What Is Lean Manufacturing?
Lean manufacturing helps manufacturers improve efficiency by eliminating waste in the production process, but what exactly is lean manufacturing? Is it a product, a procedure, a religion?
None of the above. Lean manufacturing is an adaptable set of “tools” that can be applied to any system of manufacturing–whether that system produces spring coils, jet engines or blog posts. It starts with identifying waste in a production process, and then focuses on eliminating that waste bit by bit until production is as streamlined and efficient as possible.
Background and History
Lean manufacturing has roots in Henry Ford’s assembly line, but Japanese entrepreneurial scientists–namely those working at Toyota–are directly credited with developing the lean manufacturing tools we use today. While the term, “lean manufacturing,” wasn’t coined until 1988, Toyota started developing its tools and methodologies as early as the 1930s.
Ford's Assembly Line
While Ford’s manufacturing process was certainly revolutionary, it was anything but perfect. By implementing what he called “flow production,” characterized most visually by the assembly line, Ford’s automotive fabrication plant was able to churn out car after car with a high degree of quality and precision. If Model Ts were the only car Ford ever made, they could have stopped right there. The problem, however, was variety. While flow production all but eliminated human error and manufacturing defects, it was nearly impossible to adapt the process to manufacture anything but that beautiful, black Model T.
Toyota Production System (TPS)
Starting with Ford’s system, engineers at Japanese automaker, Toyota, began the process of perfecting flow production. The system they developed, called the Toyota Production System (TPS) formed the basis for modern lean manufacturing.
Since TPS emerged, lean manufacturing has become as academic as it is practical. In fact, the term, “lean manufacturing,” was coined in an MIT Master’s thesis. A wide variety of approaches now present manufacturers with different sets of tools, and these approaches themselves are constantly in flux. Lean manufacturing can be seen as the intersection of theoretical and applied science in manufacturing.
While quite a lot has changed over the decades–both in manufacturing technology and products themselves–the basic goals of lean manufacturing remain the same: eliminate waste, increase throughput speed and improve quality.
For more on lean manufacturing history, tools and best practices, download our Lean Manufacturing Timeline below:
Tags: Lean Manufacturing, Manufacturing, Efficiency
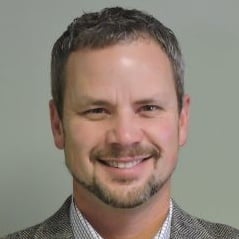
Written by Jeff Cook
Jeff Cook is Chief Sales and Marketing Officer for Eagle Alloy in Muskegon, MI. While enlisted in the Marine Corps Reserves, he began working at Eagle Alloy in 1986 as a snag grinder on 3rd shift after his father told him to “Get a job!” Jeff is past President of the American Foundry Society. His passions include educating young people on the careers and advancement available in the metalcasting industry.