrosion over time.
2. You manufacture the product in medium to high volumes. Casting provides a repeatable manufacturing process that uses fewer per-part man hours than most other metal manufacturing techniques. However, tooling costs can be high and the design process, when done right, often requires a significant amount of engineering. Sometimes casting is still the best choice for small runs, but you'll usually find the best ROI for your tooling costs if you're manufacturing products in the medium to high range.
3. The product is not aesthetically pleasing. Let's be honest: even industrial manufacturing is a beauty contest. Even if you're making parts that will never see the light of day, consideration of aesthetics can still increase product value and support product differentiation when competition is present. If you have an ugly part, chances are you can make it prettier through metalcasting.
4. You have a high return rate. If your customers are sending your products back frequently for performance issues, or you're experiencing field failures, it might be a good time to look at a new manufacturing method. Stresses can be introduced to a workpiece during production, and assembling multiple parts can reduce the integrity of an overall product. Casting facilities have a variety of tools at their disposal that allow us to predict the performance of a part long before pouring any alloy, so engineers can work out all the kinks in a virtual environment.
5. Anyone could have made it. Logos, lettering and other unique pieces of flare can easily be added to casting designs, allowing your products to stand out from the competition. Some non-casting manufacturing methods also do a good job of producing detail, but many other methods make it difficult or impossible.
If these descriptions fit your product, there's a good chance you could benefit from casting. At the Eagle Group, we've worked with a number of manufacturers who previously produced fabricated parts and benefitted immensely from making the switch. Consult this case study for an example of how a clunky, expensive part transformed into a sleek, manufacturable part that performed better, looked better and cost much less to produce.
To get an expert opinion on how metalcasting could benefit you and your product, we urge you to consult with a casting facility. The Eagle Group is comprised of three casting foundries and a CNC machine shop, and our experts are available to evaluate your product and offer our honest opinion on its castability. For a free consultation, contact us today.
For a more detailed list of characteristics that make parts good candidates for casting, download our free Fabrication to Casting Checklist.
Tags: Metalcasting, Manufacturing, Fabrication to Casting, Fab-Casting
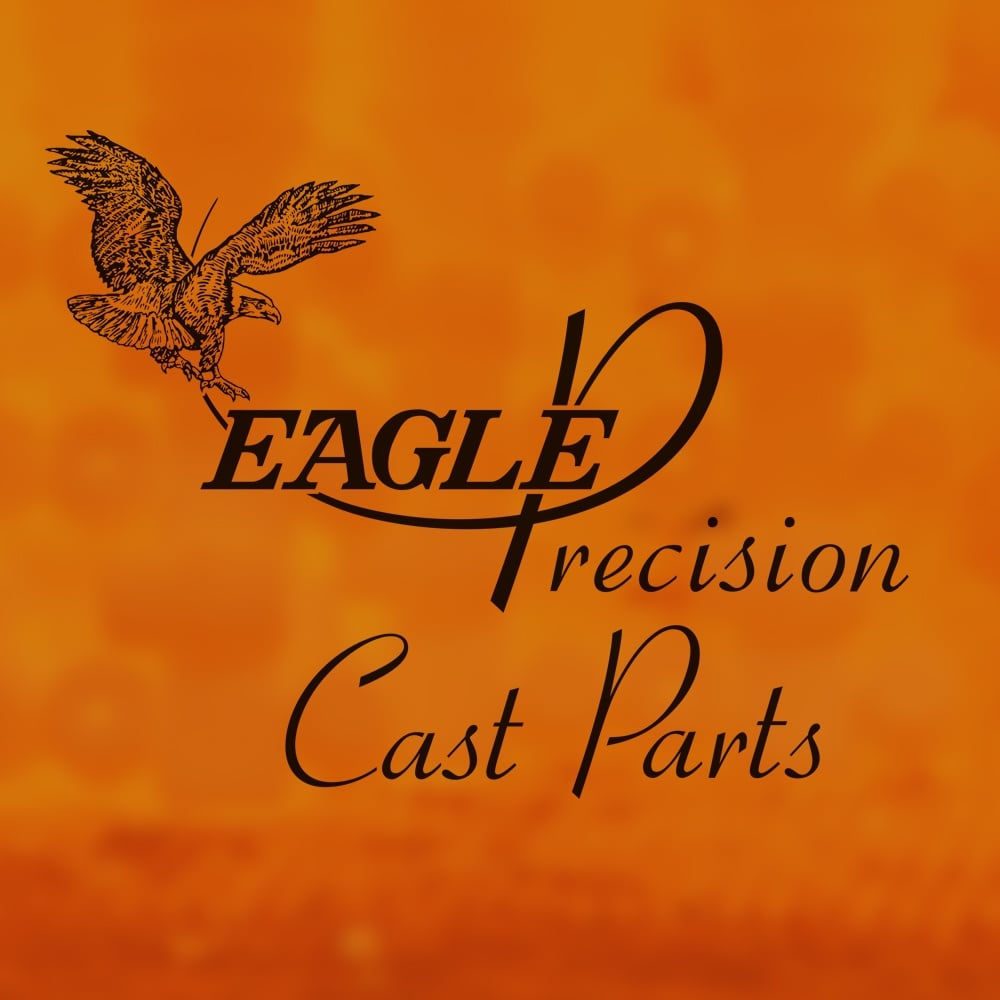
Written by Deb Pipoly
Deb Pipoly is President of Eagle Precision Cast Parts, an investment casting company located in Muskegon, MI.