Heat Treatment: Hardening
Hardening a metal achieves much more than simply making it mechanically harder. It also improves strength, making the alloy more resistant to plastic deformation, and can aid with corrosion resistance. However, a harder metal is also often a more brittle metal. As such, hardening is usually just one part of a properly designed heat treatment plan.
Because hardening can be accomplished through numerous heat treatment strategies, it’s important to know what options are available to a casting customer, how the methods differ, and where hardening fits into the master plan.
In this article, we’ll explore the science and practice of hardening, and explain when conditions are appropriate for a particular hardening strategy. Whether you’re working with the Eagle Group or another metal manufacturer, hardening is an important step in manufacturing, so it’s good to know the basics.
The Science of Hardening Cast Parts
Hardening is an expansive term covering a handful of different but related techniques used to improve an alloy’s mechanical properties, particularly strength, hardness, and corrosion resistance. Despite the variety of methods, there are fundamental principles common to all hardening practices: the highest-level principal that unites all hardening heat treatment is targeting the control of dislocations in the metal’s crystal structure.
Microstructures, Grains, and Dislocations
Before we get to dislocations, let’s take a moment to review the importance of microstructures in heat treatment. As we discuss in our Introduction to Heat Treatment blog, by altering microstructures we can control the properties of steel. Microstructures are made up of a huge number of individual crystals, also known as grains. These groups of grains are patterned lattice structures, like building blocks, that give metals their integrity. The distinct grains in a material are separated by grain boundaries, which are the dividing lines separating two grains. Below, we can observe the meeting of grains (green) at grain boundaries (black).
Grain boundaries are very important actors in the performance of a metal’s mechanical properties because grain boundaries prevent the movement of dislocations. Dislocations are irregularities in the material's crystal structure in the form of abrupt, random changes in the arrangement of the atoms. Although dislocations can be seen as a kind of 'defect' in the material's otherwise predictable lattice structure, their occurrence is completely natural: all materials are dislocated in one way or another, and to one degree or another. It's how we control the dislocations that matters.
So, why are dislocations important in the context of hardening? Because when a material is subjected to stress, these dislocations begin to move, which means the metal also begins to move, and these mobile dislocations are what permit a material to be ductile, which is the opposite of hard: if these dislocations are allowed to slip past each other, the material will readily deform. In other words, it will be ductile. But when we are hardening a material, we want to stop the dislocations from moving, not facilitate them.
So, how do we mount a resistance to these jumpy dislocations? The secret lies in hardening: successful hardening gives rise to microstructures that interrupt the movement of dislocations. There are a number of ways to prevent dislocations from traveling across a material: from adding alloying elements to applying thermal processes.
Hardening Before Heat Treatment
Before we cast and eventually heat treat parts, it is important to make sure the cast alloy is capable of hardening by virtue of its chemistry, so that its structure can actually benefit from heat treatment.
Solid-Solution Strengthening
Solid-solution strengthening is not a form of heat treatment, but it is nonetheless a way of hardening a material before subjecting it to thermal treatment.
Solid-solution strengthening is the practice of dissolving trace amounts of one element into another in order to create a crystal structure comprised of both elements. In the case of steelmaking, that often means melting iron with carbon or other common alloying elements like manganese (Mn), chromium (Cr), or nickel (Ni). Combining iron with another element, like carbon, changes the structure of the crystal lattice in a way that hamstrings the movement of dislocations. In the case of carbon, this transformation is due to atoms squeezing between the iron’s lattice structure. These points are known as interstitial: the small carbon atoms fit in the gaps between iron atoms. There are also substitutional elements that actually replace iron atoms in the solution: manganese (Mn) and nickel (Ni) behave this way in steel. What unites both of these interactions is their effect of making the material more resilient against dislocation movement, because of the stress caused to the crystal structure by these alloying elements.
Interstitial structure
Substitutional structure
Because alloying elements increase the cost of steel, it is important to not overdo the amount of alloying elements. Money is often wasted specifying an alloy steel where a simple carbon steel would be sufficient to meet specifications.
Hardening Processes: Phase Transformation Hardening
Once a part, based on the right chemistry, is cast and cooled, it’s time to move the solid castings to the heat treatment ovens. Let’s take a look at how a hardening thermal process, known as phase transformation hardening, fortifies carbon and low alloy steels against stresses in the field.
Austenization: heating to change steel's microstructure
Austenization is a critical component of phase transformation hardening: it is the process of heating steel to a temperature high enough to produce austenite, which is the phase structure you get when you heat steel between above the upper critical temperature (Ac3 temperature in the diagram below). You will also notice the change in the grain sizes just above that threshold temperature, known as the austenization temperature. Above this temperature, the steel’s microstructure starts to change shape and approach the kind of microstructure we want out of a finished product.
Quenching: quick cooling to prevent carbide formation
A critical characteristic of austenite is its ability to absorb more carbon than other phases closer to room temperature. The additional carbon is responsible for much of the hardening that happens.
But there is a practical difficulty with austenite: when the metal cools down, the carbon atoms that had been absorbed during the ramp-up (and are responsible for hardening the material) get kicked out of the steel’s inner lattice structure and group into undesirable carbides (concentrations of carbon). The only way to keep them from doing this is by cooling them off so quickly they don’t have a chance to escape. Finishing off an austenitized carbon or low alloy steel with very quick cooling is known as phase transformation hardening. Here’s how it works (on a simplified level):
Heat is the punch bowl at the party: given enough of it, atoms begin to mingle. So, when we heat steel above its austenization temperature, a phase transformation begins to occur that allows more carbon to fit between the iron atoms. Above this critical temperature, the alloy’s other microstructures begin to form austenite.
And once the steel has finished absorbing a higher amount of carbon and is fully austenitic, it is ready to be cooled (most steels have roughly a 2% solubility limit for carbon, but many common steels have solubility limits lower than 2%).
From here, it gets interesting: if we allow the steel to cool slowly at room temperature, eventually the carbon will be expelled from the space between the iron atoms because carbon is only slightly soluble in iron at room temperature. However, if we cool the austenite very quickly, for example by dropping it into a liquid solution in a heat treatment known as quenching, we effectively lock the carbon atoms in place, forming a new type of steel microstructure called martensite.
Learn more about quenching in our dedicated blog post
However, martensitic steel is very hard and brittle, so it requires a final thermal process to be brought into a good balance of strength and ductility. Tempering is a process used to relax the excess stresses after quenching. Indeed, without tempering, martensite is too brittle and lacks sufficient toughness to be of much use in industry applications. Tempering reduces residual stresses that result from the quenching and moves and alloy closer to its stable structure, making for a much more useful end product with a desirable balance of strength and ductility known as tempered martensite.
Hardening Processes: Precipitation Hardening
Precipitation hardening is a highly specialized form of heat treatment that can be used to impart superior strength and hardness on certain steel alloys as well as nonferrous metals.
Precipitation hardening only applies to alloys that are precipitation hardenable. We know, this sounds a little redundant. But the physical reality is that only steels with certain mixtures of alloying elements can actually be made to harden via precipitation. This specialized (and expensive) process works by coaxing precipitates out of a solid solution that give strengthening boundaries to a material’s microstructure. Precipitation hardening is also known as age hardening because it is a process that can sometimes take days.
Usually, precipitation hardening works best for alloys containing one or more special alloying elements like titanium (Ti), niobium (Nb), molybdenum (Mo), vanadium (V) or copper (Cu), because in order for precipitation hardening to work, an alloy system must exhibit solubility that decreases with decreasing temperature. The long heating time allows these ferro-alloying elements to dissolve completely and, along with the iron and carbon atoms, to form a single solution. Upon cooling, some of the alloying elements run out of the solid solution and create precipitates, i.e., deposits of solid form. Like other hardening methods, these solid precipitates are effective in stopping the propagation of dislocations.
Age hardening’s effectiveness in stopping dislocation movement is particularly impressive. As such, it is considered a highly specialized form of heat treatment and is often employed for parts that must be able to withstand extremely high temperatures.
Specialty Hardening Process: Case Hardening
Once your preferred alloy grade has been mixed, cast and heat treated according to your specifications, cast parts can also benefits from secondary hardening treatments that are used to add special properties to a near-finished product.
Case hardening is known as a differential heat treatment. It is a common specialty heat treatment process that results in a workpiece with different hardnesses throughout different sections of the workpiece, in this case the interior and exterior. It’s effectively the metallurgical equivalent of baking a bread with a nice crusty exterior and a gooey interior. Case hardening a metal produces a wear-resistant outer layer while still allowing for a more ductile material interior. Case hardening a metal creates a very hard, wear-resistance outer layer. The goal is to soak a workpiece in a concentrated carbon atmosphere for a very specific amount of time at an optimal target temperature. By controlling the time and temperature, we can control what is known as the ‘case depth’, which is the depth to which the hardening effect will penetrate the material.
Case hardening is carried out in controlled atmospheres, meaning the air or liquid in which the component gets submerged is a special concoction. The two most common processes used in case hardening are carburizing and nitriding. Carburizing exposes the surface of the part to a highly concentrated carbon atmosphere which saturates the surface with additional carbon, while nitriding uses atomic nitrogen gas to bring about strong nitrides on the material surface.
Hardening Heat Treatment for Cast Parts at the Eagle Group
The Eagle Group is an expert in primary heat treatments for a vast catalog of alloys. Between pouring hundreds of alloy grades and manufacturing nearly 2000 active part numbers, we have plenty of reason to heat treat as much as we can in-house. Our facilities include 9 car-bottom furnaces and 3 quench tanks offering a range of quench severity. Equipped with the latest in digitalization, we have the capabilities to produce electronic certifications for each individual heat treat cycle.
Whether it’s raw or machined cast parts, the Eagle Group has you covered for the majority of primary processes. If your part requires secondary processing, such as case hardening or precipitation hardening, the Eagle Group works with trusted heat treatment specialists Hansen/Balk Steel Treating Company and State Steel Heating Company. Our long relationships with these regional suppliers ensure a smooth workflow from conception to delivery.
Because our mission is to deliver parts that perform and that enjoy a long life in service, one thing is sure: many of our heat treatment plans will include some form of hardening. Still, hardening is only one of the steps along the way. The Eagle Group is an expert in designing holistic heat treatment programs that make sure your parts perform as required. But we don’t stop there: tell us your overall property objectives and we’ll build a program that fits your requirements.
Learn more about heat treatment for cast and machined parts. Download our free ebook below:
Learn More About Heat Treatment in Our Dedicated Series
Tags: Processes, Metallurgy, Heat Treatment
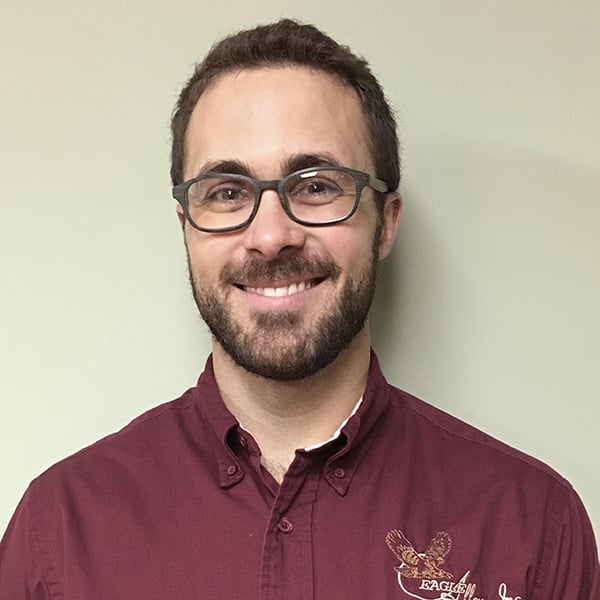
Written by Jason Bergman
Jason Bergman is Senior Quality Engineer and Metallurgist at Eagle Alloy. He has been with the company since 2013.