How the Investment Casting Process Works
Investment casting, sometimes known as lost-wax casting, is a metal forming method known for its ability to produce parts with tight tolerances, complex inner cavities and accurate dimensions.
As we discussed in our Introduction to Investment Casting post, the basic technique has existed for millennia. Over the years, innovations in equipment and methodology have kept pace with demand. Today, investment casting is one of the most popular forms of metal casting.
Read on to learn more about the unique process of investment casting.
Investment Casting Process Overview
- Manufacture the wax-injection tooling
- Produce wax patterns
- Assemble wax patterns to form a tree
- Produce the investment shell
- Dewax the mold
- Pre-heat the mold
- Pour the castings
- Clean the castings
- Finish the castings
Manufacture the Wax-Injection Tooling
In ancient times, wax patterns were made from beeswax, often by hand and just one at a time. Today, wax-injection dies are used to create a wax pattern for each casting produced.This tooling is a permanent fixture for each part, and is only replaced if it is damaged or if the design changes. The primary material used for the manufacture of the dies is aluminum, and they are manufactured primarily using CNC machining.
The shape of the die corresponds to a negative relief of the final product, with allowances made for shrinkage of the wax and the material of the final casting. As the wax used for the injection process is non-abrasive, dies can produce hundreds of thousands of shots with minimal maintenance and low risk of damage/replacement of the die.
Produce Wax Patterns
Once the wax-injection tooling is ready, pattern wax is brought to a temperature at which it is in a semi-liquid or a paste consistency. In this state, the wax is injected into the wax-injection die to form a wax pattern which is just slightly larger than the final casting being produced (due to shrinkage).
This injection process is repeated as many times as required to produce the number of patterns to fulfill order requirements.
The composition of investment wax varies, according to process or preference. Several U.S. patents have been issued for particular compositions of wax for use in investment casting.
Assemble Wax Patterns to Form a Tree
The tree, formed by combining several wax patterns along a common sprue greatly increases the efficiency of the investment casting process. Instead of casting one part at a time, these assemblies allow multiple patterns to go through the remaining steps together.
After a specified number of wax patterns as been produced, the patterns are affixed to wax bars to form the tree, sometimes referred to as a "cluster." The patterns are attached where the gates are located, which is where the metal will enter the individual casting. The tree must be of adequate size to provide enough feed metal to help provide a sound casting during the metal-solidification process.
The number of patterns assembled to form the tree is one of the primary factors in driving the piece price of the final casting: more patterns per tree can lead to a lower piece price.
Produce the Investment Shell
The assembled trees are then consecutively dipped in refractory slurries (liquid mixtures of heat-resistant materials) and coated with different sizes and types of sand, or stucco, to produce a ceramic shell around the wax. As the trees are coated, wax is left exposed at one end to facilitate removal in the following stage.
The first investment coat is critical to produce a superior surface finish, one of the advantages of the investment casting process. The first coat of slurry is applied by submerging the wax tree into a well-mixed vat of zircon-based slurry, with a consistency similar to latex paint. The assembly is then covered with zircon sand, then left to dry. After drying, the assembly is dipped in additional slurries and coated with increasingly coarse fused-silica sands, which are utilized to build mold strength.
Between each slurry/sand coating, the molds are left to dry between 8-24 hours. The mold-building step (producing the investment shell) of the investment casting process requires the greatest amount of time to complete.
Dewax the Mold
The fully coated ceramic mold is now ready to have the wax removed in order to pour the metal into the mold. In order to complete this task, the molds are placed into an autoclave with the wax-exposed end facing downwards. The autoclave is closed, and steam is injected into the autoclave in a matter of seconds which pressurizes the vessel and exposes the molds to temperatures exceeding 300F. The steam heats the wax, and the pressure of the steam is required to offset the pressure of the heating, expanding wax inside of the molds.
As the wax heats, it melts rapidly and drains quickly out of the open end of the mold. Nearly 100% of the wax is captured and recycled for use again in the wax-injection process. After a short time, the molds are removed from the autoclave, and are allowed to cool and dry.
This aspect of the process illustrates the versatility of investment casting. In other casting methods, molds must be opened (usually two sides are connected by a hinge) in order to remove the pattern. In investment casting, the pattern can simply be melted out, allowing for much greater detail in a seamless mold.
“Recycled Wax” Casting?
Due to improvements in process, wax from patterns is no longer “lost.” Instead, a large percentage of melted wax can be collected, purified and re-used in future patterns.Pre-Heat the Mold
The dewaxed ceramic mold is not quite ready to be filled with molten metal; as with any ceramic, it must be fired to bring it to an adequate temperature to accept pouring of molten metal. The molds are loaded into an oven that heats them to 1,900 degrees F and allows them to cure at that temperature for a certain amount of time. This firing process also burn -out any remnants of wax left-behind in the molds, which could cause casting defects.
This additional heating process accomplishes four tasks:
- Ensuring complete removal of pattern wax;
- Strengthening the mold walls;
- Allowing the molten metal to retain its liquidity as it travels through the mold;
- Offering improved dimensional accuracy by allowing the mold and casting to shrink together as they cool.
Pour the Castings
When the molds have been fired and held at the firing temperature, the metal to be poured is melted and prepared for pouring. Induction furnaces melt the metal by using electricity and magnetism to generate heat, and quickly liquefy metal ingot to temperatures nearing 3,000 degrees F. The chemistry of the metal is confirmed using a spectrometer, and pouring of the molds commences.
The method used for pouring depends on the material being used, the size of the mold and the facilities present. Variations include: gravity pouring, vacuum pouring, and vacuum pressure casting (VPC). In gravity pouring, the fired molds, still around 1,900 degrees F, are pulled from the ovens and brought to the furnace to be poured. The metal enters the mold cavity quickly, and as the molds are set-aside to cool, the metal inside the molds begins to solidify.
Clean the Castings
The now room-temperature castings are "cleaned" by removing the ceramic mold material and sawing or grinding away gates. The once strong ceramic mold has been spent and can be shaken away through vibration and blasting. Individual castings are cut away from the metal tree, and the gates (where the castings were attached to the tree) are removed through grinding operations. The castings are then sand blasted to remove any residual ceramic and to improve the surface finish for inspection.
Finish the Castings
The final steps of the investment casting process vary widely from part to part. Most castings receive some sort of heat treatment to improve the material's physical properties. Following heat treatment the castings are again blasted, and final-inspected prior to shipment. Many investment castings are near net-shape or net-shape products, meaning that they are dimensionally accurate enough to require little to know machining. Therefore, detailed gauging and inspection operations are performed prior to shipment to confirm the parts meet all customer requirements.
Learn More
This post is excerpted form our comprehensive guide to investment casting, the Investment Casting Process Guide. The guide is available as a free ebook download. Click below to get started!
Tags: Metalcasting, Processes, Investment Casting, Eagle Precision
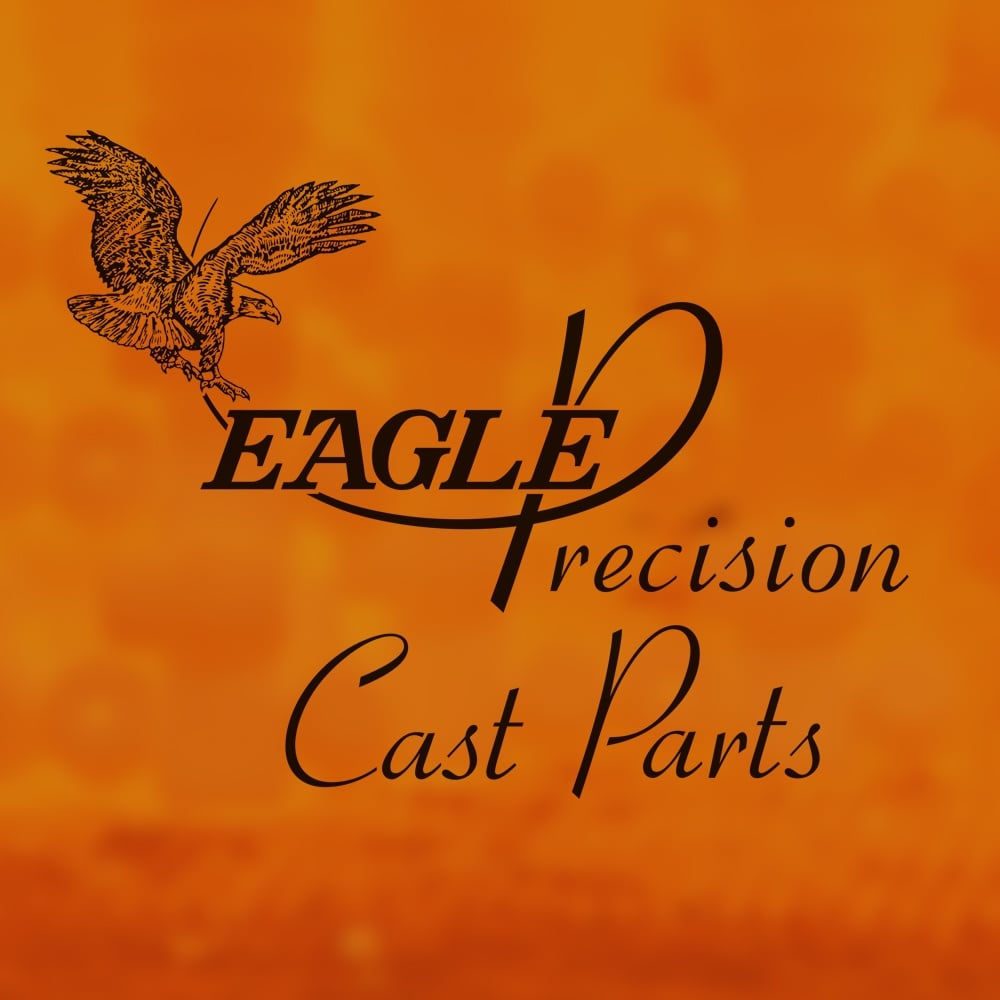
Written by Deb Pipoly
Deb Pipoly is President of Eagle Precision Cast Parts, an investment casting company located in Muskegon, MI.