Continuous Improvement at Eagle Precision: Optimizing the Investment Casting Wax Room
This article is part of our series: Continuous Improvement at Eagle Precision
The wax room is at the heart (and start) of our investment castings. By injecting the wax room with fresh ideas, we’ve been able to greatly improve our pouring efficiency, leading to higher production yields, less downtime, reduced remelting rates, and faster delivery times.
What Does Continuous Improvement Mean in Investment Casting?
Continuous improvement, or the art of making incremental changes to improve production quality and efficiency, is a key tenet of lean manufacturing. It is a never-ending process—every change to a system changes the nature and functioning of the entire system itself. As such, it is a core principle of continuous improvement to be continuously working to identify process variations that could be leading to suboptimal production yields, operational snags and even defects in final products.
In short, a robust continuous improvement program enhances consistency, reduces waste, and ultimately drives higher-quality output across the board.
Continuous Improvement: The Heart of EPCP’s Company Culture
Continuous improvement is happening all the time at Eagle Precision, and for us it’s become a philosophy. “How can we do this better?” is a phrase heard around the shop floor as constant as the whirr of our robotic cells or the drone of our drying room. Moreover, since we’ve become an employee-owned company, that question has taken on new dimensions—when every employee can share in the rewards of efficiency gains, they take the work of identifying process variations to heart.
In addition to the mindset towards continuous improvement as we carry out our usual duties, Eagle Precision Cast Parts conducts regular production audits. A production audit is our systematic review of processes, equipment, materials, and workforce practices to ensure that production activities align with our quality standards and operational goals. During the audit, we assess everything from machine settings and tool conditions to operator techniques and adherence to protocol. This process helps identify inefficiencies, deviations, or potential risks that could impact product quality. By uncovering root causes of potential problems, we can aim our changes at the right targets, rooting out issues at the source.
As an ISO-certified company, production audits are essential—they address the core principle of the ISO 9001 standard of improving performance, meeting customer expectations and demonstrating commitment to quality. Our team has put the infrastructure in place to ensure that data-driven analysis from production cycles helps refine quality control checkpoints and prevent recurring errors.
Our wax room is a prime example of the company-wide dedication to continuous improvement.
Continuous Improvement in the Eagle Precision Wax Room
What is a Wax Room in Investment Casting?
The wax room starts with wax-injection tooling. This investment casting-specific tooling is usually a CNC machined model of the part into which the semi-molten wax is injected to create wax patterns. After the wax is injected into the metal dies, what comes out is a detailed wax replica of the final parts, which are then carefully removed, inspected, and assembled onto a central wax sprue to form a "tree" structure. This assembly will later serve as the foundation for the ceramic shell. For a more detailed look at what happens in the wax room, check out our dedicated blog.
The two main areas of focus in our wax room have been die optimization (improving the ergonomics and efficiency of wax-mold production), and yield improvement (increasing the number of molds we’re able to fit on a single tree).
Die Optimization
Investment casting dies are precision-engineered molds used to create wax patterns in the shape of the final metal part. Because the quality of the wax pattern directly affects the final casting (and wax patterns come from dies), dies play a critical role in ensuring consistency, dimensional accuracy, and surface finish in the investment casting process.
In our investment casting process, continuous improvement plays a central role in how we evaluate and evolve our die tooling. One of the major upgrades we've implemented is transitioning from manual, single-cavity tools to semi-automatic, multi-cavity tools. Previously, operators had to manually disassemble the die, remove wax patterns, reassemble the die, and reposition the die for each cycle. This was time-consuming, labor-intensive, and introduced unnecessary risks. Now, with our upgraded clamp-in multi-cavity tools—featuring built-in ejection systems—the process is faster and more reliable. The machine automatically opens the die and lifts out the wax patterns, significantly increasing production rates, reducing handling time, and improving overall equipment efficiency.
→Learn more about how investment casting tooling works in this post
Improvements don’t just come from machinery—they start with people. A recent example involves an operator who, during a production audit, expressed frustration with a specific die that required excessive manual manipulation using seven separate slides (slides are mechanical inserts in the die that allow for the creation of more complex geometries and for removing the finished wax pattern without damage). By conducting a simple on-the-floor audit and working directly with our toolmakers, we re-engineered the die to function with just two slides, eliminating the need for manual maneuvering. The redesigned die is not only easier to operate but also more ergonomic and far less error-prone. This kind of feedback-driven problem-solving ensures our tooling evolves in line with real-world shop floor needs.
“It's just a much more efficient way of producing patterns,” notes AJ Menefee, VP of Technical and Engineering, “especially if we're going from a one cavity manual to a two cavity or four cavity semi-automatic tool. The result is that our production rates jump up dramatically. It reduces the amount of time that the die is being run on the press, it reduces labor hours on that particular job and reduces the risk of die damage.”
This approach now informs how we assess every potential issue in our wax room. We ask: Can this or that be simplified? Can we eliminate unnecessary steps, slides or manual processes? By applying continuous improvement principles across our tooling, we haven’t just been fixing inefficiencies—we’ve been building smarter systems that enhance productivity, and protect our people and equipment.
Yield Improvement
Recent improvements in our investment casting process have focused heavily on yield enhancement, a strategic shift that's delivering measurable gains in both efficiency and cost savings. One of the key advancements has been reducing the weight of the gating system, or the "tree" structure to which we attach the molds that will create individual parts. By engineering lighter gating components, we’re able to decrease the overall weight of the tree without sacrificing structural integrity, all while increasing the number of castings per tree.
For example, in a traditional setup, a tree might support six castings at one pound each, with the gating system itself weighing 20 pounds—bringing the total weight to 26 pounds. With our redesigned systems, we’ve been able to reduce the gating weight to 15 pounds and simultaneously increase the number of castings per tree by 50%. This not only boosts the yield per tree but also results in less excess material, which means less metal needs to be remelted after each pour. This optimization translates directly into higher pouring efficiencies. As AJ points out, “doing things this new way results in less material that we have to remelt, so it significantly improves our pouring efficiencies.” Pouring efficiency is the ratio of the weight of good, usable metal castings over the total weight of metal poured, and it is a critical benchmark for overall foundry efficiency.
With less metal dedicated to gating and more allocated to usable parts, we reduce energy consumption, streamline post-processing, and lower overall material waste. Ultimately, these improvements help us operate more sustainably while delivering better value and faster turnaround times to our customers.
At the end of the day (or the end of the run), the progress we've made in our wax room isn’t about any one innovation or any one person—it’s about the consistent application of our continuous improvement mindset. From optimizing die functionality and wax tree design to refining operator interaction with the tooling, these changes are the product of a culture committed to doing better—a culture exemplified by our employee-ownership principles. Our team doesn’t stand idly as problems cement and become chronic —we observe, question, experiment, and implement solutions proactively.
At Eagle Precision, our wax room is a prime example of the power of embedding continuous improvement deep into our operational mindset. It ensures that every person, every tool, and every process is aligned toward a single goal: producing the highest quality castings as efficiently as possible. The results speak for themselves—greater yields, less waste, a more stimulating working environment, and a production line that’s not just running, but improving.
To learn more about how Eagle Precision Cast Parts utilizes continuous improvement to optimize investment casting processes, check out our other posts in the series.
Tags: Lean Manufacturing, Investment Casting, Eagle Precision, Continuous Improvement
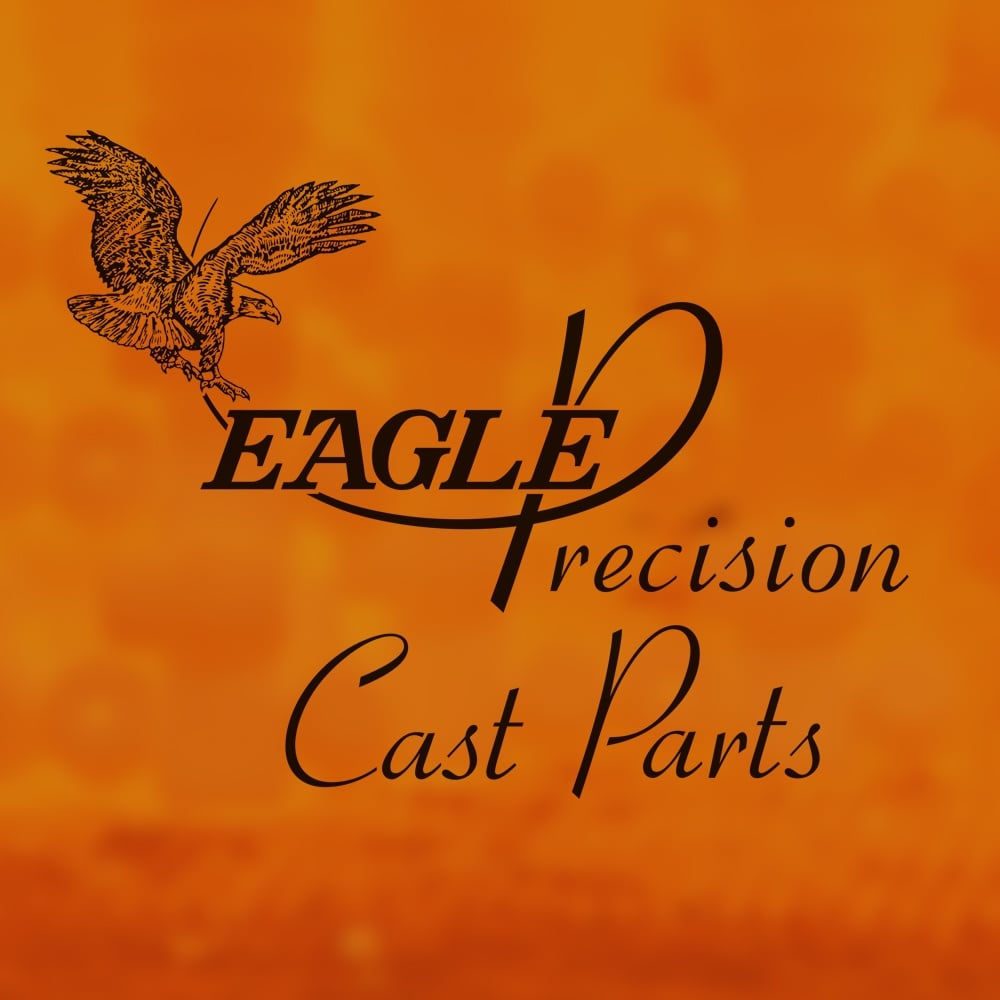
Written by Deb Pipoly
Deb Pipoly is President of Eagle Precision Cast Parts, an investment casting company located in Muskegon, MI.