All About Al: Aluminum's Winning Properties
Recently in our All About Al blog series we discussed aluminum's history and origins. Now we're getting deeper into why aluminum is the perfect material for manufacturing such a wide range of products.
Aluminum owes its versatility in manufacturing to a unique set of properties. These include:
- Low melting temperature
- Excellent malleability
- Light weight
- Corrosion resistance
Aluminum Has a Low Melting Temperature
Stainless steel melts at temperatures above 2,500 degrees F, and steel castings are often poured at temperatures exceeding 3,000 degrees F. Pure aluminum, on the other hand, melts at a much-cooler 1,221 degrees F.
Actual melting and casting temperatures of aluminum depend on other metals mixed into the alloy, but aluminum alloys can generally be cast at less than half the temperature of ferrous alloys (alloys containing iron, like steel).
Because of its lower melting temperatures, casting processes for aluminum alloys are less energy intensive than those for ferrous alloys. Setting times are also reduced, improving factory throughput and further decreasing costs.
Aluminum Has Excellent Malleability
Malleability is a substance’s ability to be deformed without cracking or breaking. Compared to other material groups, metals generally have high levels of malleability, with gold coming in first place. Aluminum is no slouch either, especially considering its other positive attributes.
An excellent example of aluminum’s malleability is the ever-present aluminum foil. Aluminum foil is made by squeezing high-purity aluminum through a rolling press, reducing the metal’s thickness to a specified measurement. The kind of everyday aluminum foil you probably have in your kitchen can be as thin as .00017 inches–about 400 times thinner than an average human hair.
Aluminum’s malleability is also why lightweight tubing can be made out of aluminum. Tubing is made through extrusion, which removes the center of a piece of aluminum and leaves the sides. A wide variety of industries--from bicycles to lawn furniture--take advantage of aluminum tubing to offer strong, lightweight products.
Aluminum Is Light Weight
Compared to iron and steel, aluminum is much less dense. That means that a finished aluminum product will be much lighter than an iron or steel product of the same shape.
Again, actual measurements differ depending on alloying elements, but a good rule of thumb is that aluminum is around 2.5 times less dense than steel. While aluminum is not as strong or hard as steel, its light weight offers design flexibility. For example, a 5-lb aluminum bicycle frame can contain 2.5 times more material by volume than a 5-lb steel bicycle frame.
Aluminum Has Excellent Corrosion Resistance
In cases where a product will be exposed to weather and the elements, aluminum comes in ahead of the pack.
Many metals produce an oxide layer covering their external surfaces. Oxide layers are formed when compounds react with water, or oxygen in the atmosphere.
Rust and other forms of oxidative corrosion are commonly seen in metals that form less stable oxide layers. These metals react with oxygen in the same way that aluminum does, but rather than maintaining a stable, microscopic thickness, their oxide layers continue to grow until they are visible with the naked eye.
Aluminum, on the other hand, forms a relatively stable oxide layer, preventing it from further reacting with oxygen. If the surface of aluminum is damaged, the layer “heals” itself, re-forming almost immediately. It’s kind of like Wolverine’s skin.
Is Aluminum Right for Your Casting?
Aluminum is an exceptional metal, but whether or not it’s the right material for your product depends on a broad range of factors. Get a comprehensive overview of aluminum's history in manufacturing, forming techniques, best practices and case studies with our guide, Manufacturing with Aluminum.
Tags: Aluminum Casting, Aluminum, Materials, All About Al
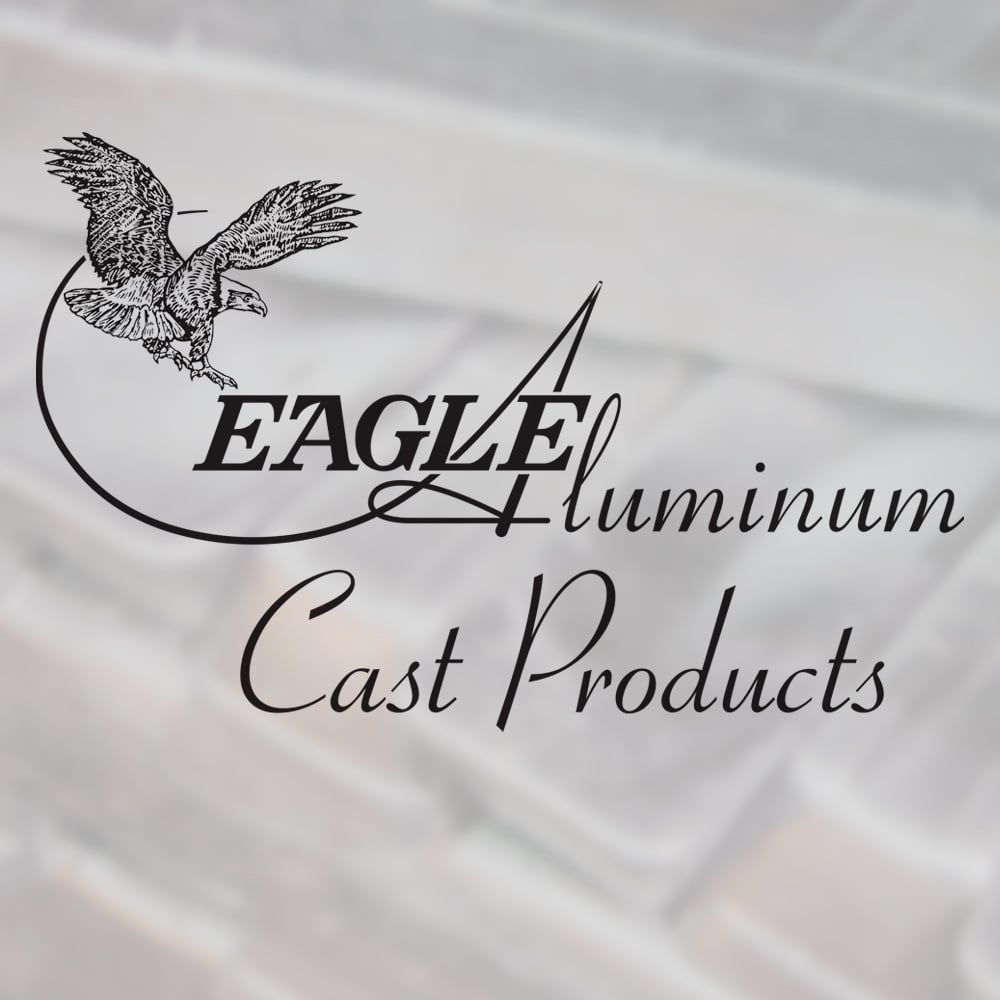
Written by Jim Smith, Jr.
Jim Smith, Jr. is the Technical & Sales Manager at Eagle Aluminum Cast Products in Muskegon, MI. Given his father’s career as a mechanical engineer, Jim grew up in foundries and often used castings his father brought home as toys. During his college years and into his first jobs, Jim developed skills in quality, engineering and customer service. Jim joined Eagle Aluminum in 2012 as a Technical Analyst and now manages all of the company’s Technical and Sales functions.