Measuring Standards: From Pharaohs' Forearms to the Speed of Light
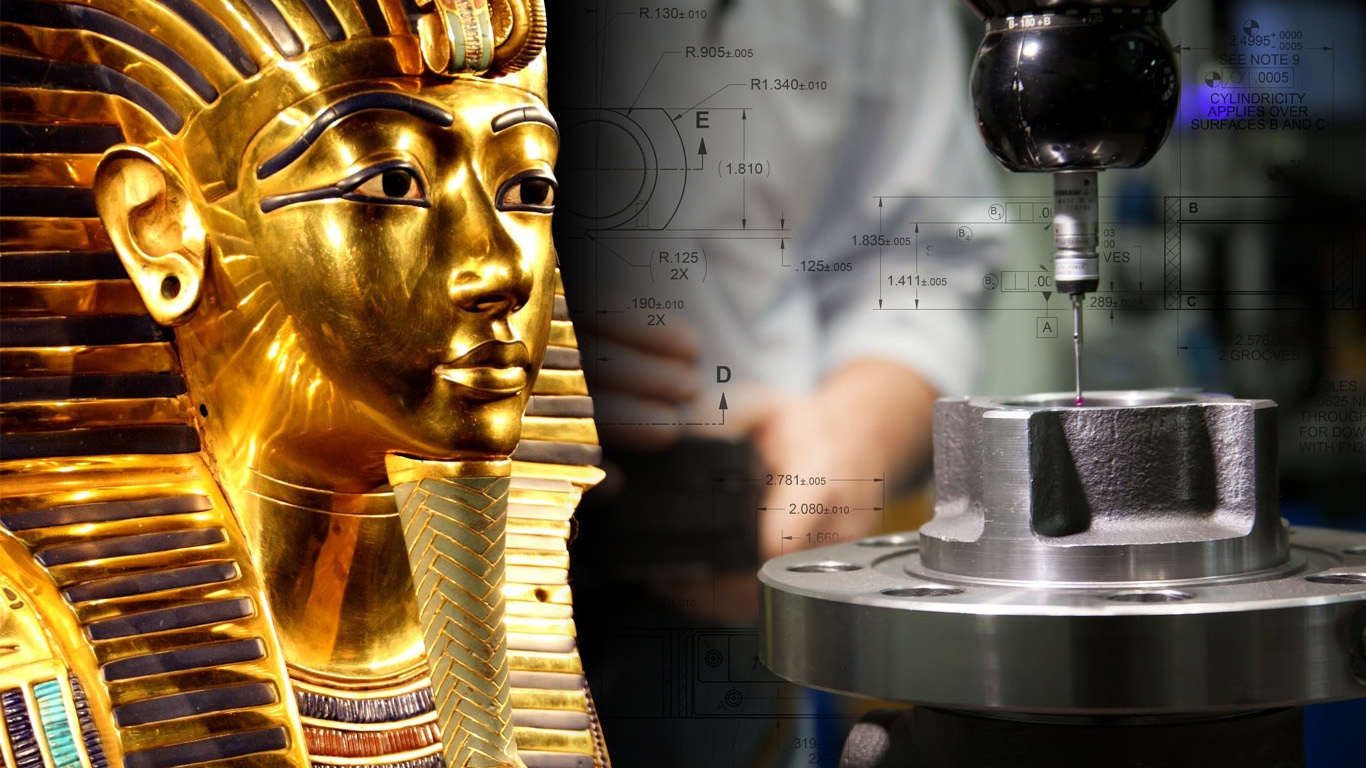
Modern manufacturing wouldn't be possible without rigorous standards of measurement, along with sophisticated tools and techniques to help us measure tools, workpieces and finished products.
CNC machining is a prime example of the practical uses of modern measuring, or metrology. In metal-based manufacturing, CNC machining is often the last process before a part is delivered. Without incredibly accurate and precise ways to measure and cut, many of the metal products we take for granted would be impossible to produce.
The history of measurement is the story of how human civilization strove to find new ways to measure accurately, and it all leads up to modern metrology.
Metrology all started with the idea of standard units of measurement. Around 6,000 BCE, civilizations had already developed measurement standards in order to calculate crop distribution and food consumption.
From then on, a wide variety of measuring standards have been used. Many were based on body parts, like the Egyptian ‘cubit,’ which measured the length from the elbow to the tip of the middle finger. Perhaps the most scientifically rigorous standard unit is the meter, which was first defined to equal one forty-millionth of the Earth’s circumference, and was determined through an 8-year, multinational survey mission. Later, the meter was re-defined based on measurable wavelengths of light.
Measuring standards used throughout history include:
- The Egyptian cubit (circa 3,000 BCE): approx. 43-53cm, based on the distance between the elbow and the tip of the middle finger. Actual length varied depending on which Pharoah was in power.
- The Roman Mile: 1,000 two-step paces; actual length varied, but this distance is very similar to today’s mile. 5,280 feet was declared the official measurement by Queen Elizabeth I in 1593.
- The Metric System: a universal measuring system first officially introduced in 1795. Spacial dimensions are based on the meter, which has had several different standards over the years. The meter is currently defined as the "length of the path travelled by light in vacuum during a time interval of 1/299 792 458 of a second."
- Imperial Measuring System: introduced in the United Kingdom in 1824; now still widely used in the United States, and includes yards, feet and inches. Inches have been based on barley grains, poppy seeds and a king's thumbnail.
Accuracy, Precision and Tolerance
Accuracy refers to how close a measurement is to a standard value. An accurate part is one that is produced to dimensions at, or very close to, the intended standard measurements.
Precision is accuracy through repetition. In CNC machining, precision means that every instance of a part will have the same, or very similar, dimensions. In metrology, precision can also mean that multiple readings give similar measurements.
Tolerance, another term you’ll hear quite often in the CNC machining world, is the degree to which a dimension is allowed to vary without making the part defective. This value is usually expressed as a range, as in “+/- .004 inches.”
Metrology Today
The sophistication of our measuring units coincides directly with our ability to measure more accurate dimensions. We’ve already come a long way from measuring the Pharaoh’s forearm to measuring wavelengths of light, and recent decades have seen even more advancements in metrology.
As our measuring demands have become more strict, our measuring standards have also changed. We are no longer content to call an inch "three barley grains laid end to end," but now define it in reference to the metric system (an inch is officially 2.54 cm.) When manufacturing microscopically intricate products like microchips, or even threads on a machined screw, we need to be able to measure to an extremely high degree of accuracy, or the part will not function as intended.
How to Measure Accurately
CNC machine shops and other facilities relying heavily on accurate and precise measurements make use of CMMs, or Coordinate Measuring Machines. CMMs allow metrologists to measure not only three dimensions, but also shape-specific characteristics like flatness, angularity and concentricity. By using machines to speed up the process, they can take hundreds, even thousands, of individual measurements, and can create accurate computer models of parts. This allows experts to track quality markers, reverse engineer parts, and diagnose problems.
For more information on the tools used in CNC machine shops to measure these extremely small dimensions, check out our blog post, 7 Essential Tools for Modern Machine Shops.
With CNC machining, quality means a high degree of accuracy and precision in every batch, every time. When you work with a CNC machine shop, make sure they have a metrologist on staff and up-to-date equipment. There's no way to guarantee quality if you don't have the tools and the skills to measure it.
For more tips on choosing the right supplier for metal-based manufacturing, download our free Buyer's Guide to Raw and Machined Cast Products.
Tags: Machining, CNC Machining, Metrology, History
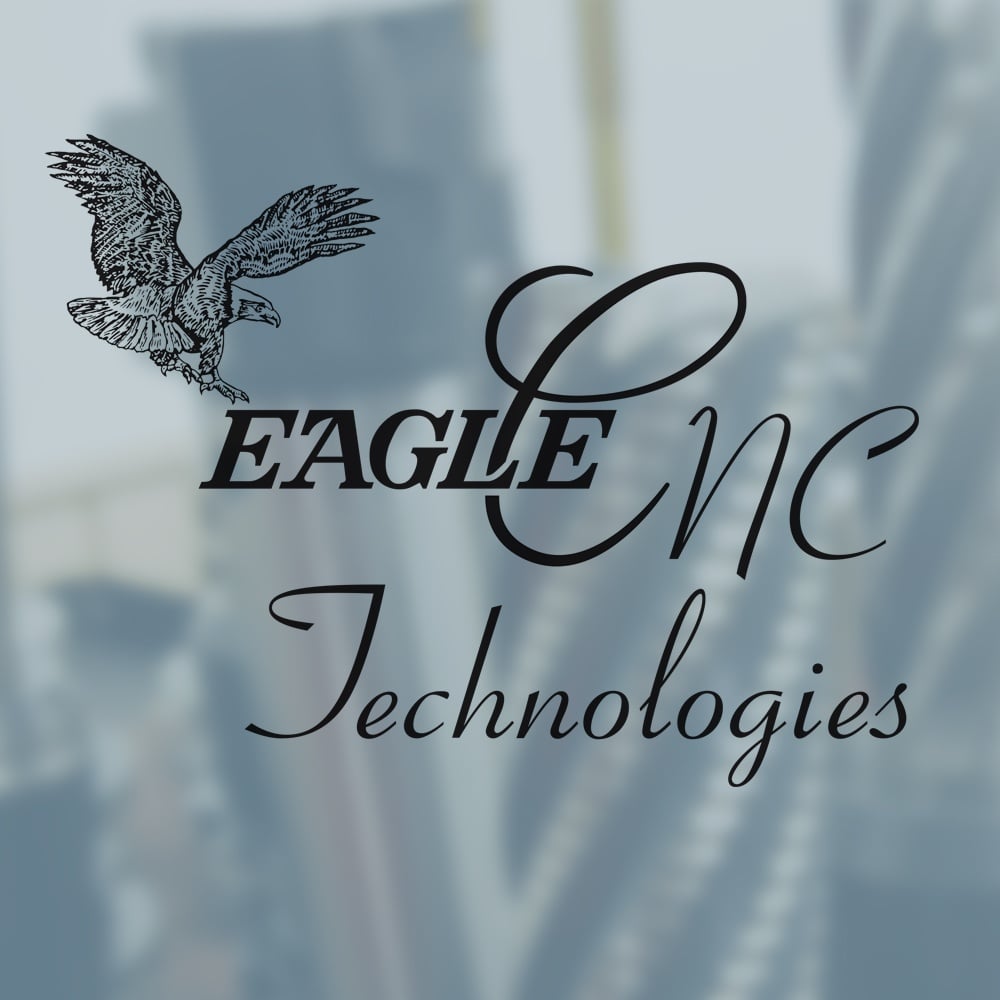