Robotics in Investment Casting
Our investment casting foundry, Eagle Precision, makes use of robotics in two steps of the casting process. We started with a robotic dipping cell and expanded into two, followed by a third robotic cell that specializes in after-cast grinding. While robotic cells like these do require a large up-front investment, we’re already seeing company-wide benefits resulting from our use of robotics in investment casting.
Robots are becoming more and more common throughout the manufacturing industry, and investment casting is no exception. According to John Scott, VP of Sales at Buntrock Industries, the investment casting industry is seeing increased demand for robotics for three reasons: “lack of workforce availability, desire for increased process control and productivity, and improved health and safety.”
At Eagle Precision we find all these points to be true. By integrating robotics into our investment casting workflow, we’ve succeeded in improving mold consistency, allowed our company greater flexibility, and freed our employees to carry out more complex tasks.
Watch Eagle Precision's robotic cell below: investment casting dipping with robotics
How Investment Casting Dipping Works
Dipping in investment casting is the process of coating a wax pattern with slurry. Several layers of slurry combine to form investment casting molds. The first layer, or primary layer, is the layer that actually touches the molten metal that gets poured into the mold. This layer is responsible for the surface finish of the cast part, so it's very important that the coating is mixed correctly and spread evenly over the wax patterns. The next layers are called backup dips, and they serve to keep the mold strong and hold its shape even through extreme temperature changes.
Standard dipping for investment casting facilities includes mixers and sanders. Operators add slurry components to the mixer and program the mixer to spin at a certain velocity. The mixer then swirls the slurry mixture to keep it smooth and even throughout the entire run. The operator takes each pattern tree from a rack, dips it, allows it to drip excess slurry back into the tank, and then places the tree into the sander. The sander is a horizontal tank that spins and continually drops sand onto the top of the new slurry coating. For most investment castings, this process is repeated to form several hard-shell layers on each mold.
When dipping and sanding are finished, the molds are dried, pre-heated to melt and remove wax, and then poured full of molten metal alloy and left to cool as the alloy hardens into castings.
Eagle Precision's Robotic Dipping Cell
Setting up and Programming the Robotic Cell
Eagle Precision's robotic dipping cell functions in much the same way as a manual dipping cell. The main difference is that the heavy lifting is carried out by an articulated robotic arm. Eagle Precision uses Fanuc robots, which are known for taking on many roles in manufacturing systems. Instead of an operator holding the pattern tree in the mixing tank to cover it in slurry, the robot holds the pattern tree in the tank. The robot then turns the tree above the tank to allow excess slurry to drip off, and transfers the tree to the sander. When the pattern tree is covered in a layer of sand, the robot hangs it to dry in a nearby rack.
However, robotic cells like the one in Eagle Precision require more preparation than manual cells. In robotic cells, human operators must program the mixing tank, the sander and the robotic arm itself. One of the major challenges to expanding robotics in metalcasting is the time and expertise required to create a new program. That's why Eagle Precision divides products into "part families" that can utilize similar dipping programs. That way, programs for several part families can be pre-loaded into the system, and an operator can simply select the appropriate program from the menu and hit "start."
Deciding which part family a new part fits into is one aspect of the detailed APQP process that we complete for every new part.
How the Robotic Arm "Sees" Its Work
Human operators definitely have an advantage when it comes to awareness of their surroundings. Experienced investment casting professionals know how slurry behaves, and they can tell when a pattern tree is sufficiently coated based on sight and weight. They know exactly how many times the tree needs to be turned in the sander, and what it looks like when it's finished. And most importantly, they don't need to be reprogrammed to change how they process a new part family.
Fortunately, robotic arms can be programmed to do more than just move objects around in a cell. They also utilize lasers to "see" the surface of the parts, allowing them to evaluate slurry consistency and the surface of sand-coated pattern trees. Constant feedback from millions of data points feeds into the robotic system, allowing the robot to make on-the-fly adjustments to various program parameters. Advances in technology continually improve these "laser vision eye" systems to make them more accurate and more practical for investment casting applications.
The Benefits of Robotics for Investment Casting
While robotic cells require a lot of up-front investment and setup time, they provide a number of long-term benefits for the foundry, our employees, and our casting customers.
Benefits for customers
First, our robotic dipping cells lead to greater consistency in our molds, and that means fewer part defects. While Eagle Precision's return rate has always been extremely low, those stats are helped even further by automating the dipping process.
Furthermore, our customers benefit from the stability that robotic cells provide. With robotic cells we are better able to measure our capacity in the short and long term, allowing us to predict turnaround times with greater accuracy.
Company benefits
With robotic cells in place, Eagle Precision can now be more flexible with additional demand and limited staff. Manufacturers around the globe are experiencing staff shortages, and the problem will likely get worse. With our robotic cells in action, we're able to increase our casting output even if we're not able to easily grow our staff. As discussed above, we're also able to more accurately predict our company's capacity, even if demand or workforce numbers fluctuate. That ability to predict is key in guiding our company into future investments.
Employee benefits
While employees may see robotics as a threat to their job security, the opposite is actually true. Just as our customers benefit from our stability in terms of casting production, our employees also benefit with more consistent hours, task lists and overtime. Also, as an ESOP company, our employees earn more when our company produces more, so the productivity boost from robotics benefits everyone.
Eagle Group companies take pride in offering employee benefits that go far beyond many manufacturing companies, including on-site health clinics, ESOP, life coaching, and education reimbursement. Any investment in our company is an investment in our employees, and robots are no exception.
Robotic Grinding at Eagle Precision
Following the success of Eagle Precision's investment casting dipping cell, we immediately took action to expand robotics into new areas. Our sister company, Eagle Alloy, already made use of robotic cells for grinding, and now we are doing the same.
Eagle Precision is an investment casting foundry, but our job isn’t over when the parts are poured. Our customers often require after-cast processes, the most basic of which are gate removal and grinding. Our new robotic grinding cell consists of two parts: a Fanuc pick-and-place arm, and a RGS230 Revolving Table Grinder manufactured by AW Bell Machinery, purchased through Buntrock Industries, a company dedicated to providing investment casting facilities (like ours) with materials, equipment and technical support.
Here’s how it works: First, an operator loads a holding table with dozens of parts. The Fanuc arm then picks up and places each part on the revolving wheel, grinds it, then removes and puts it back into place among the finished parts. While the Fanuc arm is picking and placing, the rotary table is continuously moving parts through the grinder. Programmed and synchronized, together they can get the job done faster and more efficiently.
“Cells like these reduce grinding defects,” says John Scott, VP of Sales at Buntrock, “while allowing one operator to utilize multiple pieces of equipment. The overall effect is to increase the number of parts processed per manufacturing hour.” With this setup, suddenly common errors like over-grinding become very uncommon. And even though customer returns are already very rare, Eagle Precision’s customers can expect even fewer returnable precision parts thanks to this new installation.
The grinding cell we ordered from Buntrock is also modular, adding to its flexibility. New components are designed to fit together like legos, making robotic expansion easier than ever. We don't plan to stop here – we still see plenty of places where robots can enhance our operations. For example, we are also exploring options to integrate robotics with our wax department.
The strategic use of robotics is good for our customers, ourselves, and the manufacturing industry as a whole. Whether dipping or grinding, our robotic cells demonstrate our lean manufacturing ethos. They allow us to be more agile in responding to workforce and demand fluctuations, and add to our process-optimization abilities. While the investment casting process is thousands of years old, forward-thinking foundries like Eagle Precision ensure that it remains a viable manufacturing method now and into the future.
To learn more about Eagle Precision's investment casting capabilities, download our spec sheet below:
Tags: Investment Casting, Eagle Precision, Robotics, grinding
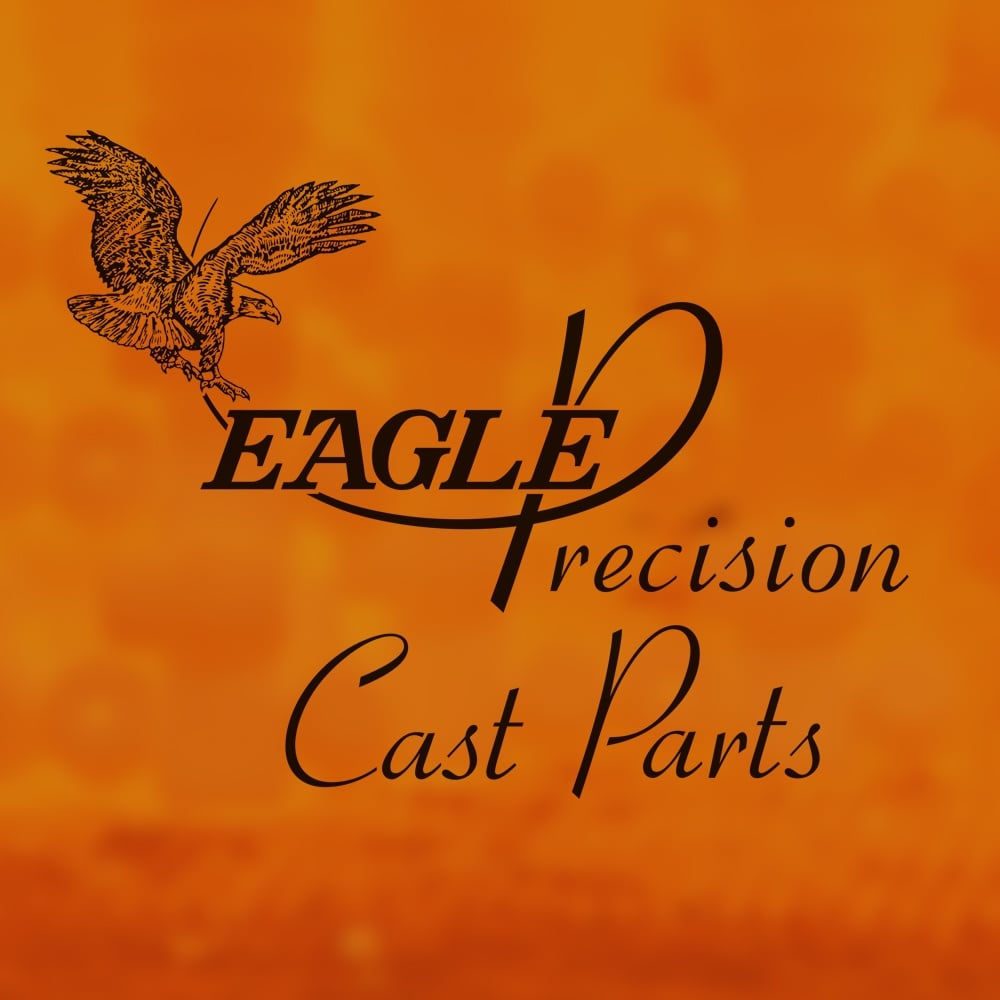
Written by Deb Pipoly
Deb Pipoly is President of Eagle Precision Cast Parts, an investment casting company located in Muskegon, MI.