9 Ways to Improve Manufacturing Efficiency
This article was updated on July 10, 2025.
Efficiency is good for any business. It doesn’t matter if your company is manufacturing or service oriented. Greater process efficiency always offers a wide range of benefits over "business as usual."
On a broad level, manufacturing more efficiently can help cut costs, improve throughput and reduce environmental impact. All of these general benefits lead to additional benefits down the road, from increased sales and quality to improved company image.
Read on for 9 ideas to improve manufacturing efficiency.
How to Improve Manufacturing Efficiency
1. Don’t Waste MaterialWaste is a broad term, and can refer to materials, energy, man-hours or space. One of the biggest and most expensive kinds of waste is material waste. Here are a few ideas for reducing it:
- Focus on design. The best way to reduce material waste is to use less material from the beginning. Designing parts using methodologies like value engineering and design for manufacturability (DFM) can drastically improve yield.
- Recycle scraps and factory returns. Even if you can’t use the recycled material yourself, you can sell it to a factory that can, turning waste into profit. Recycling helps businesses contribute to a circular economy that eliminates waste in the manufacturing process.
- Optimize processes to utilize all available material. Could you use more of that sheet metal before scrapping it? Can those tool tips be sharpened and re-used, instead of discarded? Every scrap of discarded material represents an opportunity to improve process efficiency.
- Take a close look at your shipping department. Shipping materials are inexpensive compared to other manufacturing inputs, but their costs add up. Kimray, Inc. in Oklahoma improved their shipping workflow by reorganizing materials and equipment in the packaging area, cutting packaging time in half and achieving significant savings.
There’s no substitute for hands-on, real-world training. Take stock in your employees by training them on multiple processes; that way, they can help one another troubleshoot, act as substitutes, and provide relief during repetitive tasks. Furthermore, if everyone on the factory floor has a good grasp of the entire process from start to finish, they’ll have a better understanding of their roles within that process.
3. Quantify EverythingAssign a point value, or better yet, a dollar value, to every aspect of your manufacturing process. Material costs are obvious, but take into account man-hours, equipment wear and tear, and planned obsolescence to further quantify production. By assigning numbers to every aspect of manufacturing, you’ll make it a lot easier to see which areas need immediate attention.
4. Organize EverythingOrganization is key to an efficient workspace. Take a look around your factory floor. Are hand tools easy to find? Are waste products piling up in the corner? All tools, parts, materials and instructions should have a home, and every employee should know where that home is.
5. Standardize Work and ProcessesEveryone has their own approach to things, but in the world of manufacturing, there's not a lot of room for individuality. Even the simplest tasks should be standardized to maximize efficiency.
Start by making a checklist, and placing it in each workspace. Then, make sure that every employee who does a job in that workspace follows the checklist. This simple act can reduce downtime and improve overall product quality.
Beyond routine tasks, checklists are valuable tools for streamlining important processes and maintaining consistency and accuracy in decision-making – such as determining if casting is right for your product.
6. Implement Cellular ManufacturingTaken directly from the Lean Manufacturing playbook, cellular manufacturing is a method of improving efficiency by grouping similar or sequential processes. The methodology involves dividing workspaces into cells and assigning each cell a standardized set of tasks. The machines (and employees) in each cell might be capable of carrying out a wide variety of jobs, but allowing them to focus on a single job decreases downtime for tasks like re-calibration and tooling installation, while improving consistency and quality.
Cellular manufacturing also requires you to consider your overall manufacturing process as a series of separate steps, allowing you to zero in on opportunities to reduce waste. It also makes quantifying each part of the process a lot easier.
7. Proactively Manage Equipment FailuresWe all know that a toothbrush is a lot cheaper than a root canal, but not everyone carries this wisdom over to manufacturing. Preventive maintenance is the practice of performing maintenance tasks based on the known schedule of wear for a particular tool. The idea is to provide maintenance before it’s necessary, but not so often that it interferes with other tasks. Decide on the right schedule by consulting tool manufacturers, or by considering the time between past failures.
8. Strengthen Your Supply BaseWhen quantifying your manufacturing process, be sure to take a close look at your suppliers. If you notice that some are consistently providing you with better materials, parts or tools, reward them by giving them more of your business. This is another place where quantifying comes in handy: sticker price is hardly ever an accurate indication of the true cost of an input.
You may also find that customer-service attitudes vary greatly between suppliers. To maximize efficiency, it’s recommended to work with suppliers who have a customer-first attitude. They’ll be much quicker to respond if anything goes wrong, and much more willing to fix a problem on their end while minimizing your losses.
9. Engage Your EmployeesIf your process is plagued by downtime, look to your employees for answers. It’s only logical that the person responsible for carrying out a job might have a few ideas to make the process more efficient. On the other hand, it’s easy for executives and managerial staff, who are used to looking at the bigger picture, to miss smaller opportunities for improvement. It's important to open channels of communication so that employees can effectively communicate up the chain, whenever they have suggestions, comments or complaints.
Driving Efficiency Through Continuous Improvement
Implementing continuous improvement is the backbone of improving manufacturing efficiency over the long term. Continuous improvement is an ongoing effort to make incremental changes in your businesses’ processes to boost efficiency and quality over time. This involves regularly reviewing and refining your manufacturing operations – such as the methods discussed in this article – to identify areas for enhancement, as well assess whether the changes led to actual improvements. The primary goal is to save time and reduce costs while creating superior products with shorter lead times, fewer defects and minimal significant variations. Beyond these objectives, continuous improvement fosters additional benefits, including higher product quality, faster delivery, cost savings for customers, and increased reliability. This philosophy is a core component of Lean Manufacturing, a methodology focused on maximizing output and minimizing waste.
Manufacturing Efficiency in Practice
The Eagle Group, comprised of four metalcasting and machining companies in Muskegon, MI, is proud to practice Lean Manufacturing throughout our metalcasting and CNC machining facilities. Lean offers a set of tools to help manufacturers actively improve efficiency through systematic reduction of waste. Many of the above ideas are linked to Lean Manufacturing and methodologies like it.
For more on lean manufacturing and manufacturing efficiency, download our free resource below:
Tags: Lean Manufacturing, Processes, Manufacturing, Efficiency
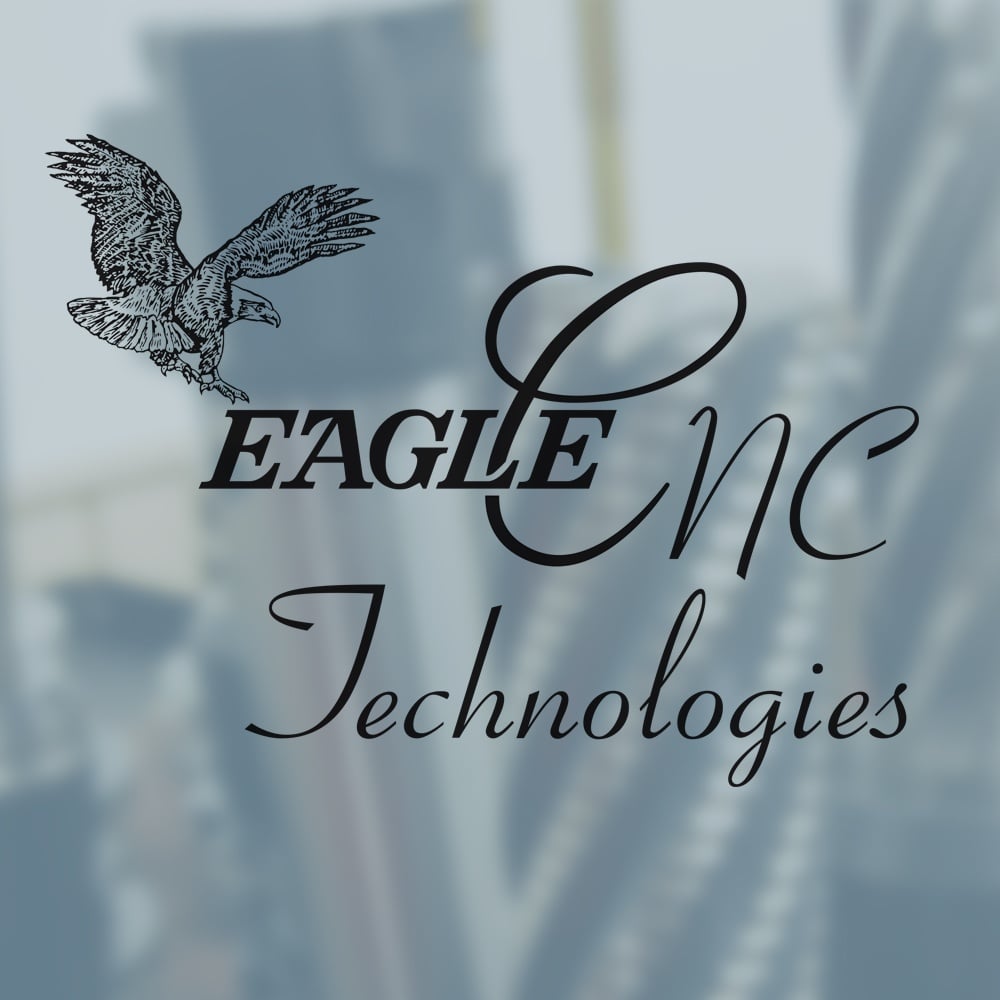