Casting Aluminum: Comparison of Methods
Aluminum can be shaped through a wide variety of process, including:
- Casting
- Extrusion
- Forging
- Rolling
For any type of metal, casting is arguably the most versatile of all of the forming processes, and results in the greatest variety of parts. In fact, the US Department of Energy estimates that over 90% of all manufactured goods contain metal cast products.
The same casting techniques used for other metals can be applied to aluminum, but some of the most popular methods used with aluminum are permanent mold casting, greensand casting and die casting.
Permanent Mold Casting
Permanent mold casting involves creating a reusable mold from metal with a high melting temperature. If aluminum is being cast, the mold is often made from gray iron or steel. Two halves of the mold are connected and then pre-heated. Molten metal is poured in from a ladle to fill the mold, and is allowed to set until sufficiently solidified to remove the casting. In most cases, the casting is removed to cool as soon as it’s solidified; otherwise, the inflexible mold may cause defects to form as the casting cools and contracts. After the casting is removed, the process can be repeated immediately.
Advantages of permanent mold casting:
- Since the mold is reusable, initial tooling costs can easily be recouped with high-volume runs
- High dimensional accuracy can be achieved if an accurately machined mold is used
- Repeatability is high, and little preparation needs to be made between castings.
Disadvantages of permanent mold casting:
- "Permanent" molds don’t last forever, and may need to be replaced midway through a large run
- Inflexible molds can lead to defects if castings are not removed promptly
- Tooling costs are relatively high compared to greensand casting
Greensand Casting
Greensand casting is a common form of sand casting that uses moist, clay-bonded sand to form a mold. First, sand is packed around a pattern to form a mold cavity. Then the pattern is removed and the mold cavity is placed in a brace and paired with its other half, similar to permanent mold casting. Next, molten metal is poured into the cavity. After the casting has solidified, the mold is broken to remove the casting. The casting is then finished by grinding off unnecessary characteristics like tabs and risers. Many facilities are able to reclaim a high percentage of the sand used in greensand casting.
Advantages of greensand casting:
- Nearly any part can be cast using greensand, with a wide range of size and weight
- Tooling and materials costs are very low
Disadvantages of greensand casting:
- Surface finish is not as smooth as other casting methods
- Dimensional accuracy is also lower than other casting methods
Die Casting
Die Casting is similar to permanent mold casting in that it makes use of a reusable metal mold, rather than disposable sand-based molds. In die casting, however, molten metal is often injected into the mold at high pressure. The high pressure results in greater detail and finer surface finish compared to other casting methods, but durability of die castings can be compromised by trapped pockets of air. While die casting is preferred for high-volume runs of smaller parts, the complexity of die castings is limited. The configuration of the die casting apparatus limits the variety of cores that can be inserted.
Advantages of die casting:
- Parts can be cast with greater detail and superior surface finish
- Dies, often machined from high-grade tool steel, last longer than other molds
Disadvantages of die casting:
- Initial tooling costs are very high
- Complexity is limited, especially for products with hollow sections
- Overall strength can be compromised by porosity and other defects
Comparison of Aluminum Casting Methods
This post is excerpted from our ebook, Manufacturing with Aluminum: History, Forming Techniques and Best Practices. Click below to download the ebook for free.
Tags: Metalcasting, Processes, Aluminum Casting, Aluminum, Eagle Aluminum
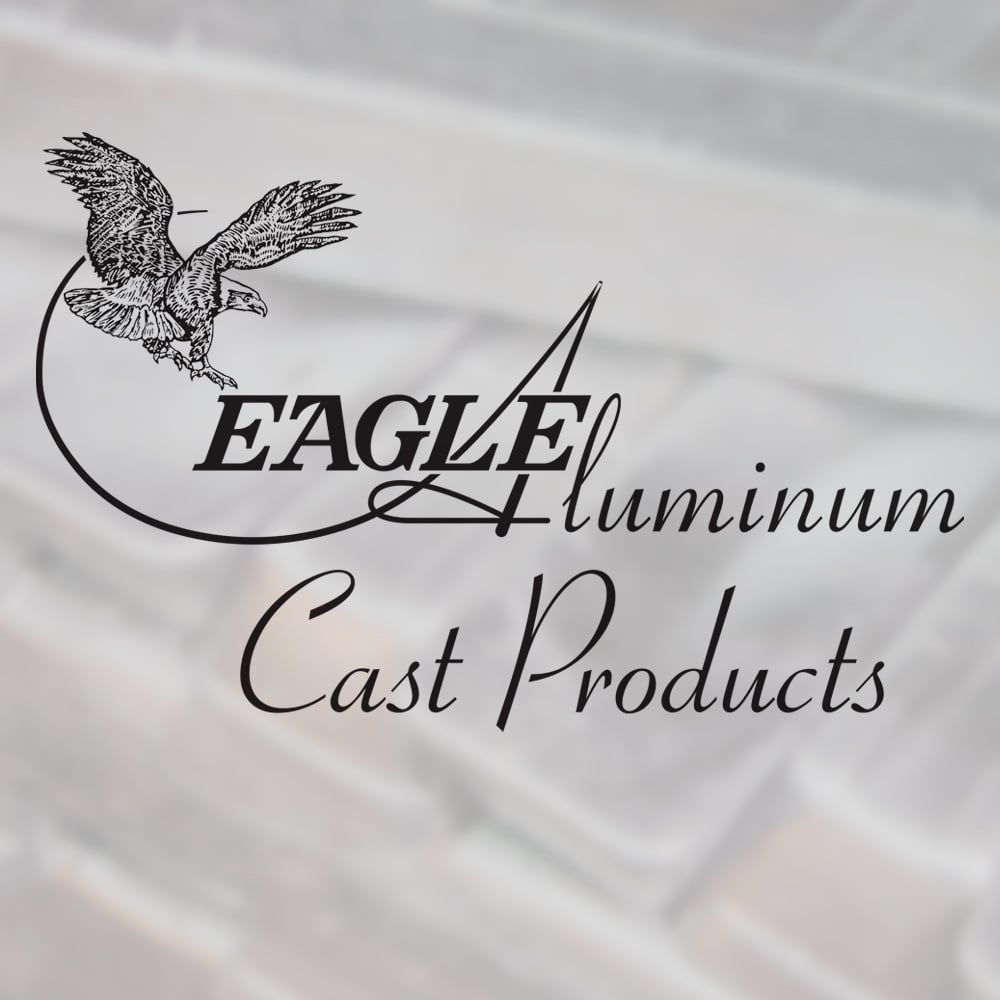
Written by Jim Smith, Jr.
Jim Smith, Jr. is the Technical & Sales Manager at Eagle Aluminum Cast Products in Muskegon, MI. Given his father’s career as a mechanical engineer, Jim grew up in foundries and often used castings his father brought home as toys. During his college years and into his first jobs, Jim developed skills in quality, engineering and customer service. Jim joined Eagle Aluminum in 2012 as a Technical Analyst and now manages all of the company’s Technical and Sales functions.