Heat Treatment: Quenching
Imagine a medieval blacksmith hammering a sword fresh out of the fire. With the weapon still red-hot, he dunks it in water. The water hisses and boils around the submerged steel as it turns color from glowing orange to grey. This iconic scene of rapidly cooling a workpiece is called quenching, or quench hardening, and is one of the oldest and most common heat treatment processes used to harden and strengthen common carbon steels. In modern metallurgy, superior corrosion resistance for most stainless steels is also an important property achieved through quenching.
Once discovered, the hardening advantages of quenching were obvious. Still, ancient metalworkers didn’t have the scientific tools to understand why quick cooling imparted beneficial properties on steel. It wasn’t until the development of modern metallurgy that we began to understand where this special strength, hardness and corrosion resistance comes from: the changes in microstructure that result from rapidly cooling red-hot metal.
In this article, we’ll draw on modern metallurgical science to explore the benefits of quenching: why it’s done, how it's done and where it fits into a typical heat treatment plan.
Looking for an in-depth guide on essential heat treatment processes like quenching for metalcasting and CNC machining?
Click below, fill out a brief form, and get your free ebook instantly.
A Brief History of Quenching
Where blacksmiths first started quenching is hard to say for certain: it likely happened in multiple regions around the same time. The earliest written record of quenching is recorded in Homer’s Odyssey, around 800 BC in the Eastern Mediterranean, but even earlier dated archeological sites in the Middle East show evidence of quenched metals.
Farther east, there is written evidence that Chinese blacksmiths were using quenching more than 2,000 years ago. Chinese ironworkers used to enjoy debating which rivers’ waters were the best for quenching. This kind of experimental thinking gave China the special distinction of a region where it was common practice to try new, untested quenching liquids.
Even farther east, although evidence of quenching comes a little later around the 6th century AD, Japanese blacksmiths began to achieve international renown for their sword making. And this was in part due to their quenching ingenuity: a clay mixture, whose exact recipe was closely guarded, was applied in various thicknesses across the blade. When the sword was quenched, different segments cooled at different rates, giving the blade its cutting-edge curvature and famous sharpness. Without this impressive understanding of cooling rates, you can forget about the iconic Samurai sword.
The Science and Benefits of Metal Quenching
Early blacksmiths were aware that quickly cooling metal workpieces somehow made them stronger and harder—or in the case of weapons, sharper and more dangerous. But until the mid-19th century, we didn’t understand why.
Steel has the added advantage of being particularly amenable to the beneficial properties imparted through quenching because iron possesses a special trait: it is polymorphic, meaning its internal structures exist in different states depending on the amount of applied pressure and heat.
As we explore in our hardening blog, steel’s crystalline structure changes as it is passes through different temperature thresholds. When steel is heated past certain temperatures, its microstructures begin to change in ways that lead to harder and stronger steels. Past an upper threshold temperature, iron is able to absorb much more carbon than at room temperature, due to the phase it is in at that point, known as austenite. When steel is quenched straight out of the furnace, it transforms this hot austenite to martensite by freezing most of the austenite microstructure in place. Therefore, quenching is the art of shortening the window of time that the desired chemical structures have to rearrange. When a material is quenched, the diffusion that happens between atoms suddenly comes to a halt, locking in the current structure. The material will then stay this way, provided it is not re-exposed to elevated temperatures that would re-encourage diffusion.
Quenching is also an effective way to improve corrosion resistance in stainless alloys. At higher temperatures, undesirable phases and natural impurities mingle with the other elements closer to the center of the steel grains. Removing a workpiece to let it cool slowly allows the impurities to be pushed to the grain boundaries where they’re susceptible to corrosion. If we quench the metal, these impurities are frozen farther from the grain boundaries, where they’re less likely to be access points for corrosive attacks.
Machinery Used in Quenching
The dedicated pools where workpieces are quenched are known as quench tanks (shown below in a quenching sequence). Modern quench tanks have evolved alongside our understanding of steel’s thermal properties. But in many ways, they have also stayed the same: a quench tank is simply a way to cool a given workpiece in a controlled atmosphere.
Quench tanks come in a variety of sizes, depending on each heat treatment facility’s needs: some quench tanks are only about the size of hot tubs, while others are the size of swimming pools. Regardless of size, quench tanks must be able to maintain cooling temperatures inside a closely controlled range. The Eagle Group’s quench tanks are monitored by digital temperature monitoring equipment in a dedicated heat treat department to make sure the cooling temperatures are well within the standards set down by the ASTM and/or other customer requirements.
One of the most important configurations of a quench system is speed. When cast parts exit the oven, the transfer to the tank has to happen quickly. If too much time elapses between the ovens and the tanks, the metal could fall back below its transformation temperature, and the cause is lost.
Well organized foundries like Eagle Alloy will house their quench tanks as close as possible to their heat-treat furnaces in order to shorten the window of time between exiting the oven and entering the quench pools. Our facilities include a range of stacking racks that allow us to configure our workpieces ideally according to shape and size, as well as to minimize stress during the rapid cooling.
Quench flow is a vital consideration when configuring the stacking racks. Flow describes the velocity of the quenching media moving over the quenched parts. Without flow, the static water boils off into steam which can cling to the part and create a kind of insulating barrier. For this reason, it’s important for the quenching media to keep moving as well as for the parts to have sufficient space between them to allow for adequate quench flow. Many foundries, like Eagle Alloy’s, will have specially designed quench racks to account for all these variables.
A Discussion of Quench Media
For millennia, quenching was limited to rapid cooling through a liquid medium. Whereas modern quenching is still predominantly performed with liquid, today’s pieces can also be cooled in controlled gaseous atmospheres for pieces requiring specific end specs (which we’ll be returning to below). To this end, there are also special vacuum furnaces capable of controlling an atmosphere by soaking a workpiece in a gas quenchant without the introduction of oxygen.
The study of quenching media is an industry of its own, and since the invention of polymers, the number of available quenchants and additives has increased significantly in the past few decades. Although polymers is part of a quench medium, it is more correctly described as an additive because polymers get added to an existing quench medium, like water.
The list of quenching mediums that have been used through the ages is remarkable (and reading through the full list requires a strong stomach). Clearly, our metalworking ancestors were open to experimenting with various natural substances. But before the advent of modern metallurgy, we had no way of isolating and synthesizing the kinds of mediums now proven to be the most effective.
Quenchants are separated into two broad categories: liquids and gases. The various types are practically distinguished by their quench severity, which is a measure of how effectively a quenchant can extract heat from a workpiece. Something with a higher quench severity will cool the workpiece faster than a quenchant with lower severity. Quenchants are also distinguished by their measures of unwanted byproducts and adverse reactions that can occur during cooling. Something may have a high quench severity, but this intensity can sometimes produce undesirable distortions or an uneven distribution of physical and mechanical properties across the piece. Understanding quench mediums is the backbone of superior heat treatment in metalcasting.
Liquid Media
Water is a very thorough quenchant, offering the highest maximum cooling rate of any liquid. It is also abundant and less expensive compared to other quenchants. It does have disadvantages, however: due to the intensity of the cooling, bubbles (also known as vapor pockets) can form on the steel and result in thermal differences across the workpiece, putting the piece at risk of unwanted stresses and distortion. The solution for this natural occurrence is to agitate the cooling bath, effectively keeping the water moving to break up the bubbles, also known as vapor barriers, that serve as a kind of insulation, keeping the workpiece warmer than it should be and interrupting the quenching process. Salt water (or brine) is another common natural quenchant, offering even faster cooling than non-salinized water. There are many variations of salt water; the proportions of minor elements can vary (sodium, potassium, magnesium, etc.), and each of these chemistries will result in a different working upon the material.
Oil has been used as a quenchant for a very long time – think back to the days when oil used to bubble up out of the ground. Oil is an excellent quenchant for its versatility: the temperature of the quenched workpiece doesn’t need to be controlled as closely as with water. Oil’s other favorable attribute is its viscosity (meaning that it flows relatively slowly). Oil becomes less viscous when it gets hotter, but this state change allows it to absorb more heat. In sum, oil is considered the least aggressive quenchant and is a common choice for high-alloyed steels.
Polymers have many of the same advantages as oil: they are versatile and stable. Their quenching severity falls somewhere between the faster quenching oils and the ultimate quenching power of water. Polymers have the special quality of being inversely soluble in water at higher temperatures, meaning the polymer solution separates from the water at the beginning of a quench. This effect creates a polymer layer around the workpiece and provides a more controlled heat exchange between the piece and the water around it. They are less corrosive than water, cheaper and less of a fire hazard than oil, and are effective in minimizing distortion. Due to these advantages, polymers have gained huge share in the quenchant market.
Water and polymer solutions are the quenchants we regularly use in the Eagle Group’s heat treatment facilities. Our Team has decades of expertise in finding the right liquid quenchant solution for your parts.
Gas Quenchants
The idea of gas quenching is the very same as with liquids: to bring a metal down from its critical temperatures quickly and uniformly across the part. One of the big advantages of gas quenching is that, unlike liquid, there is no intense surface interaction between the metal and the medium. As such, gas-quenched workpieces will carry less surface residue on the material, skipping the need to rinse and get rid of quenchant residues. The two important variables in gas quenching are pressure and velocity: the higher these are, the higher the heat transfer coefficient, and faster the cooling.
The gases used in quenching are most commonly nitrogen, argon, and helium. These gases are known as inert gases because they share the property of being very reluctant to mix with other elements to form compounds. Argon and helium are noble gases because they are totally unreactive with other elements under almost all conditions. Nitrogen is not a noble gas, but in the quenching atmospheres where nitrogen is used, it is inert for all intents and purposes.
Inert gases are ideal for quenching because they don’t mix with gases like oxygen. Oxygen is the culprit behind corrosion and is therefore wholly excluded from gas quenching. The idea of the gas quenching process is to fill a tank with a high-purity gas, ensuring no oxygen enters the tank at any time. Gas quenching is highly effective for removing oxidation from the quenching equation and is therefore also a more expensive procedure than quenching via liquid media.
Workpieces quenched in a non-controlled atmosphere develop a loosely adhering oxide layer on the surface of the material, known in the industry as ‘heat treat scale’, whereas gas-quenched parts experience no such oxidation. This absence of oxidation, or ‘rust’, means that a piece entering the oxygen-free controlled quench tank will have the same exact dimensions after the quench because there is no oxidative layer to remove by shot blasting after quenching. Due to this host of benefits, controlled gaseous quenching is used for parts with extremely stringent dimensional specifications, such as are required by the aerospace and foodstuff industries.
Quenching as Part of a Comprehensive Heat Treatment Plan
Quenching is an essential hardening process, resulting in a steel that is very hard and very brittle. However, the modern use cases for steel this brittle are few and far between. Quenching is almost always followed by subsequent heat treatment processes that seek to keep some of the hardness and strength won by quick cooling while also increasing toughness and ductility. The quenching process often falls between initial heating and the secondary heat treatment processes: tempering.
The Eagle Group’s quenching facilities have grown with our experience. After decades of in-house heat treatment, we have the expertise to apply a wide range of quenching programs to cast parts. Quenching—and heat treatment in general—is one more way that the Eagle Group takes parts all the way from casting to completion.
Learn More About Heat Treatment in Our Dedicated Series
Tags: Processes, Metallurgy, Heat Treatment
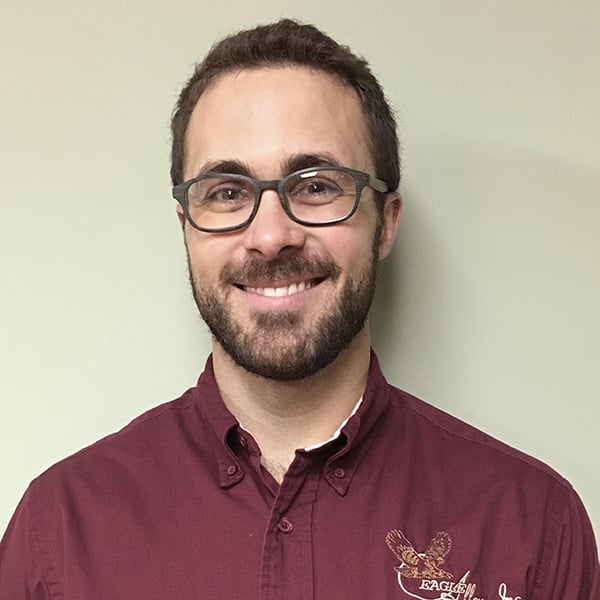
Written by Jason Bergman
Jason Bergman is Senior Quality Engineer and Metallurgist at Eagle Alloy. He has been with the company since 2013.