Metal Properties: Fatigue Resistance
Metal fatigue is the cracking and eventual failure of a metal workpiece under the stress of perpetual loading, a type of continual loading known in the industry as cyclic loading. Fatigue resistance in metal parts is the other side of the coin: it represents a part’s ability to avoid cracking and failure under cyclic loading. Not surprisingly, scientists and manufacturers alike have honed the processes necessary to produce components that resist failure from fatigue as efficiently as possible. Manufacturing parts with the aim of resisting failure from perpetual loading is vital for a part’s longevity in service, and for ensuring that our customers are receiving parts that meet a minimum of expected performance life.
What Causes Failure from Fatigue?
Fatigue is brought about slowly through repetitive or continuous loading exerted on a part. Metals eventually fail from fatigue because a small load applied cyclically and repetitively over time will eventually push the material beyond the limits of its structural integrity. Small loads add up over time, and fatigue resistance is a measure of how long a part can hold out under regular operating conditions.
Because parts can fail in numerous ways, it’s important to outline the distinction between sudden failure and fatigue failure. When we talk about sudden failure under a large and rapidly loaded stress, it’s a metal’s yield strength that’s responsible for saving the part from catastrophic failure. Yield strength is the point after which a material begins to plastically deform and will not return to its original shape after the load is released. The important distinction between yield strength and fatigue resistance is the magnitude of the stress applied in cyclic loading: the level of stress that causes fatigue failure is much lower than a metal’s yield strength. Yield strength measures how much a part can withstand from a single, heavy blow, whereas fatigue resistance dictates how many small loads, applied in cycles, the part can withstand before failing.
Cyclic Loading
Cyclic loading is defined as any type of load that is applied to a part or component and that repeats in a more or less predictable pattern. Think of a crane repeatedly lifting the same weight, or a machine part bearing the brunt of vibration due to normal operation, or even people walking on the same floor for decades. Cyclic loading is subtle but deadly over time, and manufacturing fatigue resistant parts is essential to safety and performance.
The Propagation of Cracks: Fatigue Failure
Fatigue is the name given to the initiation and propagation of cracks in a material due to cyclic loading, and fatigue failure is just that: failure from the propagation of cracks.
Because of the creeping nature of these crack attacks, their propagation passes through a few phases of increasing degradation: first, micro-cracks begin to appear, usually tending to concentrate on vulnerable geometric features like edges. As more cyclic loads are applied, the cracks begin to grow. Finally, the cracks reach a critical size where they begin to cause rapid crack propagation across the entirety of the piece.
What Factors Can Accelerate Fatigue Failure?
Because of the microscopic size of the initial cracks. fatigue failure can often go unnoticed up until the moment it’s too late. And although responsible manufacturers are constantly testing their workpieces for fatigue strength (which we discuss next), there are environmental variables that can compromise even the most carefully designed workpieces. These variables are the same that affect other mechanical properties: temperature and pressure fluctuations; corrosion; and exposure to vibratory or other wear-and-tear environments that cause axial stress. In fact, even a part’s geometry and how it fits into a structural design can also cause problems if proper due diligence is not carried out during the design stage.
Measuring Fatigue Resistance
In metalcasting, we build fatigue resistance through a deep understanding of metal fatigue, and two metrics allow us to quantify it: fatigue limit and fatigue strength.
Fatigue Limit
A fatigue limit is defined as the stress level below which an infinite number of cycles of loading can be applied without inducing fatigue failure. The caveat to this definition is that it describes a material’s resistance to failure under ideal conditions. Once we take field conditions into account (corrosion, temperature fluctuations, vibrations caused by the operating environment), as well as economical and practical considerations, fatigue limit becomes a more or less theoretical concept. In reality, there is no such thing as a part that lasts forever. While fatigue limit is important as a way of comparing various alloys, the practical importance of fatigue strength often takes precedence in manufacturing.
Fatigue Strength
The ASTM defines fatigue strength as ‘the limiting value of stress (denoted by SNf) at which failure occurs after Nf number of load cycles.' In layman’s terms: fatigue strength measures how many cycles a part will last under a given value of stress. Stated differently, a metal’s fatigue strength is its ability to hold its integrity and resist cracking through cyclic loading of a defined stress value.
Fatigue strength is a more practical measure than fatigue limit. The reality is that cast parts in the field are often subjected to loads above the fatigue limit, so they will not last through an infinite number of loadings. We aim to produce cast parts with high fatigue strength (meaning, with high resistance to failure), but not with a perfect resistance to failure because casting parts in this way is inefficient and unrealistic in most scenarios.
Testing for Fatigue and Fatigue Resitance
Here, we discuss the various testing methods used to determine a part’s resistance to cyclic loading. This knowledge helps metalcasters and customers predict when a part will need replacement before it reaches a point of no return.
Destructive Fatigue Testing
Cast and machined metal parts in the field are often safety-critical, so there is no substitute for simulating operating conditions and subjecting a workpiece of a given material and a given geometry to a real-world analysis.
These types of tests are known as coupon tests (here, coupon is just another name for ‘sample’). In other words: take a sample of the proposed part and simulate field conditions under a variety of scenarios. A graph is then plotted that demonstrates how many cycles a part can withstand at given stress levels before failure.
Non-Destructive Fatigue Testing
Most commonly used in manufacturing, non-destructive fatigue testing (also known as NDT) refers to a set of methods of detecting micro-cracks without subjecting the parts to destructive forces. In this way, manufacturers can verify a large percentage of a batch of parts without scrapping the test samples. At the Eagle Group, we often use mag particle or x-ray testing in order to detect the presence of microscopic cracks. Regulations and customer specifications may require NDT to be performed on a certain percentage of parts, depending on the application. In the automotive industry, for instance, it’s common for every single individual part to be non-destructively tested if they are deemed safety-critical.
Mag particle inspection at Eagle Alloy
Designing Fatigue Resistant Parts
We know how to measure fatigue resistance, and we know how to test for it, but how do we improve fatigue resistance in cast and machined parts? The answer is similar to how we approach other metal properties like strength and ductility: using standards, testing and experience to guide material selection, part geometry and post processing.
Material Selection
There is a large body of knowledge around fatigue strength of the various industrial metals, so very often the parts’ end-users will have already conducted their own FEA (finite element analysis) testing, destructive testing and landed on the optimal material for the job. In the words of Eagle Alloy metallurgist Jason Bergman, “Once we have a data set and we know what the material is capable of, we can start putting in the design or the part-specific requirements.” It all starts with selecting the right material, and although material selection is often customer-led, foundries like Eagle Alloy and Eagle Precision are material experts with a deep understanding of fatigue’s effect on the alloys they pour. It’s therefore common practice for an OEM and foundry to work together in selecting the optimal material. From there, it’s the foundry’s job to make sure the material is cast and manufactured under the most stringent quality control requirements. Jason continues: “From a material side, we have to control the gating, rigging, and quality and process control so that we give them the best possible part to help with this fatigue application.”
Geometry
Improper geometry can cause fatigue failure to happen unexpectedly. Like many other aspects of the design process, geometry is often customer-driven, meaning the geometry has should have already been tested for fatigue resistance before it reaches the foundry. However, it is also common for foundries and customers to combine their expertise in drafting improvements to part designs. Whatever approach is taken, the principle remains the same: various part geometries have to be modeled and tested to ensure there are no sections that are capable of concentrating unwanted stress.
“I have this material,” Jason summarizes, referring to the relationship between material selection and geometry, “but I have the material in this shape. What is this capable of?”
Heat Treatment
A proper heat treatment plan is vital to any part design, and goes hand-in-hand with material selection. Especially in the case of carbon steel alloys, heat treatment plays a major role in determining the alloy’s mechanical properties. As a concept-to-completion manufacturer, the Eagle Group is able to discuss all heat treatment options as well as apply the treatment to most parts in-house.
Because fatigue failure results from uncontrolled microscopic stresses, properly stress relieving materials is paramount to the production process. Without using one of the stress relieving methods such as normalizing or tempering, the metal will contain too many residual stresses, creating a breeding ground for the propagation of cracks.
For a deeper dive on heat treatment and its role in metalcasting and machining, check out our dedicated series.
Fatigue resistance is a critical property in the design and manufacture of metal components, ensuring their longevity and reliability under cyclic loading conditions. As a mechanical property, fatigue resistance is incredibly important for cast and machined metal parts, as it has a direct relationship to each part’s longevity and safety. Collaboration between foundries and customers is essential in selecting the best materials and design practices to produce parts that withstand the rigors of real-world applications. By continuously refining these processes, manufacturers like the Eagle Group can deliver high-performance, durable components that meet stringent safety and performance standards.
To learn more about metals' mechanical and physical properties, check out our free, 47-page Metal Properties ebook:
Tags: Metallurgy, Metal Properties, Mechanical Properties
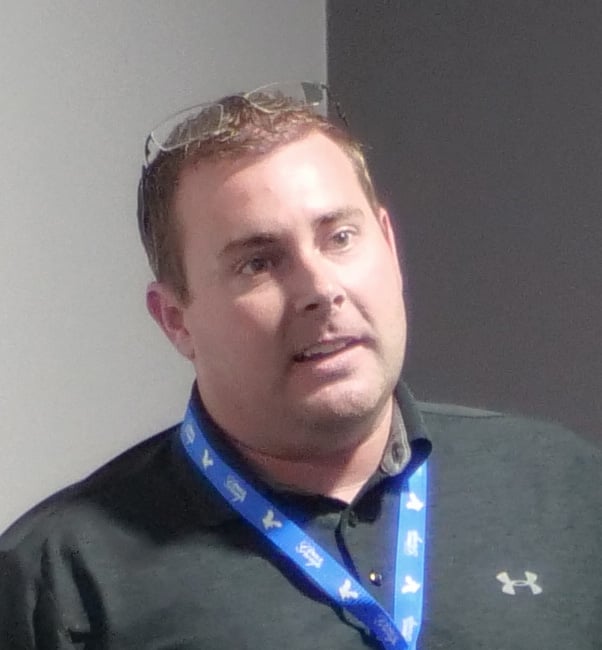
Written by Nic Tarzwell
Nic Tarzwell is Chief Technical Officer at Eagle Alloy, Inc. He has been with the company since 2007.