How Shell Molding Compares to Other Metalcasting Methods
The shell mold process is unique and exhibits many advantages over other metal casting processes, but many people don’t fully understand its benefits.
In this installment of the Introduction to Shell Molding blog series, we will compare and contrast the shell mold process with investment casting and greensand casting methods. It is important to keep in mind that all processes have their own appropriate applications.
Based on your part's needs in terms of tolerances, production volume and surface finish, any one of these processes could be the ideal match.
Before continuing in this post, you may want to review the basics of metalcasting in our "Introduction to Metalcasting" blog post.
We make our comparison based on the following:
- Surface finish
- Dimensional tolerances
- Tooling costs
- Labor costs
- Typical production quantities
1. Shell Mold Casting Vs. Investment Casting
Investment casting is an ancient casting technique that has been used for centuries. Some may know it as “lost wax” casting, but the process has not changed significantly.
Investment casting uses wax to create replicas (patterns) that are assembled onto “trees” and then dipped into a ceramic slurry. The ceramic layers are allowed to air dry. Then, the wax is melted out, and the molds are preheated and then poured.
Despite lower initial startup costs (tooling), investment casting is often more expensive than shell molding due to higher labor costs.
2. Shell Mold Casting Vs. Greensand Casting
Greensand is a highly popular molding process used for making castings. In the greensand process, raw sand is mixed with organic clays. Unlike shell molds, greensand molds are not baked; rather, the process relies on compaction to bond the grains together.
The name “Greensand” has nothing to do with the color of the sand, but denotes that there is moisture present in the sand.
Automotive manufacturers often employ greensand casting, as it lends itself well to automation. The low cost of manufacturing and the small investment needed to start has made greensand casting a top process in high-volume scenarios.
The principle drawback of greensand casting is that the surface finish of parts is relatively rough. Shell molding, in comparison, allows for more intricate designs, smoother surface finishes and tighter tolerances.
Metal Casting Comparison Chart
Shell Molding |
Investment Casting | Greensand Casting | |
Tolerances |
+/- .03-.06 in. | +/- .005-.01 in. | +/- .06 in. |
Surface Finish |
Good | Very Good | Fair |
Tooling Costs |
High | Medium | Low |
Labor Costs |
Medium | High | Low |
Typical Production Volume |
High | Low | High |
For more information on shell molding, check out our other blogs from the series, Introduction to Shell Molding. Or download our free Shell Molding Process Guide.
Tags: Shell Molding, Metalcasting, Processes, Introduction to Shell Molding
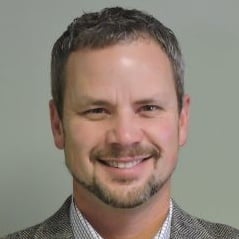
Written by Jeff Cook
Jeff Cook is Chief Sales and Marketing Officer for Eagle Alloy in Muskegon, MI. While enlisted in the Marine Corps Reserves, he began working at Eagle Alloy in 1986 as a snag grinder on 3rd shift after his father told him to “Get a job!” Jeff is past President of the American Foundry Society. His passions include educating young people on the careers and advancement available in the metalcasting industry.