Metal Properties: Weldability
Joining multiple metal parts together into a single, cohesive unit is an indispensable process to manufacturing. Bolts, screws, and adhesives are often used to unite separate parts, but many applications call for a more solid connection. Thanks to the craft of welding, manufacturers are able to effectively create a single part from multiple components. Casting facilities are also able to use welding to repair minor casting defects, improving overall process efficiency and reducing part cost.
Understanding the weldability of various alloys is key to creating welds that last and parts that perform in the field. As a mechanical property, weldability is also an important consideration in designing and producing cast parts.
What Is Weldability?
Weldability is the ability of a material to be welded and, more specifically, the science of knowing the environment, process and materials required for a successful weld. When we say successful, we are referring to a weld that exhibits necessary material properties and performs as expected in the field.
By understanding weldability, metal casting companies can choose appropriate materials for each part, and can plan for successful production welding. .
Weldability in Metalcasting
Foundries use weldability principles to deliver batches of parts in the most cost-effective way possible by repairing minor defects with successful welds. Castings destined to be connected through welding must be made of weldable alloys. With the right materials and solid welding technique, manufacturers can ensure that welded parts are indistinguishable in their field performance from non-welded parts.
The image below compares two metal samples with effectively identical microstructures, one welded and one not welded.
Production Welding
There are hundreds of variables in the metalcasting process. Even with a robust quality management system, both shell mold and investment castings inevitably result in a small percentage of parts that don’t meet customer requirements. Instead of scrapping these parts, we usually recommend repairing many of them through welding. Any welding carried out before delivery to the customer is known as production welding.
If we encounter a problem with part quality during our production runs, we can often remedy it with engineering controls. For example, shrink is a potential issue that requires returning to the drawing board to make sure there is enough allowance for the liquid metal to solidify in proper proportion to the casting mold.
However, there are a few points in the casting process where unwanted and outside particles or formations can infiltrate the process. For example, when putting the mold halves together and adding the consumables, loose sand could be left in the mold cavity and result in surface blemishes. Another example is during the pouring: turbulence from the molten metal filling the cavity can suck air down with it, the result of which can be small bubbles on the part’s surface. Although we have many engineering and production controls in place to minimize these interactions, they still occur, albeit infrequently, due to the sheer number of variables and the complexity of the casting process. The important point is that when we do have to weld, we do it in the most efficient way possible.
A strong understanding of each steel’s weldability is essential for streamlining this process. For example, by qualifying a weld process for each alloy based on its weldability properties, we are able to quickly and efficiently assign the process and materials to use in a successful weld.
Luckily, steel casting companies have an equation in their quiver that tells them almost everything they need to know to choose the optimal alloy and execute successful welds: carbon equivalency.
Understanding Weldability to Cast Parts that Perform
Carbon equivalency (CE) is so important to understanding weldability that the two terms are sometimes used interchangeably.
What Is Carbon Equivalency?
Carbon equivalency relates the total chemistry of an alloy to its carbon content. This is due to the other alloying elements, when taken together, behaving like carbon in hardening the material. As we discuss in the next section, hardenability and weldability are closely correlated.
You might be asking why carbon takes center stage in this property: carbon is the chief element that governs how hard and brittle a steel will be. For example, low carbon steels are quite ductile, whereas cast iron, with higher carbon levels in the 2-4% range, is extremely hard and brittle and is, for all intents and purposes, non-ductile.
Carbon Equivalency and Hardenability
Why are hardness and hardenability (how capable a material is of forming martensite) so important to welding? Because welding is, in effect, a small and localized heat treatment process. As such, we have to be careful not to change the microstructure of the heat-affected zone (HAZ) to a more brittle constitution, such as martensite, after application of the heat [for an in-depth discussion of martensite's place in the hardening process, head to our dedicated blog here].
“There's an actual dimensional section size change with the phase transformation. It's a big deal. That is one of the biggest things that can lead to cracking due to thermal stresses or residual stresses based on that material phase change if a weld process is not properly defined and monitored,” says Jason Bergman, Eagle Alloy's Metallurgist and Senior Quality Engineer. In other words, a careless weld can produce a phase change in the material, which in turn will leave residual stresses that can lead to problems in the field.
We avoid this unwanted outcome by managing all weld variables, namely by controlling the preheat temperature required of the base metal and by maintaining adequate heat between each pass in a multiple pass weld. This strategy is also known as managing the interpass temperature.
The carbon equivalency equation, discussed below, tells us what we need to know to regulate temperatures during welding.
The Formula: to Preheat or Not to Preheat
The International Institute of Welding’s carbon equivalency formula is as follows:
Where:
- CE = Carbon Equivalency
- Mn = manganese
- Cr = chromium
- Mo = molybdenum
- V = vanadium
- Cu = copper
- Ni = nickel
The largest factor in carbon equivalency is carbon content, and the higher the overall number, the more likely the steel will require pre-welding heat treatment. Generally, a carbon value above 0.30% and carbon equivalency value above 0.50 means that the base metal will have to be preheated and remain adequately hot during each interpass. It must be noted that these are ballpark figures, but that they still serve as important guidelines when assigning a weld procedure to new material.
As for the range of preheating temperatures, they can vary widely; some high carbon tool steels need to be preheated as high as 800 degrees Fahrenheit. A typical range is 300-400 degrees F.
Weldability for Carbon vs. Stainless Steel
Carbon equivalency is the golden equation for carbon steels. As we’ve explored in other articles, stainless steel’s hardness comes down to its chemistry, and is much less susceptible to hardening through thermal processing.
However, there are specialty grades of stainless like 17-4 PH which is a martensitic stainless steel that can be precipitation hardened. Like carbon steels, these grades would be considered harder to weld because they would have similar restrictions to carbon steels, namely preheating and cooling rate requirements.
The Eagle Group’s Post-Weld Process
Heat treatment is sometimes necessary after a weld is performed. Post-weld thermal treatment generally targets the normalization and stress relief of the base metal surrounding the weld, known as the heat-affected zone. Interestingly, the weld itself doesn’t usually require the structural normalization that heat treatment imparts on material – it’s really just the base metal that needs a little shoring up. The reason for this can be credited to the advancements made in the welding rod industry: most rods are designed to be used with little to no post-weld heat treatment.
Finally, a welded casting will be put through a post-weld heat treatment plan. This often applies the same thermal processing as its non-welded counterparts as part of preparation for service. After all, heat treatment is how we finesse the mechanical properties of each casting, whether they’ve been welded during production or not
For a comprehensive study of heat treatment in machining and metalcasting, head to our dedicated Blog Series.
The process of welding stands as a pivotal cornerstone in the manufacturing domain, enabling the assembly of distinct metal parts into cohesive units. The comprehensive understanding of weldability, underscored by the balance between various alloys and their respective properties, is vital for ensuring the longevity and functionality of welded components. The Eagle Group sets the industry standard, combining strict ASME (and other welding) guidelines with experienced practices to ensure each weld exceeds expectations. For our own processes as well as those of our customers, weldability is a key metal property.
To learn more about metals' mechanical and physical properties, check out our Metal Properties ebook. Fill out the form below to download:
Tags: Welding, Metallurgy, Metal Properties, Mechanical Properties
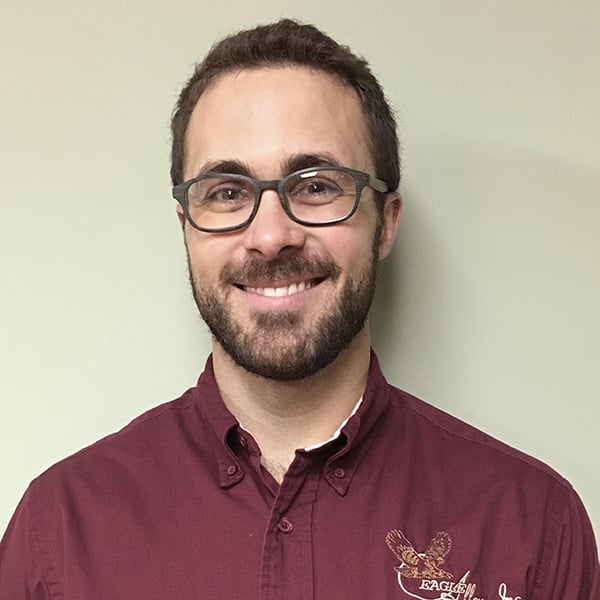
Written by Jason Bergman
Jason Bergman is Senior Quality Engineer and Metallurgist at Eagle Alloy. He has been with the company since 2013.