What Precision Machine Shops Do: Introduction
Our new blog series What Precision Machine Shops Do focuses on the processes, equipment and knowledge involved in modern machining. We'll take a close look at key metal removal techniques like milling, turning, facing, boring and tapping, along with the many products and parts that work as a result of these processes.
For the most part, we'll be discussing CNC machining, or Computer Numerical Control machining. For a brief introduction to CNC, explaining how it developed and how it differs from non-CNC machining, check out our Introduction to CNC Machining blog post.
What is Machining?
Machining, at its most basic level, is the removal of material to create a specific design. Additive manufacturing, like 3D printing, does the opposite: it brings material together to form a product.
In the world of manufacturing, cast parts are rarely ready to go right out of the mold. Machine shops are often tasked with machining cast parts to ensure that they meet requirements for shape, design and accuracy. Machine shops also implement uncastable characteristics.
Machine shops are capable of manufacturing products directly from raw materials, but machining-only workflows can result in excess material waste. In the world of metal manufacturing, casting often gets the ball across the court and machining scores the slam dunk.
What Do Precision Machine Shops Do?
The following standard machining processes are among the most common techniques used by machine shops today.
- Turning: Rotating the workpiece to bring metal in contact with the cutting tool. Lathes are often used for turning.
- Milling: Rotating a cutting tool to bring it into contact with a stationary workpiece. Milling machines are used for milling.
- Drilling: Creating, or refining, holes by bringing a rotating cutting tool into contact with the workpiece. Milling machines or lathes are often used for drilling.
- Boring: Removing material to form, or refine, highly accurate and precise inner cavities in a workpiece. Boring can be performed using a lathe or a milling machine, or a specialized boring machine.
- Sawing: Cutting a narrow slit in a workpiece, using a saw blade as a cutting tool. Saws or Sawing machines are used for sawing.
- Broaching: Removing material through a series of shallow cuts, using a tool with many teeth of ascending height. The cutting tool is called a broach and is used in either a lathe or a broaching machine.
- Grinding: Bringing a workpiece in contact with a rotating abrasive surface to smooth, or alter the shape of, a surface. Grinding machines are used for grinding.
Within these standard methods are a broad range of more specific applications. Milling machines and lathes can be used for facing, or finishing a planar surface. Tapping and reaming are ways to finish holes, whether they're drilled, bored or cast. Tapping creates threads to correspond to a screw or bolt, and reaming widens a hole to a specific diameter. 5-axis machines perform actions comparable to milling machines, lathes and drill presses, but are capable of controlling pitch and yaw of the workpiece (or the tool) as well its XYZ motion.
The following modern machining processes can be found in state-of-the-art machine shops, and require very specific equipment. While their fundamental goal is the same–the removal of material–they act on workpieces in novel ways.
- Plasma cutting: cutting metal with a plasma torch, made up of compressed gas and electrical arcs.
- Water jet cutting: reserved for very hard materials, like granite and some metals, water jet cutting sprays wanter onto the workpiece at high pressure. Sometimes the water is mixed with abrasive materials, like sand.
- Electrical discharge machining (EDM): not to be confused with the other EDM, this machining method material is removed by passing a strong electrical current between two electrodes on the workpiece.
Stay tuned to the Eagle Group Blog for detailed information on all these processes (and more) in our What Precision Machine Shops Do blog series.
Learn more about CNC equipment and techniques from our free ebook, the CNC Machining Process Guide
Tags: Machining, CNC Machining, Eagle CNC, What Precision Machine Shops Do
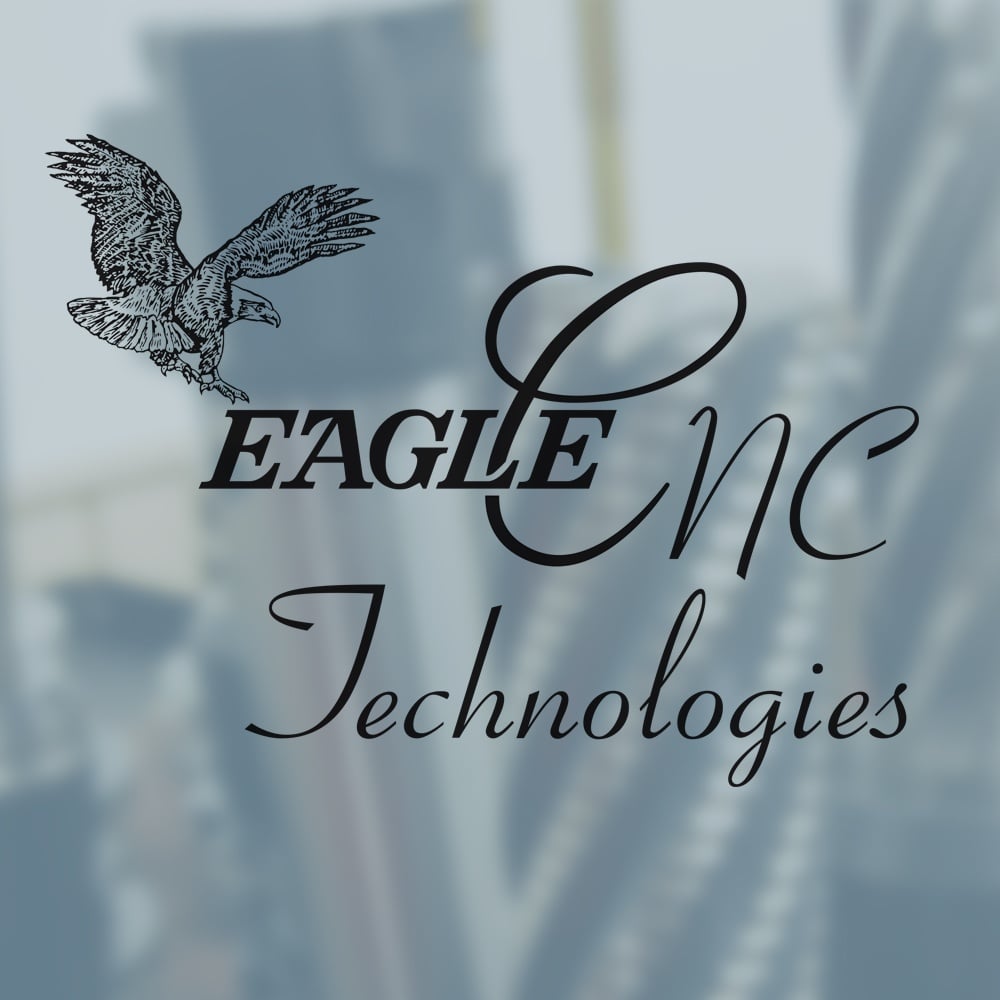