Getting Started with Airset Casting
Every manufacturer bringing a cast product to market must decide on the right casting process to use. Casting methods like shell molding, greensand casting, investment casting and airset casting all have their own sets of benefits and drawbacks. The right choice depends on the quantity being cast, the size of the part, and the requirements for dimensional accuracy, surface finish and material.
While it's not as widely used as shell molding or greensand casting, airset casting has plenty of advantages, and can be the perfect option for the right product.
Airset casting, or no-bake casting, is a sand casting method that involves creating molds from chemically bonded sand. Unlike shell molds, airset molds do not need to be heated to solidify. Compared to other sand casting methods, like greensand, airset casting can offer better surface finish and tighter dimensional tolerances.
The unique characteristic of airset casting is the chemical bonding agent introduced to the molding sand. Greensand casting, in contrast, uses moist, clay-bonded sand to form molds. These molds can be created and cast quickly, but the drawback is that the sand grains are often coarse, resulting in rougher surface finish. Airset casting can make use of much finer sand that–without a chemical additive–wouldn't bond well enough to form a mold. As an added bonus, airset casting can provide excellent consistency from part to part, with very few surface defects. Since as-cast parts are aesthetically appealing, manufacturers can save on machine finishing costs in many cases.
What to know before you start airset casting
Airset casting foundries use a wide variety of bonding agents and sand types, so be sure to consult with your supplier before ordering a run of parts. You'll want to make sure that the sand used is suitably fine to produce your desired surface finish. You'll also want to be aware of the type of binder used in the airset process. If certain chemicals are used, the foundry must file paperwork with the Environmental Protection Agency. Other binding agents are considered more environmentally friendly, and can be used without restriction.
Most importantly, be sure to choose a foundry with a strong customer-service approach. Your supplier should be willing to discuss your product and make design recommendations, if necessary, before getting started on casting. A good foundry will have expertise in many different metal casting methods, and can help you decide which technique is best for your product.
To learn more about airset casting, take a look at Eagle Alloy's reference guide: Airset Casting Tolerances, Capabilities and Design Recommendations
Tags: Metalcasting, Eagle Alloy, Airset Casting
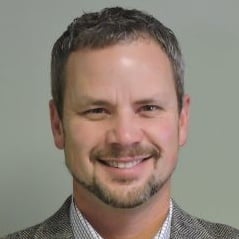
Written by Jeff Cook
Jeff Cook is Chief Sales and Marketing Officer for Eagle Alloy in Muskegon, MI. While enlisted in the Marine Corps Reserves, he began working at Eagle Alloy in 1986 as a snag grinder on 3rd shift after his father told him to “Get a job!” Jeff is past President of the American Foundry Society. His passions include educating young people on the careers and advancement available in the metalcasting industry.