The Benefits of Machined Part to Casting Conversion
Metalcasting is a highly versatile manufacturing process. In fact, many manufacturing professionals are not aware of just how versatile it is, and they continue to produce parts through other less efficient methods. While there is certainly a necessity for fabrication and machining in the metal manufacturing world, these processes can sometimes be replaced by casting.
We previously discussed one part's journey from fabrication to casting, showing how a part made by welding and bolting metal stock was re-engineered as an investment casting. Here we focus on a selection of parts that are fully machined from start to finish. Often these parts can be modified and produced as castings, as we have seen many times at Eagle Precision Cast Parts. By switching the manufacturing process from full machining to casting we can offer a range of benefits to the customer, including: reduced material waste, reduced part costs, faster production times and reduced man-hours.
What is Machined Part to Casting Conversion?
Machined part to casting conversion is the process of taking a product that is manufactured predominately through machining and altering it so that it can be made through metalcasting. Fully machined parts are often complex shapes with a number of critical characteristics, leading some manufacturers to believe that machining is the only process capable of achieving the desired results. However, metalcasting – and in particular investment casting – can also create intricate shapes, hollow cavities and even knife edges without the need for further post processing.
The Benefits of Machined Part to Casting Conversion
When switching the manufacturing process from machining to casting, customers can see a wide range of benefits. The most common are reduced scrap, lower part costs, faster lead times and fewer man-hours.
Scrap Reduction
Machining is a subtractive manufacturing process, meaning machined products are formed by removing material. Whether the machining facility uses turning, milling, boring, drilling or any other process, machining always results in scrap material. When done right, machining is a finishing process that finalizes critical surfaces, creates threaded holes through tapping or otherwise finishes a part without excessive scrap.
Eagle CNC performs a variety of machining operations on castings from Eagle Alloy and Eagle Precision, and the overall manufacturing process is designed to minimize discarded material. However, when parts are fully machined from bar stock, scrap can start to add up fast. Casting can minimize scrap by creating a part that is already near net shape, so only critical surfaces and threads need to be machined. Furthermore, any excess material produced in the casting process can be melted, purified and reused in another casting run.
Lower Part Costs
There are a number of ways casting can reduce part costs. One way is related to scrap reduction as discussed above: less material waste means more savings. Another way is a reduction in the number of overall processes: fully machined parts may require three, four or more separate machining processes, while a well designed casting can be near net shape. Third, casting processes are often designed to produce multiple parts at one time. Especially in investment casting, where several parts are placed along a sprue to form a tree, multiple parts are nearly always poured at once. With machining, multiple parts require multiple machines which can quickly raise the part cost.
Faster Lead Times
Casting does require some setup, including alloy selection, tooling, prototype production and testing, but once the details are hashed out parts can be rapidly produced with little or no downtime between runs. A well trained metalcasting team can continually produce castings, whether the process is shell molding or investment casting. Often, as mentioned above, multiple parts come out of a single mold. When all of these parts are near net shape and require few finishing processes, lead times can be drastically reduced.
Fewer Man-Hours
Both casting and machining require manual inputs from expert operators. Machining requires an operator to program the machine for each process, and to install and remove the part from the machine following each step. Casting requires operators to create molds, to pour alloys and to cut cast parts away from the sprue. The time savings in casting often comes from the ability to produce multiple parts from a single mold.
Machined Part to Casting Conversion: Getting Started
If your company manufactures parts entirely–or almost entirely–through machining, it would be worthwhile to explore a potential casting conversion. The best way to get started is to put your company's engineering department in touch with a casting facility. According to Deb Pipoly, "The bulk of [machined-part to casting conversion] customers come from tours in our plant. As we're walking through we always mention that the biggest opportunities are for 100% machined components or fabrications to single piece castings for internal savings. That gets people's minds going."
Even better, she continues, is if the casting facility is able to see machine drawings and assembly drawings for the product. One issue she often sees is that in-house engineers include standard tolerances in their design files because it's the default setting in the software they use. Sometimes machining is required in order to meet those tolerances, but a trained professional can often spot instances where the tolerances are far tighter than they need to be.
By understanding where the component goes and how it will be used, metalcasters like Eagle Precision can offer advice on where as-cast characteristics may be more than enough for the application. Knowledge of how the part will be used is valuable in informing the manufacturing strategy. "We understand the capabilities of our process," Deb continues. "We help customers incorporate the capabilities of our process into their design to make a better casting and hopefully less costly."
To learn more about Eagle Precision's casting process, Investment Casting, download our free ebook below.
Tags: Machining, Investment Casting, Productivity, Eagle Precision
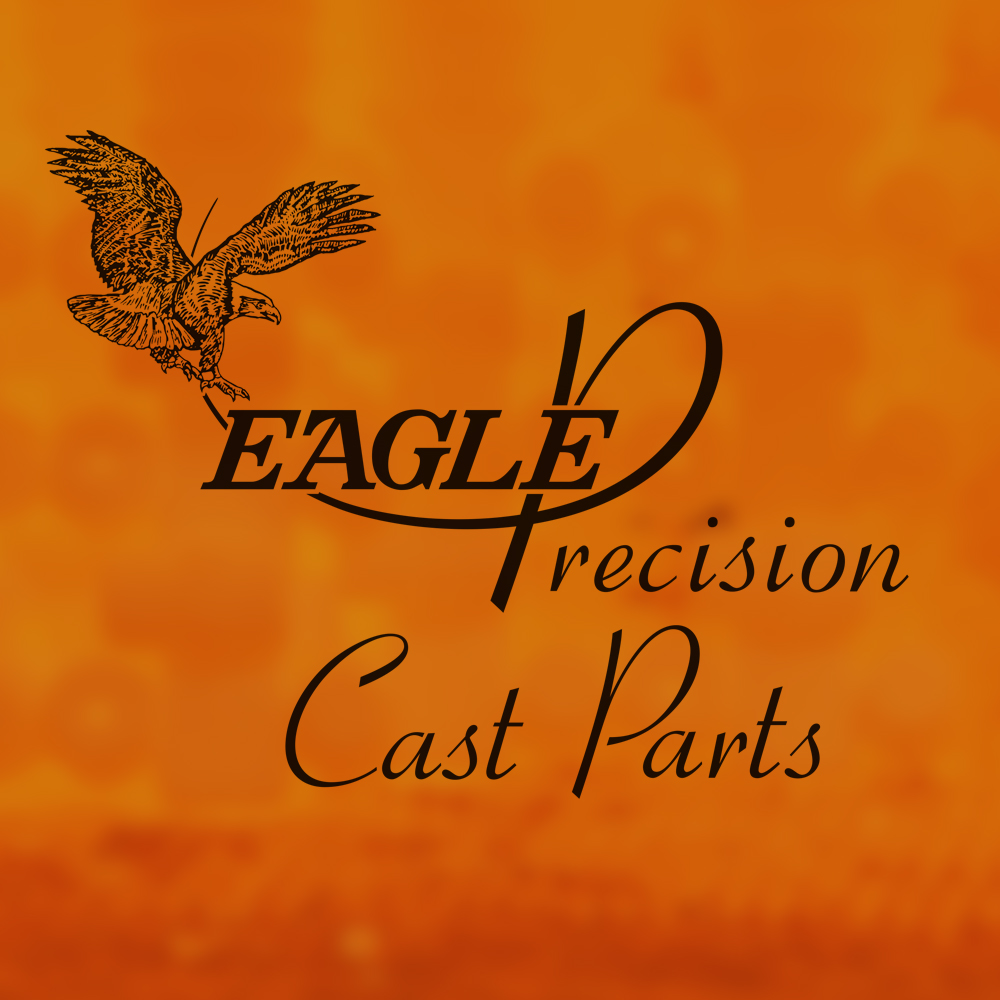
Written by Nate Neading
Nate Neading is Sales Technician at Eagle Precision Cast Parts, Inc. He has been with the company since 2010.