Heat Treatment in CNC Machining
In this article, we’ll discuss how experienced machine shops like Eagle CNC think about the complex relationship between heat treatment and machinability. Determining where heat treatment fits into the CNC machining process is a vital consideration for machining parts to net shape quickly and cost-effectively.
Eagle CNC is the Eagle Group’s state-of-the-art machine shop, specializing in CNC machining of both ferrous and nonferrous castings, forgings, bar stock and burn outs. At Eagle CNC, we machine new parts directly from raw stock, or from parts that have been shell cast or investment cast by our sister companies, Eagle Alloy and Eagle Precision. While our workpieces start in a variety of states, nearly every product we machine undergoes heat treatment before delivery.
An Eagle CNC-machined product is only finished when its dimensions are cut to spec and its mechanical properties are properly adjusted to its operating environment. In order to achieve the required mechanical profile, proper heat treatment must be conducted at one or more points along the road from raw material to finished product. When heat treatment is built into the overall Design for Manufacturability strategy, customers are much more likely to get the best product at the lowest cost.
Machinability and Material Hardness
A thorough understanding of the relationship between material hardness and machinability allows machinists to minimize lead times and tooling costs.
The decisive mechanical property in determining when and how a machined part should be heat treated is hardness. In material science terms, hardness is a material’s resistance to local scratching and deformation. In CNC machining terms, it’s basically a measure of how often we will have to replace cutting tools and tool inserts in order to machine the material down to net shape.
Machinability, on the other hand, is a measure of how easily material can be cut away from a workpiece to leave only the desired part shape. Machining is a type of subtractive manufacturing because we take a larger piece of material and ‘subtract’ portions by carving them out to arrive at the final form. Machinability is roughly equivalent to softness: if a material is more machinable, it’s usually because it’s softer and therefore easier to cut through. Conversely, the harder a workpiece is, the more difficult and expensive it will usually be to machine it. When we begin work on a part, its machinability depends on its alloy and on the processes it’s been through before it reaches us.
When to Machine: Before or After Heat Treatment?
Many parts come through our doors pre-heat treated, meaning they have been heat treated prior to arrival.
Machining Pre-Hardened Material
Pre-heat treated material is already hardened, often through both alloying and heat treatment. Working with pre-hardened material has a clear-cut purpose: maintaining the highest level of accuracy and the tightest tolerances possible. Machined parts carry a lot of tight-tolerance sections and individual features that are unachievable via casting alone. Heat treatment inevitably involves a small degree of thermal expansion, and even after cooling, dimensional differences can stick around. Because these differences are small they can be acceptable for some cast parts – but they are usually unacceptable for critical surfaces of precision machined parts. In short: some parts must be machined after heat treatment to avoid dimensional distortion.
For example, one of the parts we machine, Hydrant Guard valve plates, are made from 17-4 stainless, which is 5-6x stronger than 316 stainless after heat treatment. “That makes it a lot harder to machine,” points out Nik Seyferth, President of Eagle CNC Technologies. But Hydrant Guard’s valve plates require a high degree of precision to perform in the field, and thermal expansion could take the part out of its required tolerance range. In this case, the best option is to machine the part after hardening.
Learn more about how the Eagle Group manufactures Hydrant Guard check valves in this case study.
Using Heat Treatment to Save on Machining Costs
Tooling costs are one of the largest line items affecting final part price in CNC machining. For customers wishing to keep tooling costs to a minimum, heat treatment can be a solution. The most common form of heat treatment used make material more machinable before the intensive CNC work begins is known as annealing.
Eagle CNC will sometimes recognize a part whose profile doesn’t require it to be machined in a hardened state, and could benefit from pre-machining heat treatment. This usually means employing thermal processes to soften the part. “If it looks like we could process a part in a more machinable state, we’ll reach out to the customers and ask if that’s a possibility,” Nik says, “because sometimes it’s worthwhile to double check a part’s original design to ensure tooling costs are optimized.”
Furthermore, some materials are more thermally stable than others. If the part is made from one of these grades, there’s a better chance that it can be machined in a softer state and then hardened after machining.
Starting with a part in a softer, more machinable state allows the milling machines, lathes, saws, broaching machines, and boring machines to do their jobs of removing metal with much less resistance. For example, if a part design is highly complex and requires multiple machining steps, it’s often best to work with a softer material from the get-go because a more machinable material broadens the scope of machining processes that can be utilized.
When parts arrive at Eagle CNC hardened and pre-heat treated, we make it a priority to communicate to the customer which processes can be utilized. While it is possible to machine very hard materials, exceptional hardness limits the number of machining methods strong enough to carry out machining operations. In cases like this, Eagle CNC will work with the customer to make sure these restrictions are clearly understood: often, only milling or grinding can be used to machine a part after intense hardening. We will also need to use harder bits, more cutting fluid, lower cutting speeds, all while optimizing cutting feed and cutting depth.
Common Post-Machining Primary Heat Treatments
Post-machining heat treatment refers to heat treating a finished part to bring out its final mechanical properties – usually, this means hardening it (if it’s not already hardened, or hardening it again if it’s been softened to a more machinable state) and relieving internal stresses that result from the machining process.
Machining jobs are intense mechanical operations and, as such, machining leaves behind residual stresses in the fabric of the manufactured material. Stress relief is used to stabilize these stresses, ensuring uniform mechanical properties across a specific section. Stress relief is industry standard: it is a widely used heat treatment performed on the majority of parts to ensure proper performance before shipment.
As discussed above, if we have machined a part in a softer state, it will often need to be hardened before it is stress relieved. There are numerous ways to harden a part (head here for an in-depth look at hardening), but a standard hardening process involves heating the metal above a critical transformation temperature for a designated period of time, then removing it from the oven and quickly cooling it by quenching.
For some orders, we take a hybrid approach that incorporates machining both before and after a heat treatment: we start with a softer material and conduct a preliminary machining job on the workpiece. This is called ‘roughing’ the piece, which generally means machining it to within .002-.005” of final dimensions. We then heat treat the piece to harden it before circling back to apply the final touches.
Secondary Heat Treatments after Machining
Hardening and stress relief are considered integral steps in the manufacturing process, and so they are seen as primary heat treatments – part and parcel of any responsible manufacturing work. There are, however, secondary heat treatments which are intended to enhance a part in particular ways.
Case hardening is a common secondary heat treatment process conducted after the machining job is done. It’s effectively the metallurgical equivalent of baking bread with a nice crusty exterior and a soft interior. Case hardening a metal produces a wear-resistant outer layer while still allowing for a more ductile material interior. A good example of a steel that calls for the whole lineup of heat treatments discussed above is tool steel. The manufacturing process for tool steel is complex and often involves machining, hardening, quenching, stress relieving and case hardening.
Induction heat treatment, or localized heat treatment, is another common form of secondary heat treatment. The furnaces used in induction heat treat operations are smaller and work by a different thermal process than large ovens, like car bottom furnaces that uniformly heat all pieces belonging to a batch. Induction heating furnaces are smaller and permit targeted heating (usually hardening) of particular sections of a workpiece by electromagnetic induction. Drive shafts are a good example of a part requiring localized treatment: the spline teeth are often the only part that need to be really hard. An induction furnace can harden just the teeth after machining, leaving the rest of the part in a more ductile state.
Want an in-depth guide on essential heat treatment processes for metalcasting and CNC machining?
Click below, fill out a brief form, and get your free 40-page ebook instantly.
CNC Machining and Heat Treating at Eagle CNC
Many of the orders we receive at Eagle CNC come with heat treatment instructions. Our customers often use both industry standards and trial and error to arrive at the best way to manufacture their product. In these cases, Eagle CNC follows machining and heat treatment instructions provided, working with external partners to handle heat treatment processes that we don’t do in-house.
In the case of a newly designed part, customers usually fall back on industry wisdom by referencing a manufacturing standard. If desired, we can provide additional advice to improve machinability and bring a part to completion in the most efficient way possible. At the Eagle Group, we are proud to have a team of metallurgy and engineering experts ready to provide valuable input in case you’re unsure how best to go about heat treating your new product.
With the entire spec in hand, including heat treat orders, we get to work. The Eagle Group’s in-house heat treating facilities are extensive, and many parts are taken from inception to completion right here within the Eagle Group family. Of course, that isn’t possible for every single part. For specialty heat treatment operations, we also work closely with West Michigan heat treatment facilities Hansen/Balk Steel Treating Company and State Heat Treating Company. The close proximity of these partners helps make our supply chain direct and dependable: we can truck material between facilities in less than an hour.
There is no single heat treatment plan that suits all machined parts. Instead, the goal with each part is to minimize costs and maximize product quality. A comprehensive Design for Manufacturability plan will ensure both of these goals are met.
Learn More About Heat Treatment in Our Dedicated Series
Tags: CNC Machining, Eagle CNC, Metallurgy, Heat Treatment
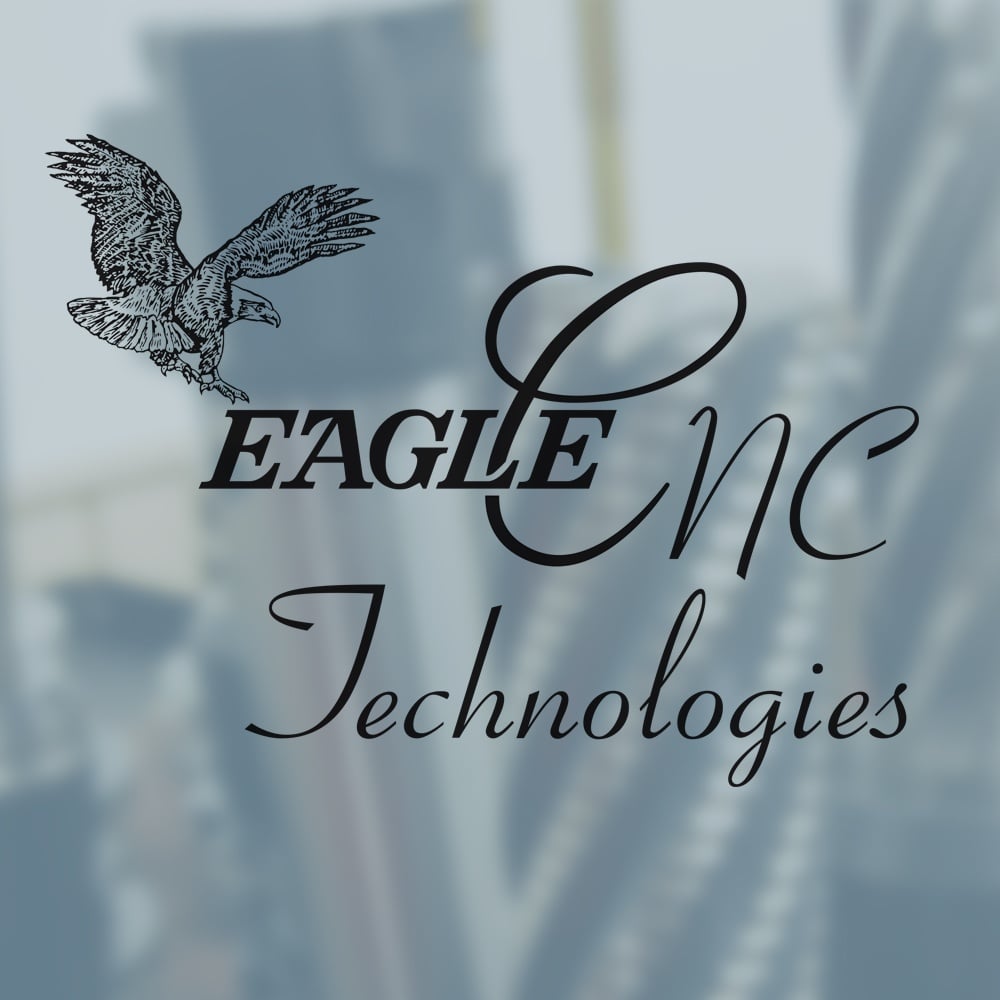
Written by Bill Seyferth
Bill is President of Westech Corporation, the state-of-the-art machine shop that merged with Eagle CNC Technologies in 2007. He founded Westech in 1984.