Eagle Alloy Upgrades Casting Facilities with New Airset Sand Mixer
The Eagle Group produces a wide variety of cast and machined products for many industries. One of our strengths as a company is our ability to employ different casting processes. Eagle Precision Cast Parts, for example, specializes in investment casting, and Eagle Alloy specializes in shell molding. When you tour the shop floor at Eagle Alloy, you’ll see our shell molding machines busy at work, turning out most of our order flow. But that’s not all we do: Eagle Alloy also houses a robust airset (no-bake) molding line to support our shell customers.
While the bulk of what exits Eagle Alloy’s doors is shell molded, airset casting is another production method we employ for low quantity production runs, or for part numbers that are too big for shell molding. Airset casting is also known as no-bake casting because, unlike shell molding, the mold does not require heat to be set. Instead, the sand settles into a mold by introducing chemical recipes that fix the sand in place. Because airset casting uses a chemical reaction to set the mold, finer sands can be used; a process which results in superior surface finishes and tighter dimensional tolerances than competing methods like greensand casting.
And as proud holders of an ISO certification, Eagle Group companies are held to account by the world’s foremost standard-setting organization. “There are small airset foundries out there, but they don’t have our credentials. We’ve put in the time to become ISO-certified, and we want our shell customers to know that they can come to us for their lower-volume airset work also,” remarks Jeff Cook, Chief Sales and Marketing Officer at Eagle Alloy. Eagle Alloy is also PED certified, RoHS and REACH compliant, and ITAR and SAM registered. For more about why we value certifications, and why it should matter to manufacturing customers, check out our blog post, The ABCs of ISO.
In fact, airset casting has been a part of Eagle Alloy’s services since the company was founded in 1979. Since then airset technology has evolved, and although we’ve never had a problem delivering on product specifications, we felt it was time for an upgrade. In 2021 we added a Palmer M300XLD No-bake Sand Mixer to our equipment list, ensuring that Eagle Alloy is ready for another four decades of high-quality airset castings.
Why We Chose the Palmer M300XLD No-bake Sand Mixer
“Palmer has the best technology out there for airset molding,” notes Rich Chase, Product Manager at Eagle Alloy, and Eagle Alloy has already seen the difference compared to the original system. “Even people who know our foundry well, they come in and say, ‘that piece is airset casting?’ They’re surprised. They think it’s a shell molding, it looks so good.” These castings look so good thanks to a slew of innovations. Palmer is a pioneer in mixer technology, and with their M300XLD they’ve got the best of their new features on display.
As described above, airset casting is a metalcasting process that uses chemically bonded sand to create molds. Mixers like the M300XLD are a huge part of the process because they determine the consistency and quality of the sand/chemical mixture. Different parts require different mixes, based on the alloy being cast as well as the size and shape of the part. A good mixer helps foundry operators adjust a mix with precision and accuracy, allowing easy changeovers and consistent adhesion throughout a run of parts.
The M300XLD uses an air actuated system to coat the sand in binding chemicals. This mechanism is essentially a nozzle that knows exactly where to spray the binding agent to guarantee perfect dispersion across the mix, which means virtually no chemical or sand waste, and even better-quality castings. “Our molds are crisper, with sharper edges and better detail. The chemicals are set perfectly. We had good quality before, but I know this is better quality,” adds Rich.
And toggling between projects is now fully automated. Since different parts require different mixes, airset operators often move between different recipes with distinct sand and chemical measurements. With the flip of a switch, this machine recalibrates and starts pumping out the new mix. “You just hit a button – it measures the mix automatically, starts filling with sand and, boom, you’re making new molds in real time,” explains Jay Morrison, Sales Representative at Carpenter Brothers – a certified distributor of Palmer machines.
Enhanced Safety Features of Eagle Alloy’s New Airset Mixer
Rich Chase is also excited about the Palmer’s new efficiency and safety features. “We’re doing a lot more with less, which means faster throughput times for customers. And our workers are enjoying superior ergonomics with the Palmer. It’s a win-win. One safety feature we are really excited about is called the supercone.” Historically, one drawback of working with fine particulates like silica or zircon sand is the inhalation risk it poses to operators. In the past decade, airborne silica standards have been high on OSHA’s safety agenda, so new machines are built better equipped to protect workers. The supercone is a dust collection system – a high pressure vacuum that sucks the fine debris out of the air. In fact, the supercone has proven to be so effective at creating a safe and healthy working environment that Palmer actually markets them as a standalone product for retrofitting older machinery.
Eagle Alloy’s decision to upgrade our airset casting equipment is based on our fundamental goal of continuous improvement. All Eagle Group companies embrace innovation and strive to keep our equipment and processes up to date. Eagle Alloy will continue to focus on shell molding, but for large products and smaller runs, our shell customers can expect the best airset castings on the market with fast turnaround times and impressive surface finishes. In short, they’ll get what they’ve always gotten from Eagle Group: top-drawer technology and a trustworthy team behind the machines.
For more information on airset casting at Eagle Alloy, click the link below:
Tags: Eagle Alloy, Airset Casting, Facilities, Equipment
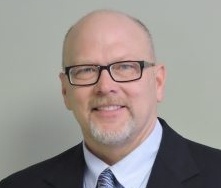
Written by Dave Fazakerley
Dave is Vice President of Manufacturing at Eagle Alloy in Muskegon, MI. He has been with Eagle since its inception in 1979.