How a New Drum Blast Eliminated a Production Bottleneck
Eagle Alloy takes pride in our reputation as a world-class metalcasting facility, and we make sure every batch of castings is ready for the customer before it leaves our facility. In most cases, the final step before packing and shipping is blasting. The blasting process removes burrs, flash and other excess metal from cast parts and improves their overall surface.
As part of our dedication to lean manufacturing, Eagle Alloy is always on the lookout for production bottlenecks. We identified a bottleneck in the blasting phase, and since nearly every part that leaves our facility is blasted, we knew we had an opportunity to significantly improve efficiency by optimizing our blasting station. In late 2020, we worked with Pangborn to install a brand new RotoDrum Blast Machine. This investment has essentially doubled our blasting capacity, reducing throughput times by 50%.
How Shot Blasting Works
Shot blasting is the process used at Eagle Alloy to prepare our cast products for delivery to our customers. In shot blasting, a machine hurls small abrasives – usually sized between a grain of sand and a BB – at high speeds onto the surfaces of cast parts. The abrasives clean the metal and leave parts with smooth, uniform surfaces.
Overcoming a Blasting Bottleneck
During a lean manufacturing audit, Eagle Alloy leadership discovered that we had an opportunity for improvement in our blasting station. The original tumble blast machine required several interactions from the operator in order to get through a load. It also leaked shot because the blast chamber was not tightly sealed. Even further, maintenance on the tumble blast required a significant amount of time due to a variety of moving parts that regularly needed servicing.
Our new drum blast solves all these problems at once. Operators are only required to select the blasting program from the machine's PLC and start the machine. The rest of the process is now automated, as the machine thoroughly blasts each load, shakes away excess shot, and then releases the parts for inspection. Because the process is so well automated, the operator can prepare the next load while the first load is in the drum blast. The blasting process itself is also markedly faster. According to Eagle Alloy foreman Rich Chase, "The old-style blast could do three loads an hour, so 24 loads a day. With this new one I can get 24 loads by lunch. It's really that efficient."
Pangborn representative Mike Pellowe isn't surprised by the success we're having with the RotoDrum. "As the parts are rotating and mixing in the drum, they actually do a figure-eight pattern," he says. "It's all made possible by the drum design. It's the shape of the inside."
Maintenance has been reduced significantly, because the drum blast is effectively sealed and contains so few moving parts. The Pangborn RotoDrum features a one-piece manganese drum that rotates to allow even blasting of all parts in the load. With almost no moving parts or wear points, Eagle Alloy has seen blast machine maintenance fall from 8 hours per week to an estimated 16 hours per year.
Pellowe also explains that, as part of the design, all media and parts are 100% in, 100% out. That means we go through a lot less shot, which is an added bonus that adds up to cost savings. Our employees' boot treads also benefit: leaked shot no longer litters the floor surrounding the blasting station.
Transferring the Benefit to Our Customers
Eagle Alloy's new drum blast provides a number of advantages to our customers. With reduced throughput times, we can deliver batches more quickly than before. We've also reduced our number of factory returns, as with the previous blast a small percentage of parts were bent and needed to be discarded. The new blast has no pinch points, and so even parts with a high bend risk can be blasted without incident.
As with all of Eagle Alloy's equipment investments, the new blast machine aims to improve our overall process, and to transfer those benefits to the customer by way of more consistent products with faster lead times.
Learn more about Eagle Group facilities:
Tags: Facilities, Equipment
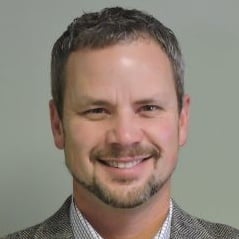
Written by Jeff Cook
Jeff Cook is Chief Sales and Marketing Officer for Eagle Alloy in Muskegon, MI. While enlisted in the Marine Corps Reserves, he began working at Eagle Alloy in 1986 as a snag grinder on 3rd shift after his father told him to “Get a job!” Jeff is past President of the American Foundry Society. His passions include educating young people on the careers and advancement available in the metalcasting industry.