Heat Treatment: Normalizing
Normalizing is one of the most common heat treatments used in manufacturing carbon steel. It is a vital process to ensure that the mechanical and physical properties of a carbon steel workpiece are integrated and distributed uniformly across the material.
In steelmaking, material uniformity is achieved by carefully controlling a casting’s microstructure – specifically, its grains. Grains are distinct areas of crystal structures oriented in the same direction. Multiple grains together make up a metal’s structure. The goal of normalizing is to target these grains in order to even out the differences between them, resulting in a more mechanically stable product. It’s for this reason that the process is named as such: it ‘normalizes’, or homogenizes, grain size, shape, and orientation.
Normalizing is a critical process for returning carbon steel to a more homogenous condition after forging, machining, forming, or welding. Foundries and steel mills use normalizing to give steel a clean slate, wiping away the effects of previous working.
In this blog, we’ll look at its importance in foundry casting while also including concepts and principles that are applicable to the larger world of steel manufacturing.
The Effect of Normalizing Steel Products
The chief purpose of normalizing is to refine microstructures. But it does have other benefits: normalizing will also result in a steel that responds better to further working, such as cold working or surface hardening. And whereas some heat treatment processes will always make a steel either harder and more brittle, or softer and more ductile, normalizing doesn’t have a prescribed outcome: depending on the preexisting state of the workpiece, it can either produce a softer or harder material relative to its pre-normalized state.
Normalizing=Uniformity
Imagine trying to build a wall if each brick was a different size and shape, and all stacked together in different directions and orientations. Normalizing a structure like this would mean replacing these irregular bricks with uniformly sized bricks.
Grain Homogenization
When molten metals cool, their grains crystallize and solidify into place. But the type of mold the metal was cast and cools in, as well as how quickly it cools, are two important variables that determine how grain patterns will look when they return to room temperature. This means that many parts will not possess the desirable grain structure without further processing. In other words, grains don’t usually crystallize the way we would like them to on their own.
Moreover, the grains can cool in many different ways, depending on how they got there. If you picked up a piece of natural iron ore, metamorphosed by its time on earth, the grains would be mostly stochastic, meaning their size, shape and orientation would be random and unpredictable because they formed over a long period of time, under a variety of pressures and temperatures. In the world of manufacturing, steel products cool according to more predictable grain patterns, but the patterns themselves are still undesirable and therefore unsuited to properly finished parts: forged steel, for example, has grains that stretch out and crystallize in the direction in which the piece was pressed into shape. In foundries, the grains nucleate inwards beginning from the mold walls due to the thermal gradient between the mold media and the liquid steel.
In short, un-heat treated steel products are vulnerable to mechanical problems because of their grain behavior, no matter how they initially formed.
The Importance of Normalizing for Steel Foundry Castings
Normalization is an especially indispensable heat treatment for foundries. Eagle Alloy, a shell molding foundry, uses silica sand as molding material for castings. Because silica sand is a highly efficient insulator, the metal cools slowly after casting.
Due to the thermal gradient between the mold media and liquid steel discussed above, when cooled, the as-cast microstructures look like columns (see below). These large columnar concentrations are undesirable in a finished casting product. And because the steel cools quite slowly in the mold, the columns settle deep in the alloy’s core. The goal of normalizing is to break up these large columnar grain structures, a process which significantly improves a part’s performance.
Above: as-cast columnar grain structure
Above: the same piece after normalizing
Because the grains are quite large after a casting is removed from the mold, the effect of normalizing produces much smaller grain sizes. As we mentioned above, normalizing doesn’t necessarily lead to a harder steel – it depends on the state of the steel before heat treatment. With carbon steel castings, however, it will usually make the steel harder. This is due to the Hall-Petch relationship: the Hall-Petch relationship predicts that material hardness increases as grain size decreases. In other words, there is an inverse correlation between hardness and grain size. As you can see from the images above, the normalized steel grains are not only more uniform, they are also much smaller.
Many foundry castings will be ready for shipment after being normalized, and do not require further thermal processing.
The Recipe for Normalizing
The point of normalizing is to heat steel to a temperature above the point where grains disassemble and regrow, and then to cool them in a way that promotes uniform grain patterns. Normalization’s recipe calls for heating the metal above a certain threshold temperature, in this case called the recrystallization temperature, then removing it from the oven and letting it cool at room temperature.
The three main stages of normalizing are: recovery, recrystallization, and grain growth. During recovery, internal stresses are relieved. When the steel crosses the recrystallization temperature, new grains are formed. Finally, those grains come to maturity during cooling in a process known as grain growth.
After this careful heating and cooling process, the size of the individual grains will have shrunk and the relative sizes between the grains will be more uniform. This is the perfect outcome for workpiece integrity.
Normalizing and Other Heat Treatment Processes
Normalizing is very similar to the type of heat treatment known as full annealing. In fact, normalizing is sometimes listed as a type of annealing. The reason is that both processes are exactly the sam until the cooling stage. But the differences in cooling produce such divergent results that these two processes are studied individually. Whereas normalizing steel calls for taking the steel out of the oven and cooling it at room temperature, full annealing uses a methodic cooling process inside the oven as the oven follows a ramp-down cycle, carefully controlling the temperature drop. A full anneal is capable of softening very hard materials, like tool steels, enough to make them workable or machinable. It does this by producing very large grains (remember: larger grain sizes correlate with softness). So, despite being similar in process, normalizing and annealing are employed to very different ends.
Normalizing at the Eagle Group
Eagle Alloy uses normalizing more than any other thermal process. Untreated cast parts created using the shell molding process are often too unstable because of the way they cool inside their silica sand molds. Luckily, our world-class foundry boasts an extensive in-house heat treatment facility designed to handle huge volumes of cast parts. Leveraging our metallurgical team and heat treat specialists, the Eagle Group uses normalizing as a finishing process for many castings produced at Eagle Alloy and Eagle Precision Cast Parts, and as a stress relieving process for machined parts from Eagle CNC.
We have developed a 40-page ebook on heat treatment for cast and machined steel parts as a resource to help purchasers procure the highest possible quality steel parts. Click below and fill out a brief form to claim your free copy.
Learn More About Heat Treatment in Our Dedicated Series
Tags: Processes, Metallurgy, Heat Treatment, Normalizing
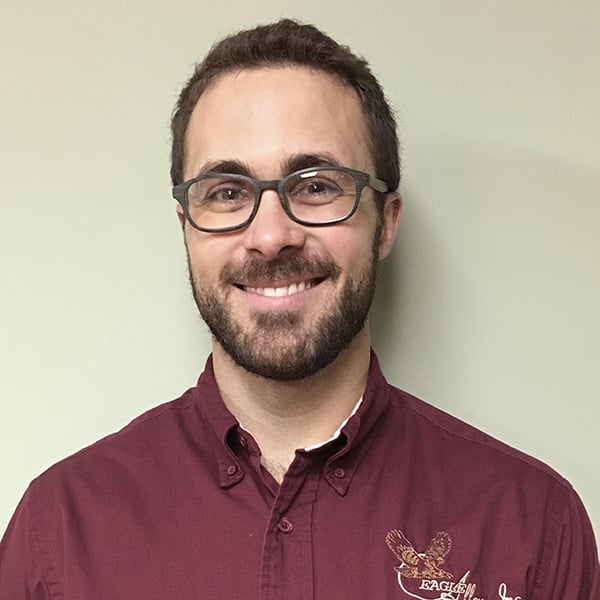
Written by Jason Bergman
Jason Bergman is Senior Quality Engineer and Metallurgist at Eagle Alloy. He has been with the company since 2013.