After Casting: Perfecting the Blasting Process
After a casting solidifies in the mold, the part undergoes a number of post processes to prepare it for delivery. One of the most commonly used post processes is blasting, an intensive cleaning process that removes debris and excess material from castings. At the Eagle Group, blasting plays a pivotal role in prepping casting surfaces for delivery or for further processing. Our latest investment in state-of-the-art stainless-steel grit and an optimized media blasting process is paying dividends for our customers and our employees by providing cleaner parts, less oxidation, and a safer workplace.
But getting to this point has been a years-long journey. Here's how we got here.
To begin, it's important to note that blasting commonly takes place at two stages in the casting-production process: after casting, and after heat treatment.
- After casting: to remove sand prior to gate and riser removal from the casting. We can think of this as process blasting.
- After heat treatment: To remove surface oxides and scales from the casting to bring about a cosmetically uniform part. We can think of this as finishing blasting.
The goal of blasting is to remove debris, rust and other extra material or cosmetic imperfections from the surface of castings (Note: some of these blemishes and imperfections are known as burrs and flashes in the industry). With sand mold castings, sand can cluster on the surface of the material in a very hardened state, so any blasting technique must be able to propel a large amount of energy at a casting surface in order to remove these caked-on sections.
In other words, blasting is a methodology for removing ‘stuff’ from the casting surface, which also means we occasionally use blasting to return the surface of our parts to a clean slate: for example, to remove a faulty paint job or rework a powder coating.
Types of Blasting: Sand vs Shot Blasting
First, let’s take a look at the various types of blasting encountered in a foundry.
The key to effective blasting is making sure the media being flung at the casting’s surface is traveling with enough momentum to remove lingering debris. There are broadly two industrial methods foundries use to blast and clean cast products: sand blasting and shot blasting.
Sand Blasting
Historically, sand blasting has been the name for the process of propelling an abrasive media using compressed air (in other words, using an air hose to fling a high-pressure stream of silica sand at an object). For various health and safety reasons, the use of silica ‘sand’ in ‘sand blasting’ has been phased out in many foundries – OSHA and EPA regulations, although not technically prohibiting it, have made the hurdles to using silica sand so high that it’s practically unfeasible. Eagle Alloy does not use silica sand for blasting of any kind.
The practice of using a high-pressure stream to clean products is still very much in use, it’s just that the media has changed. Somewhat confusingly, when a blast media is being sprayed from a high-pressure handheld nozzle onto a casting surface, this is still referred to as "sand blasting," even if the media is not silica sand. At the Eagle Group, we opted to update our terminology: when we are using a handheld blaster we now call it ‘media blasting’, a redesignation that we believe is a better reflection of what the process actually is today in the post-silica sand era.
Shot Blasting
Different from the pressurized stream of sand blasting, shot blasting propels an abrasive media at high speed against castings’ surfaces using a centrifugal or mechanical force. The rapid impact of the blasting media against the metal surface removes excess debris.
There are different types of shot blasting units. There are hanger units that hold parts up while they move through a blast stream. There are barrel units that utilize a large rotating drum, and tumble units in which parts tumble downwards under blasting pressure in a rotating chamber. Another common method is belt blasting, which is a little like the conveyors at security checkpoints: you lay the parts on the belt, and they get pulled through a blast inside the unit. The two shot blasting configurations we use most at Eagle Alloy are barrel blasts and tumble blasts. These units are responsible for processing the majority of our parts, but not all of them: we also have hanger and belt style blasts to supplement our blasting capacity. We use barrel and tumble blasts more than other methods because they are the most efficient and flexible methods.
Although shot blasting is part of a foundry’s standard routine, using state-of-the-art equipment isn’t necessarily standard practice. However, having an optimized equipment setup can significantly increase efficiency. That’s why we installed a RotoDrum Blast Machine. The addition of this barrel-type shot blasting unit went a long way in resolving a bottleneck.
Upgrading Media Blasting Facilities at Eagle Alloy
Although we’ve always used blasting, we’ve made notable investments recently: first, we built a dedicated, fully ventilated media blast room. And more recently, we upgraded the actual media used to blast the castings from a carbon steel to a stainless steel formula.
Media Blasting at Eagle Alloy Today
The Eagle Group’s practices have evolved alongside the latest technological developments in the industry, with minimal lag between the newest product launch and rolling out that product across the Eagle Group. That goes not only for blasting, but for processes throughout the casting process: melting, pouring, grinding, sand reclamation and heat treatment. We pride ourselves on continually offering the best blasting solutions available.
The Latest Upgrade: Stainless-Steel Grit
The name ‘stainless-steel grit’ gives away its two main advantages over previous blasting media: the first is in the grit. What exactly is grit? The grit refers to little chopped up pieces of wire, shapes with jagged edges that interact with the surface of the castings differently from spherical or rounded shot. The jagged shape of grit makes it a particularly impressive and aggressive cleaning media compared to other alternatives.
The next clue in the name is the material: stainless steel. To quote Nic Tarzwell, Eagle Alloy’s Chief Technology Officer, a traditional carbon steel blasting media “essentially increases the free-iron content on the surface, which can increase rusting potential on a stainless steel product.” However, stainless grit is a win-win. As Tarzwell explains: “by matching a stainless product with a stainless grit, you remove that potential to deposit free-iron on the surface which reduces rusting potential. Basically, we’re using a higher quality blasting media of taking a cheaper carbon steel and blasting that on top of stainless. There’s no performance downside to stainless media used to blast any carbon steel product.”
The third advantage is perhaps the most important: important: the new stainless-steel grit makes for a much safer working environment. This new media is not a particulate, so it creates a less dusty and therefore healthier environment for our workers. And this is especially important since we built a dedicated blasting room where we do all of our media blasting in a contained environment.
Does SS Grit Have Drawbacks?
There are virtually no drawbacks to using this upgraded material. But completing the upgrade did require a significant capital expense: “I would say it's probably a 10x investment relative to the old media, but now we're going to get 100x uses to life, if not close to a 1000x. As long as we don't let the shot walk away in the castings and slowly deplete it over time, the product should far outlive the castings,” Tarzwell summarizes. With that in mind, there is a huge incentive to recycle the grit as effectively as possible.
Blasting and Lean Manufacturing
In order to preserve as much blast media as possible, we set up our dedicated blasting room to optimize material reclamation. Nearly every morsel of the grit we use is reclaimed and recycled. And because the new media has a very long in-use lifespan, the combination of quality and lean manufacturing means our new process results in little to no material waste.
Overall, blasting is a crucial step in the metalcasting process, ensuring that castings are clean and free of imperfections. At the Eagle Group, we have invested in the latest technology and techniques to achieve exceptional results. Our recent upgrade to stainless-steel grit has further improved deburring, descaling, cleaning, and surface preparation, while also providing a safer working environment. The long lifespan of the new media and the ability to recycle it effectively make it a valuable addition to our lean manufacturing process, and a vital contributor to meeting customers’ expectations.
Tags: Lean Manufacturing, Eagle Alloy, Equipment, Continuous Improvement, Blasting
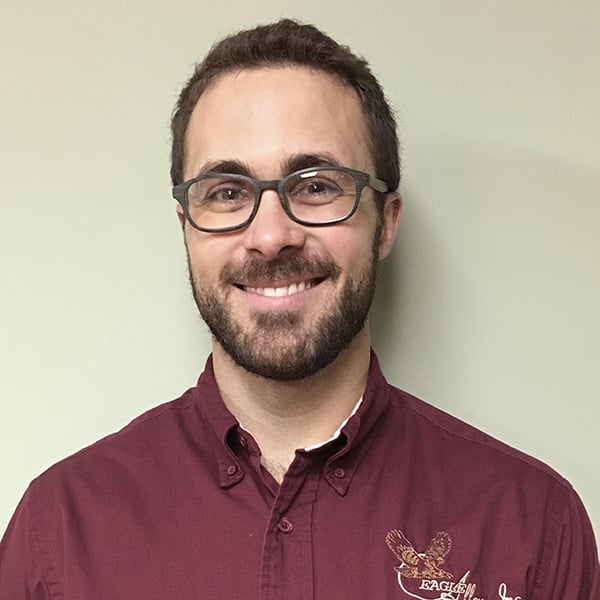
Written by Jason Bergman
Jason Bergman is Senior Quality Engineer and Metallurgist at Eagle Alloy. He has been with the company since 2013.