Industrial Valve Types and Applications
Clockwise from top left: Globe valve, butterfly valve, gate valve, ball valve
Valves are employed in just about any situation involving the flow of liquid or gas. A valve controls the flow of water through your kitchen sink. A different valve brings propane gas into the burners of a gas stove. Outside the home, industrial valves are built to handle high pressure, either from fluid or gas, and to last through years of use in harsh environments. Most utilities, from water to oil and gas, wouldn't be able to function without heavy duty, industrial-strength valves.
Because many components of industrial valves are cast, foundries and machine shops like the Eagle Group often supply valve manufacturers with the parts they need to assemble finished products. The following valve types represent the most commonly seen valves for industrial applications around the world.
Gate Valves
A gate valve consists of a channel that can be opened or closed by moving a metal gate up and down. When raised, the gate clears the channel and allows flow; when lowered, the gate obstructs the channel.
Most often considered isolation, or on/off valves, gate valves have been around for decades. Their simplicity allows them to be produced at relatively low cost, and with fewer parts than other valve types. However, their design makes them difficult to control precisely. Gate valves are most prevalent in the water industry.
Butterfly Valves
A butterfly valve consists of a channel and a paddle affixed to the channel through its central axis. The paddle, which is often disc-shaped, can spin to obstruct or open the channel.
Butterfly valves are another type of isolation valve; while they offer little control in terms of flow rate, they do allow large volumes of material to flow through the channel. Because the paddle can be positioned parallel to the flow, they barely obstruct the flow when opened. Butterfly valves are easier to control through remote actuators than gate valves, but they are often limited to large-volume applications.
Ball Valves
A ball valve is comprised of a valve housing, which is often a metal casting, and a perforated ball. Actuating the valve turns the ball, increasing the flow as the perforation comes in line with the channel.
New developments in ball valves, such as segmented ball valves, allow greater control over flow rates. As a result, modern ball valves have many advantages: they can be precisely controlled, either manually or electronically, and they also allow higher volumes than globe valves.

Globe Valves
A globe valve is characterized by an S-shaped channel and a horizontally oriented valve member that raises and lowers to control the flow of fluid or gas.
Globe valves are designed as control valves, and are able to modulate flow more accurately than other valve types. Not only does globe valve design support control, but many valve bodies allow interchangeable inner parts, so the orifice in the middle can be larger or smaller depending on the user's needs. However, globe valves restrict flow more than other valves; ball valves can offer 30% - 40% higher flow rates.
Valve Manufacturing
No matter what type of valve is being produced, the manufacturing process takes several steps. Many valve components can be cast, resulting in durable valve bodies and inner parts. In order to finish valve bodies, threads must be machined into any areas that will connect to other valve parts, or to upstream and downstream pipes.
Inner components can be produced using a variety of methods. The ball of a ball valve often must be machined in order to produce the smoothest, most precise spherical surface possible.
Depending on the surface finish and tolerances required, a variety of metal casting methods can be used to produce valve components. Eagle Alloy produces valve enclosures, bonnets and other parts through shell mold casting. Eagle Precision manufactures additional components through investment casting. Still more metalcasting processes are used by Eagle Aluminum, like permanent mold casting and greensand casting, to manufacture valve system components for different applications.
To learn more about industrial valves and valve manufacturing check out our post, Anatomy of an Industrial Valve
Tags: Manufacturing, Valves
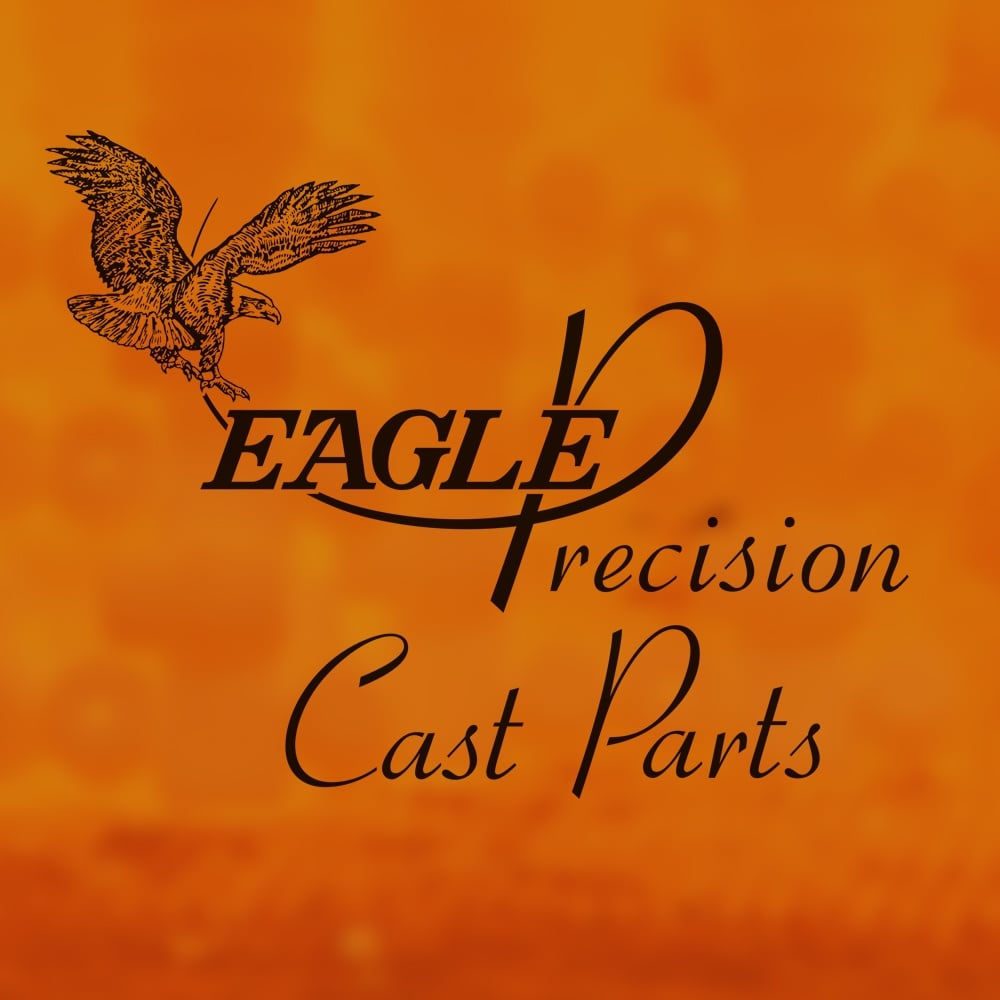
Written by Deb Pipoly
Deb Pipoly is President of Eagle Precision Cast Parts, an investment casting company located in Muskegon, MI.