Getting Started with Permanent Mold Casting
Permanent mold casting is a type of metalcasting involving reusable molds. Whereas other casting methods, like sand casting and investment casting, use disposable molds, permanent molds last much longer and can be used to produce hundreds, or even thousands, of identical parts.
Every project can be matched with the ideal casting method. For non-ferrous castings with medium-to-high volumes, permanent mold casting offers a long list of advantages.
Making Permanent Molds
In most cases, permanent molds are made out of metal. The ideal metals for permanent molds have high melting points and exceptional thermal fatigue resistance. Permanent molds are often made of ductile metals, like cast iron or steel; bronze and graphite are other options.
In order to produce molds for permanent mold casting, manufacturers can use a number of metal forming techniques. Depending on the material used, these may include sand casting, investment casting or CNC machining.
Ductility and thermal fatigue
Thermal fatigue occurs when repeated heating and cooling cycles diminish the structural integrity of a material, often as a direct result of tiny cracks that form on the material's surface. Ductile metals, or metals that can more easily stretch without breaking, tend to have higher resistance to thermal fatigue.Another consideration in designing and producing molds for permanent mold casting is the material being cast. Permanent mold materials must have high melting points so that they can maintain solidity while molten casting material is poured in. As a result, permanent mold casting is almost always performed with non-ferrous metals. Aluminum is a great choice for permanent mold casting, because it can melt at less than half the temperature required for steel. If iron or steel is used for the mold itself, pouring in molten aluminum will not pose a significant risk of deforming the mold material.
Once a permanent mold is produced, it usually lasts through hundreds of parts. However, molds will eventually wear out, so it's important for manufacturers to be able to replicate the mold, and even keep multiple versions on hand in the foundry for seamless transitions during large runs.
Costs Involved in Permanent Mold Casting
Compared to sand casting and investment casting, tooling costs of permanent mold casting are high. The majority of costs go directly to producing the mold itself, which must be cast or machined like any other precision metal part. Once the mold is produced, however, per-part costs start to drop significantly.
Labor costs are less than sand casting and other disposable-mold techniques. Permanent molds can be reused as soon as each casting is ejected, with very little preparation. Beyond the energy required to heat the mold to temperature for the first casting, very little energy input is needed throughout the process. The mold retains the heat from each previous casting. Sand casting methods like greensand and airset also need only small amounts of heat, but they require other processes, like compacting and setting, for each individual part cast.
Permanent Mold Casting Characteristics
Parts cast using permanent mold casting can be held to very tight tolerances and display fine surface finish. Eagle Aluminum Cast Products, Inc. can meet tolerances as low as +/- .015 in, and offers surface finish of at least 300 RMS. In some cases, surface finishes can be further improved by applying a wash to the mold before casting.
Permanent Mold Casting Case Study
Eagle Aluminum Cast Products, Inc. provides both greensand casting and permanent mold casting services. For clients with high part volumes, permanent mold casting is almost always a cost effective choice. The case study below details EACP's experience developing a permanent mold workflow for a client with a relatively complex part with rapidly growing volumes. Take a look to gain more insight into working with a permanent mold casting foundry.
Tags: Metalcasting, Aluminum Casting, Eagle Aluminum, Permanent Mold Casting
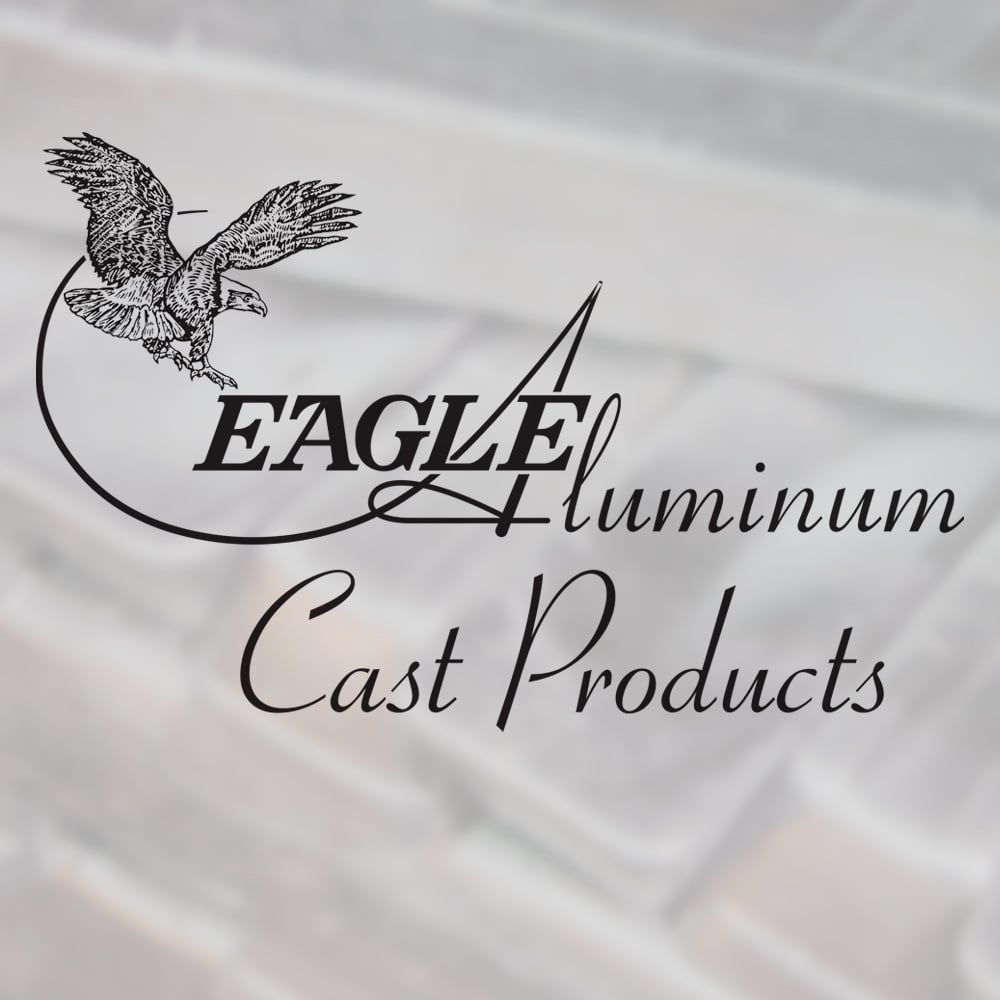
Written by Jim Smith, Jr.
Jim Smith, Jr. is the Technical & Sales Manager at Eagle Aluminum Cast Products in Muskegon, MI. Given his father’s career as a mechanical engineer, Jim grew up in foundries and often used castings his father brought home as toys. During his college years and into his first jobs, Jim developed skills in quality, engineering and customer service. Jim joined Eagle Aluminum in 2012 as a Technical Analyst and now manages all of the company’s Technical and Sales functions.