Aluminum Casting in Practice: A Case Study of Cast Aluminum Fan Blades
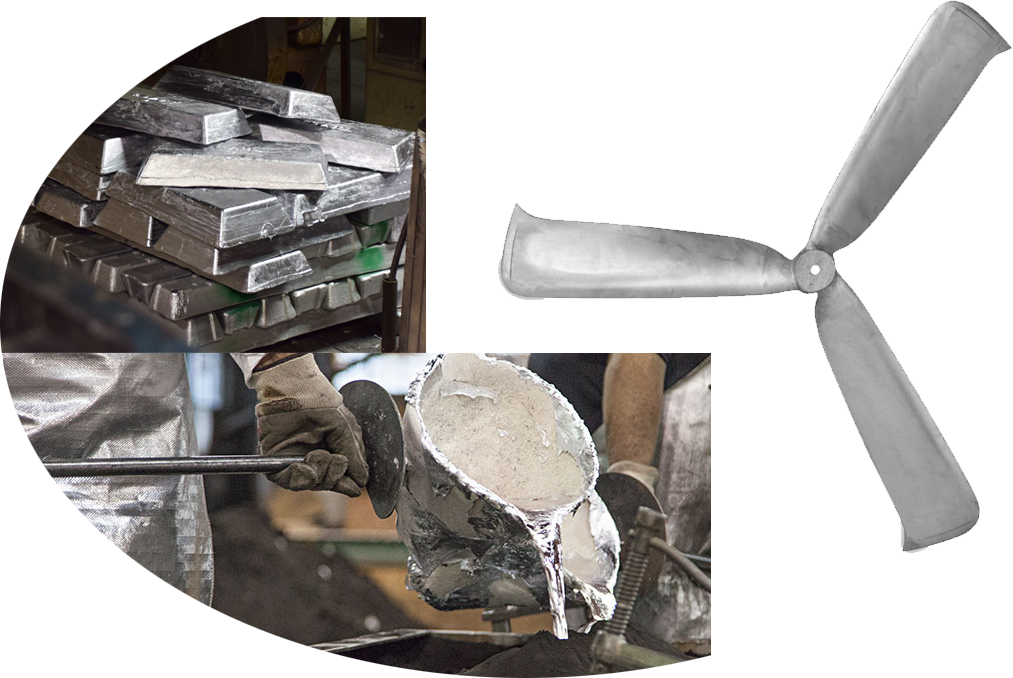
A major manufacturer of ventilation systems contacted Eagle Aluminum Cast Products, Inc. when demand was growing and they were ready to make a change.
The customer had already been producing 48” fan blades for agricultural use through green sand casting, but they’d outgrown that method. Demand projections suggested that permanent mold casting would yield lower per-part costs, with the added benefit of greater consistency.
Years later, EACP still produces fan blades for the customer through the process of permanent mold casting. Demand has increased even more, and product offerings have become more diverse. Read on to learn how EACP handles the design, production and delivery of this cast aluminum fan blade.
Design and production
EACP received a CAD file from the customer with part designs, and their engineers went to work to decide how to produce the part through permanent molding. EACP found optimal placements for feeding and gating. Because of the shape of the fan blade, they placed the gating near the hub–the thickest area–so that the metal could easily travel to the thinner blade edges.
Since permanent molding was the process being used, engineers also had to account for ejector pins and ejector tabs. Green sand casting doesn’t require these additions, because the casting is released by simply breaking the mold. In permanent mold casting, the mold is reused again and again, and the casting must be removed each time by pushing on ejector pins and/ or tabs. In order to ensure even weight distribution across all blades, EACP decided to place ejector pins inside the hub, and tabs at the end of each blade.
EACP makes use of advanced lean manufacturing to produce these parts. In fact, an entire fan blade can be produced by one operator, from molten aluminum to final delivery. Not only does EACP's use of lean manufacturing result in better quality and efficiency, it also leads to lower inventory costs and, ultimately, lower per-part costs for the customer.
Learn more about the Permanent Mold Casting process in our blog post here
Improving the production process
Initial production runs were successful, but over time the operators and managers at EACP noticed trends that could lead to improvement. Today, the streamlined manufacturing process results in a very low number of factory returns.
Maintaining Consistent Mold temperature: Some of the castings were forming defects called heat cracks, caused by excessive heat from the mold itself. he solution was to install a cooling system near the hub of the mold. Engineers at Eagle Aluminum also modified the design to allow a more direct connection between the hub and the fan blades, improving metal flow. These adjustments have removed all instances of heat cracking.
At the other end of the spectrum, EACP noticed that the blade areas of the mold, particularly farther out from the hub, were cooling too much between runs. To solve the problem, they added external burners to keep the blades heated.
Cooling Brace to Aid Solidification: EACP noticed that a number of parts were bending slightly as they cooled outside the mold, and they designed an innovative solution: a cooling brace. Engineers replicated the shape of the mold, and installed cooling elements to surround it. Now, each part is moved from the mold directly into the cooling fixture, which holds the part’s shape while it cools and solidifies. Instances of bending were reduced to zero. EACP has since applied this process to several other parts, with excellent results.
Finishing and Delivery
EACP is equipped to handle basic finishing on their castings. They saw off gatings and grind down runners, ejector pins and tabs. Then, they do a pre-balance check and conduct a visual inspection. After a part passes, it’s delivered to a local balancing company.
The balancing company is a specialized machine shop that focuses on products like this. In the casting, EACP has included tabs at the end of each fan blade. The balancing company grinds down the tabs with a high degree of accuracy to ensure a perfect operating balance.
After balancing, the fan blades are sent to the customer for final assembly. This particular customer handles the rest of the process in-house. They assemble the fan blade, the drive, the housing and any other auxiliary parts to produce an agricultural fan ready for installation.
Production Growth
Since Eagle Aluminum Cast Products started producing these parts, orders have increased in number and diversity. The part that started the relationship was first produced at a rate of around 3,000 parts per year. Today, that number averages above 10,000 parts per year. Thanks to the flexibility allowed by lean manufacturing practices, EACP can easily match demand and avoid excessive inventory.
The customer has also ordered an additional nine variations on the original part, comprising a range of different sizes and design variations.
Why aluminum Is the Right Material
Aluminum is the perfect material for this product for a number of reasons:
- Weight: aluminum’s low density leads to lighter parts. Lighter fan blades lead to more efficient ventilation systems. They also allow greater freedom in installing the ventilation systems, which can be placed on posts or non-load-bearing structural elements.
- Process: Permanent mold casting just doesn’t work with heavier, higher melting point alloys, like stainless or carbon steel. Even if the product would function with the added weight, the process would have to change. The customer initially made the switch from green sand, which could have accommodated different alloys. Stamping is another possibility. Permanent mold casting is generally done using steel or iron molds, and so using ferrous metals is often not an option.
- Corrosion resistance: These fan blades are often installed in agricultural environments, where they pump fresh air into enclosed spaces. They are often placed at the barrier between inside and outside, and are constantly subjected to the elements. Ferrous alloys, which are known for rusting, would not be ideal for these environments.
- Cost: EACP uses alloy 319 F for these castings. The cost of this alloy is very low compared to other alloys. Since EACP negotiates a fair market price for aluminum ingot, they can pass their savvy onto their customers in the form of savings.
Interested in aluminum casting? Click below to read more about alloys and casting processes used by Eagle Aluminum Cast Products, Inc.
Tags: Aluminum Casting, Aluminum, All About Al, Case Study, Eagle Aluminum
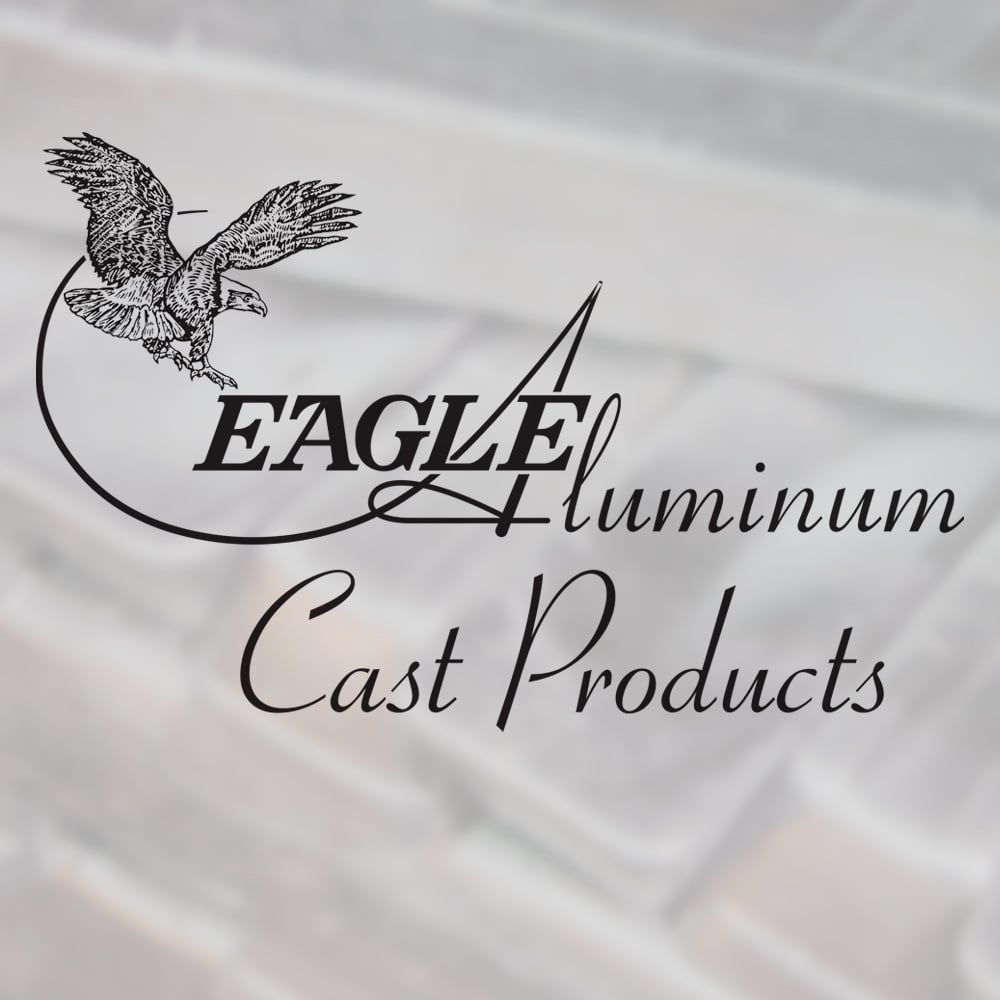
Written by Jim Smith, Jr.
Jim Smith, Jr. is the Technical & Sales Manager at Eagle Aluminum Cast Products in Muskegon, MI. Given his father’s career as a mechanical engineer, Jim grew up in foundries and often used castings his father brought home as toys. During his college years and into his first jobs, Jim developed skills in quality, engineering and customer service. Jim joined Eagle Aluminum in 2012 as a Technical Analyst and now manages all of the company’s Technical and Sales functions.