Eagle CNC on the Rise
Just a year since being fully acquired by Eagle Alloy, the Eagle CNC team is showing their resilience and ability to thrive in their new environment
It’s been a year since Eagle Alloy fully acquired Eagle CNC, and a lot has changed. The companies are growing closer together in terms of shared systems and shared goals, and both are benefitting immensely. From improved efficiency on the shop floor to more streamlined scheduling, the partnership has opened up a world of opportunities for shared growth as a holistic, concept-to-completion manufacturing team.
Eagle CNC as we know it today began as Westech Corp in the early 1980s. About a decade later, Westech founder and owner Bill Seyferth entered into a partial merger with Eagle Alloy. Westech changed its name to Eagle CNC, but still functioned almost entirely as an independent entity. The two companies certainly contributed to each other’s success, with Eagle CNC providing superior machining capabilities and Eagle Alloy sending consistent work to the machine shop, but at the end of the day they were separate companies with a supplier-customer relationship. The full merger that went into effect in July of 2023 changed all that: Eagle CNC and Eagle Alloy are no longer independent. We are now part of the same ecosystem, doing whatever we can to help each other succeed, and to allow our customers to have a complete source for finished, high-quality products.
“Whether we got the work or we didn’t, the piece price really drove that,” says Jason Clark, who came on as President of Eagle CNC after the merger. “We were more like a standard supplier. Now engineering is communicating, I’m communicating directly with sales, being part of the team or a coworker with Eagle Alloy.”
Some of the most effective changes made since the merger have been behind the scenes. By moving Eagle CNC’s administrative system from the Shoptech E2 Manufacturing System to B&L Informations Systems Odyssey, the two companies can now essentially mirror their operations. Eagle Alloy and Eagle Precision have already been using Odyssey for years and have a dedicated Odyssey expert on staff. Not only can Eagle CNC benefit from Eagle Alloy’s experience with the ERP software, but they can now tune their systems to echo schedules, material costs, process cycles and other parameters that would be confidential between independent companies. While it’s an ongoing process, Jason is already looking forward to the benefits provided by the new ERP: “It takes a good year to vet it and get everything right, but eventually we can start using the capacity planning portion of Odyssey to help us predict what will happen month to month, down to the part.”
New equipment has also played a role in Eagle CNC’s growth since the merger. Previous ownership and management had a great track record of investing in equipment throughout the history of Westech and Eagle CNC, and that pattern has remained as part of Eagle CNC’s ethos. The shop floor has already taken on two new robotic cells, one with an Okuma 2SP-2500H and one with a Haas UM C500SS, improving overall capacity and making it possible to automate tasks. Other new machines adopt the latest in machining and programming tech, like the DMG Mori NTX 2500 and the DN Solutions PUMA 2600SYB. These new machines are faster, more accurate and more user friendly, maintaining Eagle CNC’s position at the forefront of machining technology.
As Higginson said, “Originality is simply a pair of fresh eyes.” The same applies to Eagle CNC’s post-merger management. As a former outsider, Jason has been able to tackle a number of challenges that may have simply gone unnoticed in the past. He upgraded the machine coolant to a synthetic variety that doesn’t smell bad – a common problem in machine shops, but an easy fix that boosts employee morale. He invited machine tool vendors to visit the shop and present the latest tool technology to free up staff from complicated tooling and fixture work. He shuffled staff to highlight talents and aptitudes, moving people between quality, sales, machining, tooling, and maintenance to create a better shop-wide balance. The addition of two staff members dedicated to maintenance has paid off well, allowing the company to keep the shop and equipment in working order virtually continuously.
Employees have played a huge part in making Eagle CNC’s transition smooth and effective. Rearranging roles within the company can be challenging, but employees are embracing the change and thriving in their new environments. One employee in a new role ensures that tooling fixtures are fully optimized; another has managed to shave 5 to 20 minutes per part from the programs under his supervision. Jason has seen the transition firsthand, starting from day one: “The team has shown a remarkable ability to change and grow to new levels in less than a year’s time,” he says, “and there’s more to go, but we’ve made a lot of headway in just a short period.”
Compensation structures have also changed, giving employees even more motivation to succeed. As of November 2023, Eagle CNC employees started to accrue the threshold of 1,000 hours to qualify to take part in Eagle Alloy’s Employee Stock Ownership Plan (ESOP). The ESOP turns everyone who works for the company into a part-owner. Every employee now benefits from owning stock, and benefits from profit sharing. In fact, following measures to tighten cash flow, improve efficiency and raise throughput, Eagle CNC employees received their first quarterly profit sharing check in years, and they’ll continue to receive them for the foreseeable future.
This is not to say that Eagle CNC was not a successful company in the past. Under Bill Seyferth’s leadership, followed by his son, Nik Seyferth, the company saw 26-27% growth year over year – more than any other Eagle Group company. But with the companies combined, there are many opportunities to share experience and best practices, streamlining operations and boosting productivity. According to Nic Tarzwell, who is Eagle Alloy’s CTO and has worked closely with Eagle CNC following the merger, “We now have the ability to constructively help and coach [Eagle CNC] to have success with us, not as two competing entities, but to make sure we both succeed.” Through profit sharing and ESOP, all Eagle CNC employees can benefit from the merger.
Today, Eagle CNC continues to put record months on the books, and Jason estimates that with a few more hires, they’ll have the capacity to double their yearly revenue. Seeing these positive trends provides even more motivation for Eagle CNC staff to put in their best work on the shop floor, in the head office or on the sales circuit. Having solidified its place as part of the Eagle Group team, Eagle CNC is moving forward rapidly. As Nic Tarzwell puts it, “This is a new beginning, with a solid foundation.”
See Eagle CNC's team in action in the gallery below:
Learn more about what Eagle CNC Can do:
Tags: CNC Machining, Eagle CNC
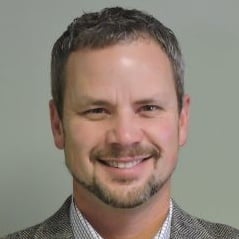
Written by Jeff Cook
Jeff Cook is Chief Sales and Marketing Officer for Eagle Alloy in Muskegon, MI. While enlisted in the Marine Corps Reserves, he began working at Eagle Alloy in 1986 as a snag grinder on 3rd shift after his father told him to “Get a job!” Jeff is past President of the American Foundry Society. His passions include educating young people on the careers and advancement available in the metalcasting industry.