Metal Properties: Toughness
Toughness is a mechanical property that measures the amount of energy a material can withstand, or absorb, before fracturing. In the context of other mechanical properties, toughness for steel products represents a balance of strength and ductility.
As a material term, toughness can sometimes cause confusion: two very different materials can both be considered tough. For example, an iron anvil is tough because its strength is very high, and it resists fracture by maintaining its material integrity thanks to its strength. On the other end of the spectrum, silly putty is also a tough material, not because it’s strong but because it’s very ductile and will resist fracture until you pull it far enough apart that the two ends separate. Anvils and silly putty are very different, but they’re similar in that they are both tough, and they both absorb a good deal of energy before fracturing.
In the real world, most metal products need to be somewhere on the spectrum between the anvil and the silly putty. That means that for foundries and other manufacturers working with steel, optimal toughness means a balance between strength and ductility. The toughness of a material can vary markedly for different alloys, even those with similar chemical compositions or heat-treatment recipes. Toughness also varies within the same alloy under different testing conditions. For example, operating temperature augments toughness, as does speed of loading (the speed at which a loading force is suddenly applied to the material).
In this article, we’ll discuss how toughness fits within the bigger picture of mechanical properties for raw and machined cast parts: how an appropriate toughness level is determined for a cast part, how toughness is measured, and why measurement must take real-world scenarios into account.
Toughness Compared to Other Mechanical Properties
Because the words ‘tough’, ‘hard’, and ‘strong’ are sometimes used interchangeably in everyday speech, clearing up their precise definitions in the language used by material scientists, metallurgists, and engineers is an important task:- Hardness is a material’s resistance to localized deformation in the form of both indentation and abrasion forces. It’s a measure of how well a material resists deformation when you indent, pierce, hammer, scratch or drop a heavy ball on the same spot, repeatedly.
- Strength is a measure of material’s resistance to failure under conditions of an applied load. Strength’s two points of measurement are the yield point, at which a material begins to deform plastically (meaning it will not return to its original shape once the load is released). The second type of strength is known as tensile strength, which is the measure of maximum stress a material can withstand before fracturing.
- Toughness measures the amount of energy needed to fracture a material, and tough materials can be made tough either by virtue of strength, or ductility, or more commonly, a careful balance of the two.
A little more theory along with some practical examples will help clear up the difference between these closely related properties.
Tying the Properties Together: The Theory of Toughness
“A high-strength, low-ductility material can have the same toughness (or fracture resistance) as a low-strength, high-ductility one.” 1
Why is the scenario described in the above quote true? in the first case, a strong material is able to withstand significant loading before fracturing. But when it does fracture, it forms a brittle fracture, meaning that instead of pulling slowly apart before fracturing, it just snaps. While a low-strength, high-ductility material will already begin to deform plastically under a much smaller load, it will be able to withstand significant plastic deformation before actually fracturing. Technically, you could engineer the same toughness value from either one of these extreme cases. In other words, the total amount of energy absorbed can be made equivalent using either extreme. In both cases, the fracture point could be the same, but their mechanical properties will be different and they will deform differently.
How We Measure Toughness
Outlining how a toughness test is conducted will help clarify the difference between toughness and its neighboring mechanical properties.
Toughness Testing: Tensile Tests
To understand a metal’s toughness relative to strength and ductility, we can use the same data we obtain from a tensile test, which is commonly used to measure a material’s strength (see our Mechanical Properties: Strength blog for a full explanation of a tensile test). Once you’re a little familiarized with a tensile test, you’ll recognize how it’s graphed:
The y-axis represents the amount of stress applied to a material, while the x-axis represents the amount of deformation as a result of this stress.
Take a look at the green area, representing a very strong material: the stress curve climbs and climbs while the strain curve barely moves. This is because the steel is so strong, it hardly deforms at all until a lot of stress has been applied to it. Notice, however, that once it begins to deform, it doesn’t last long before coming apart, because it has very little ductility. In other words, it will form a brittle fracture. High-carbon steel is a strong material.
Now notice the blue-grey area, representing a very ductile steel. This specimen is stretchy. It begins to come apart at its weakest point quite quickly, but it will continue to maintain integrity under continually increased loading conditions (i.e., it will stretch) before fracturing. This low-carbon steel is a ductile material.
In-between, the orange area represents a tough material: it absorbs more stress before beginning to deform than the ductile material (but not as much as the strong material) and absorbs more stress before fracturing than the strong material (but not as much as the ductile material). This graph demonstrates how toughness is a utility value: it describes the balance of strength and ductility that the part requires to perform as intended in the field.
The key observation is this: toughness is the total area under the stress-strain curve from test initiation to fracture. In other words, if you measure the total surface area of the orange section and compare it to the surface areas of the grey and green sections, you will find it to be the largest of the three.
Toughness Testing: Impact Tests
Toughness must be understood from two different test scenarios: 1) how well a material absorbs energy before fracture under slow loading conditions (described by the tensile test section above) and, 2) how well a material absorbs energy when subjected to a rapidly applied load. Obviously, these are very different kinds of stresses, and this is where the real-world circumstances matter: what kind of stresses do we expect the part to be exposed to? Is it a slow tensile stress, or a rapidly loaded stress? Or both?
Therefore, we also have to understand a material’s resistance to rapidly applied loads. Several tests have been developed to evaluate a material’s toughness when subjected to a rapidly applied load, or impact. The most common, and the one we use most, is a ‘bending impact test’ called the Charpy test.
The Charpy test involves a pendulum that swings to break a small piece of sample material. After the pendulum breaks the sample, we can determine how much energy the sample (and therefore the material) absorbed by measuring the distance between the original height of the pendulum before its downward swing, and the height it reaches at the peak of its upward swing. The difference between these two heights correlates to the energy lost to the test specimen, and therefore indicates the amount of energy it absorbed.
In many cases, the values obtained from high-speed (dynamic) impact tests often fail to correlate with those obtained from the relatively slow-speed (static) tensile tests. This is why both methods exist, and why the expected operating conditions of the part must be taken into account when determining the most important test result. Concept-to-completion manufacturers like the Eagle Group have in-house equipment to carry out these tests, as well as personnel experienced in interpreting the results.
Toughness in Practice: Casting Tough Parts that Perform
What interests foundries and machine shops (and their customers) is what toughness means for metal parts. Using anvils and silly putty as examples of tough materials is OK for demonstrating the sheer diversity between the various tough materials, but in the real world of steel castings we need our products to be both strong and ductile, and, more importantly, to perform as expected in their operating environments.
Alloy Selection
Like all mechanical properties, toughness is part of alloy selection, which is based on knowing what the operating environment calls for. Thankfully, reference guides like the ASTM specify values for mechanical properties, including toughness. Predicting a part’s ability to withstand stress and absorb as much energy as possible is baked into the Eagle Group’s design process.
Operating Environment
As mentioned above, we need to know what kinds of stresses a part will be subjected to in the real world. We also need to know its operating temperature range. That's because another important ingredient in the metalcasting recipe is ductile-to-brittle transition temperature (DBTT). DBTT is a temperature threshold below which an otherwise ductile material will abruptly stop being ductile and will assume a brittle structure. In order to ensure that our parts will not fail due to crossing the DBTT, we rely on impact resistance test results that have been obtained at temperatures far lower than real-world operating scenarios.
Specialty Steels
If you’re in the market for a part with exceptionally high toughness and fracture resistance, there are specialty steels that are able to meet your specifications. If this is the case, it’s recommended to speak to a professional metallurgist (such as the team we have on our staff at the Eagle Group).
For example, steel parts requiring exceptional toughness would be thin parts that have been quenched and tempered. Here, we’re walking about parts that are designed with thin sections and that have strict flatness specifications on those sections. Having undergone very stressful structural changes through quenching and tempering, they must still be tough enough to withstand pressing, which is the mechanical flattening of a workpiece.
Common Casting Grades for Toughness
ASTM A216 and ASTM A352 are designed for low temperature and impact situations. In other words, they’re designed to be tough and remain tough at low temperatures. These grades have low temperature toughness minimums built right into them. They are known as ‘casing grades’ and are a common selection at the Eagle Group.
Specialty Steel vs Titanium
Looking at a broader picture, the toughest industrial metal is titanium. But of course, titanium is much more expensive than steel. There are many high-alloy steels that can compete with titanium on toughness. Often (and like with many other properties), toughness can be over-toleranced, meaning the original designs give excessive requirements for toughness, when in reality lower toughness would be more than adequate for the job. This over-tolerancing often excludes high-alloy steels and virtually limits options to only titanium parts, when in reality a specialty steel would be perfectly adequate for the job.
In short, if you’re in need of a really tough material for your application and assume only titanium can do the job, speak to us about the range of high-alloy steels we pour. We might be able to provide steel cast parts that perform as needed, at a fraction of the cost of titanium.
From a metal manufacturing perspective, the bottom line is that a tough material seeks to maximize the amount of energy it absorbs, and it does this by striking a balance between strength and ductility. Manufacturing tough materials is vital to heavy industry so that manufactured materials can be both strong and continue to hold up even after they’ve begun to deform. At the Eagle Group, defining a part’s required mechanical properties is an essential step in the design stage. From there, our expert casting process and quality control protocols ensure each part is delivered as specified, and that your parts possess the strength, ductility, and toughness you require.
To learn more about metals' mechanical and physical properties, check out our free ebook, Metal Properties and Their Applications in Metalcasting and CNC Machining. Click below to download:
1. Black, JT., & Kohser, Ronald A. (2019). DeGarmo’s Materials and Processes in Manufacturing (13th Edition). John Wiley & Sons, Inc (pg. 28)
Tags: Metallurgy, Metal Properties, Mechanical Properties
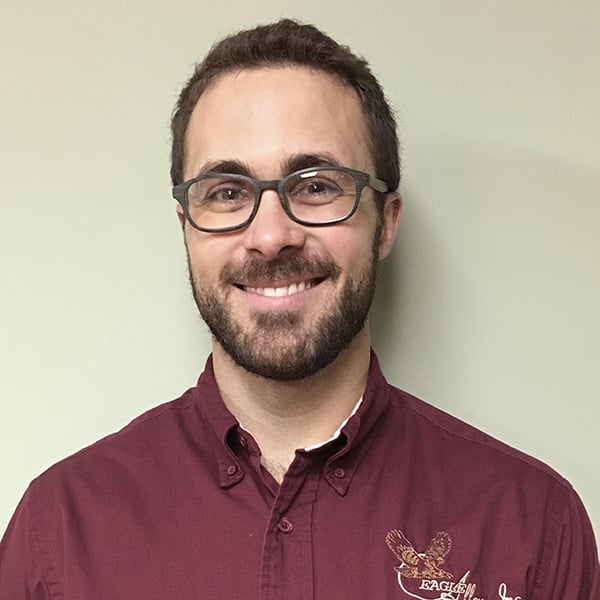
Written by Jason Bergman
Jason Bergman is Senior Quality Engineer and Metallurgist at Eagle Alloy. He has been with the company since 2013.