What You Need to Know about Weld Repair for Steel Castings
When done right, weld repaired castings are just as structurally and functionally sound as their non-welded counterparts. However, weld repair in steel castings is often misunderstood by casting customers. Some companies simply do not allow weld repair, and others place strict requirements on where weld repair can take place on a part. By better understanding the effects of weld repair on part appearance and functionality, casting customers can benefit from weld repair strategies that optimize cost, production time and part quality.
Click here to learn more about common defects in casting
The problem with weld repair often stems from a bad experience the customer had somewhere along the line. "Sometimes when we receive a drawing for a new part," says Eagle Alloy Chief Sales Officer Jeff Cook, "there's a note on it that prohibits weld repair." In these cases, Eagle Alloy enters weld repair as a point of negotiation. "Most of the time I find out it's on the drawing because they've had a bad experience with another foundry at some point in time," Cook continues. "You've got castings coming in from overseas that have been weld repaired and heat treated improperly. No wonder these folks are nervous about it; they think all foundries do it that way."
But what many customers don't realize is that welding is a standard part of the casting process, and according to ASTM International Guidelines, foundries are responsible for determining when and where welding should take place. By limiting or disallowing weld repair, customers can drive up part prices and go against the principles of some of the world's top foundries.
Good Weld Repair Does Not Reduce Part Quality
Part of Eagle Alloy's role as a casting supplier is to educate customers on the facts of weld repair. To facilitate the process, we produced a case study comparing welded and non-welded parts in terms of hardness, chemical composition and microstructure. The study shows that the properly welded and heat-treated section of the part varies negligibly from the non-welded sections. In other words, welding in no way diminishes the performance of the part.
Download case study: Weld Repair at Eagle Alloy
The image above shows the typical microstructure of base metal away from the weldment (left) and the heat-affected welded area. Magnification at 500x.
In fact, this challenge is so prevalent in the casting industry that the Steel Founders' Society of America (SFSA) provides readymade content for casting facilities to share with their customers to improve their understanding of weld repair. In their white paper, Welding Steel Castings, SFSA points out that welding is one step in the process of manufacturing steel castings to customer requirements. The word "repair" implies that welding is a sign of poor quality, when in fact welding is a tool that is used as part of standard procedure. SFSA recommends using the phrase production welding instead of weld repair to more accurately reflect welding's role in the casting process.
"Welding is an additional cost like machining, and manufacturing seeks to minimize the requirement for welding to lower costs and improve quality," the guide states. "Even so, welding is routinely used as a part of the production process to manufacture the highest quality castings."
When Weld Repair Is Used
The vast majority of weld repair is done on cosmetic blemishes. When a defect is large enough or placed in a critical area so that it threatens the integrity of the part, it is almost always scrapped. In order for an inspector to mark a part for weld repair, that part must contain a defect that can be excavated without making walls too thin or affecting load-bearing elements.
In other cases, weld repair may not be economically viable. Welding also takes time and resources, including equipment, space and man-hours. If it's cheaper for a facility to produce another part, the foundry will often elect to scrap weldable parts and produce more to make up the difference.
Consequences of Limiting Weld Repair
While ASTM International standards impose no restriction on steel casting producers in the use of welding, purchasers are free to add restrictions during the product design phase. Foundries and customers may come to an agreement resulting in no welding, limited welding, or welding only with prior approval. However, all of these arrangements present challenges.
- First, any limitation to a foundry's ability to weld repair parts will result in higher piece prices. Foundries like Eagle Alloy incorporate a certain amount of weld repair into their pricing structures. Without the ability to use weld repair, they'll plan to scrap more parts, and the cost of those additional parts will be added to the overall costs of production.
- Second, limiting weld repair to certain areas can create bottlenecks and confusion during production. Weldable areas may be strictly delineated in a blueprint, but in the real world it's difficult for an inspector to tell if a weld repairable defect lies inside or outside the boundary. This can lead to excess welding, or unnecessary scrapping, or can require further input and consultation from the customer.
- Third, by limiting a foundry's ability to weld repair parts, many customers disqualify themselves from working with some of the world's top foundries. Not only is welding an accepted practice among high-quality casting facilities, it is mandated by some. For reasons including scrap rates, lean manufacturing, production workflows and environmental goals, many excellent foundries will simply refuse to take on a project that disallows weld repair.
When casting customers are well informed of the facts surrounding weld repair, everyone benefits. In some cases it is perfectly reasonable for a customer to request limitations on welding, but more often the responsibility should be left to the foundry to determine when and where welding can be performed. If a customer has had a bad experience with welding in the past, the foundry can help assure them that welding will be done properly by explaining the process and showing documents (like the Eagle Alloy case study) that illustrate key points.
To learn more about casting defects, weld repair and casting quality control, review our resources below:
Tags: Casting Defects, Welding
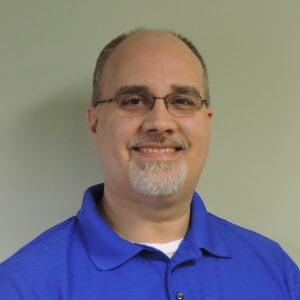
Written by Mark Hollenbeck
Mark Hollenbeck is Senior Sales Engineer at Eagle Alloy. He has been with the company since 1995.