The Heart of the Foundry: Celebrating the Career of Michigan Casting Trailblazer Dave Fazakerley
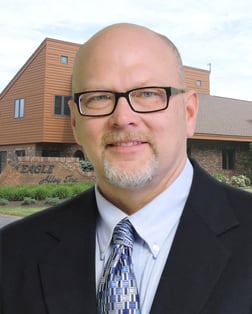
Dave Fazakerley, Eagle Alloy President and Chief Operating Officer, has played a central role in shaping the company since its early days. Over the course of his career, he has helped guide Eagle Alloy’s growth, build its operations, and foster a culture of quality and innovation—contributions that have helped the company become a recognized leader in the steel casting industry.
After exactly 46 years of dedicated service, Dave is bidding farewell to the company he helped build from the ground up. On April 21st, 2025, he not only marked his work anniversary with Eagle Alloy but also officially began his retirement.
Like many classic American business origin stories, Dave’s career in casting started in a garage. He and his brother, Eagle Alloy co-founder Mark Fazakerley, created their own metalcasting setup while Dave was still in high school.
“We constructed a brass and aluminum furnace ourselves,” recalls Mark. “We just got the components and put it together. He and I started out by making patterns and pouring brass belt buckles in my garage.”
“It was quite the thing,” Mark adds, referring to the belt buckle craze of the late ‘70s. Imagine Burt Reynolds or Elvis in their heyday, sporting oversized brass statement buckles. That’s the kind of product the Fazakerley brothers were supplying to their earliest customers. “We did some creative belt buckles,” Mark recalls. “We even commemorated a couple local high schools with their mascot.” That DIY garage setup whet their appetites for metalcasting, kicking off a journey that would eventually lead to running a steel foundry with over 300 employees, casting parts for fortune 500 companies.
Just a few years later, in 1978, both brothers were already working in the foundry business. Dave had put in a year at a West Michigan shell-mold foundry, and Mark and his business partner, Wayne Jarvis, were about to open Eagle Alloy. When Mark decided to start a shell-mold foundry, bringing his brother on board made a lot of sense: not only was he someone Mark could trust, but his hands-on foundry experience gave him more direct shell molding acumen than anyone else on the team.
“Dave was the very first employee other than the two founders,” recalls John Workman, Co-Chairman of the Board at Eagle Alloy. He was truly there from the beginning, building the foundation alongside his brother, Mark, and co-founder Wayne Jarvis. John joined as a third partner just over a year after the company began and worked closely with Dave on the production side for many years.
Of course, working with family came with its own dynamic. “I found out rather quickly that he didn’t especially care for taking orders from his brother,” Mark says with a laugh. Since Mark focused on sales, pattern engineering, and quality, and Dave worked in production—an area under John’s leadership—it made practical sense (and helped keep the peace) for Dave and John to work side by side on the shop floor.
As Eagle Alloy evolved, so did Dave’s responsibilities. “Dave grew in his role as the company grew,” says John. “He served as a supervisor, production manager, and ultimately as President, Chief Operating Officer, and Board Member.” Looking back on their parallel journeys as part of the original team, he adds, “Quite frankly, we all grew together in our roles and responsibilities.”
Dave’s deep knowledge of the casting process, his strong analytical skills, and thoughtful approach to operations and communication have played a key role in Eagle Alloy’s growth, as well as his role in it.
Mark Fazakerley recalls those early days of rapid expansion. “We were doing an expansion every three or four years over a couple of decades,” he says. “To go from 3,000 square feet to a quarter of a million is a lot of steps. Every time we put another building up, we wanted to keep our workflow,” says Mark. “All the things that require placement of equipment and processes that facilitated the most efficient way to process a part—Dave played a big part in all of that.”
“He always had an excellent perception of how product should flow through a shop, no matter how we configured the shop at the time, and with the minimum effort used,” Mark continues. “He was smart and had good common sense when it'd come to manufacturing.”
Dave’s colleagues know him as a leader, a mentor, and an innovator—just what you’d expect from the President and COO of a foundry like Eagle Alloy.
Rich Chase, who has worked side-by-side with Dave for more than a decade and is set to step into his role, shared some insight into what it’s been like reporting to Dave and growing under his mentorship. “He's been teaching me, training me, mentoring me for 10 years. I started here in 1987—just a kid out of high school, first real job,” reflects Rich. “Honestly, I just moved up the ranks. Eagle Alloy is wonderful about promoting from within, and that's what happened. They just kept giving me opportunities, and I learned. Dave prepared me for the job, really. We’re good friends now, and he taught me a lot.”
Among all of Dave’s strengths, many of his colleagues say what stood out most was his ability to pair deep operational knowledge with a natural talent for communication. “He has a thoughtful perspective of the operation and always gives well-thought-out communiqués to the plant,” says John Workman, reflecting on what made Dave so effective in his role as COO.
Rich agrees. “He knows everything about a foundry,” he says, “but his strongest skill outside the shop is wordsmithing.” Dave’s letter-writing abilities to get a point across were legendary. “He can write a letter like nobody else I've ever met. He's blunt—he'll lay the facts out there—but he words it in a way that doesn’t offend anyone. By the time he finishes, he makes every employee think they wrote it!”
That unique combination of foundry production knowledge and communication skill is, according to many, Dave’s greatest legacy—especially in his leadership of Eagle Alloy’s lean manufacturing initiative. Even with early success, Eagle Alloy’s leadership wasn’t satisfied with the status quo. They saw an opportunity to achieve greater efficiency, stability and quality by implementing lean tools tailored to their specific production environment. “Dave was very good about saying, ‘We need this because of this reason,’ versus, ‘We need it because it looks good and everybody else has one,’” explains Rich Chase. “He made sure the company truly needed to invest in new equipment or technology before making the decision.”
That instinct—to distinguish between wants and actual needs, and to weigh each investment carefully—allowed Dave to lead and expand lean initiatives that had a direct impact on plant layout and productivity. “Dave has been responsible for the lean manufacturing initiative and plant layout that drives our productivity,” says John Workman. “He’s hired excellent folks to lead production and has managed to keep our culture alive with both the production employees and management team.”
Implementing lean tools the right way wasn't easy. It required not only investing in new equipment and infrastructure, but also shifting the culture, from individual work styles to a unified focus on getting things done in the optimal way. Establishing clear communication channels and enforcing accountability at every level, every single day, has been essential to creating an environment of continuous improvement. And with hundreds of employees from diverse backgrounds and experiences, keeping everything running smoothly is not always an easy feat.
But that’s where Dave excelled. His deep understanding of the production process, combined with an ability for crafting language in just the right way, helped align employees and keep operations running at their best. “He was able to draw the line when he needed to and encourage somebody in their growth if he could,” says Mark Fazakerley.
With a strong foundation in place, Eagle Alloy is well-positioned to remain a vital part of West Michigan’s manufacturing landscape for years to come. As Rich Chase puts it, “Eagle Alloy is a very successful company—the way Dave has steered the ship—and I just want to keep her on course.”
What’s next for Dave in retirement? Ask anyone who knows him: “No question there—hunting and fishing!”
Above-left: Dave Fazakerley with his sons, Andy (left) and Eric.
Above-right: The original Eagle Alloy team. Left to right: John Workman, Wayne Jarvis, Dave Fazakerley and Mark Fazakerley
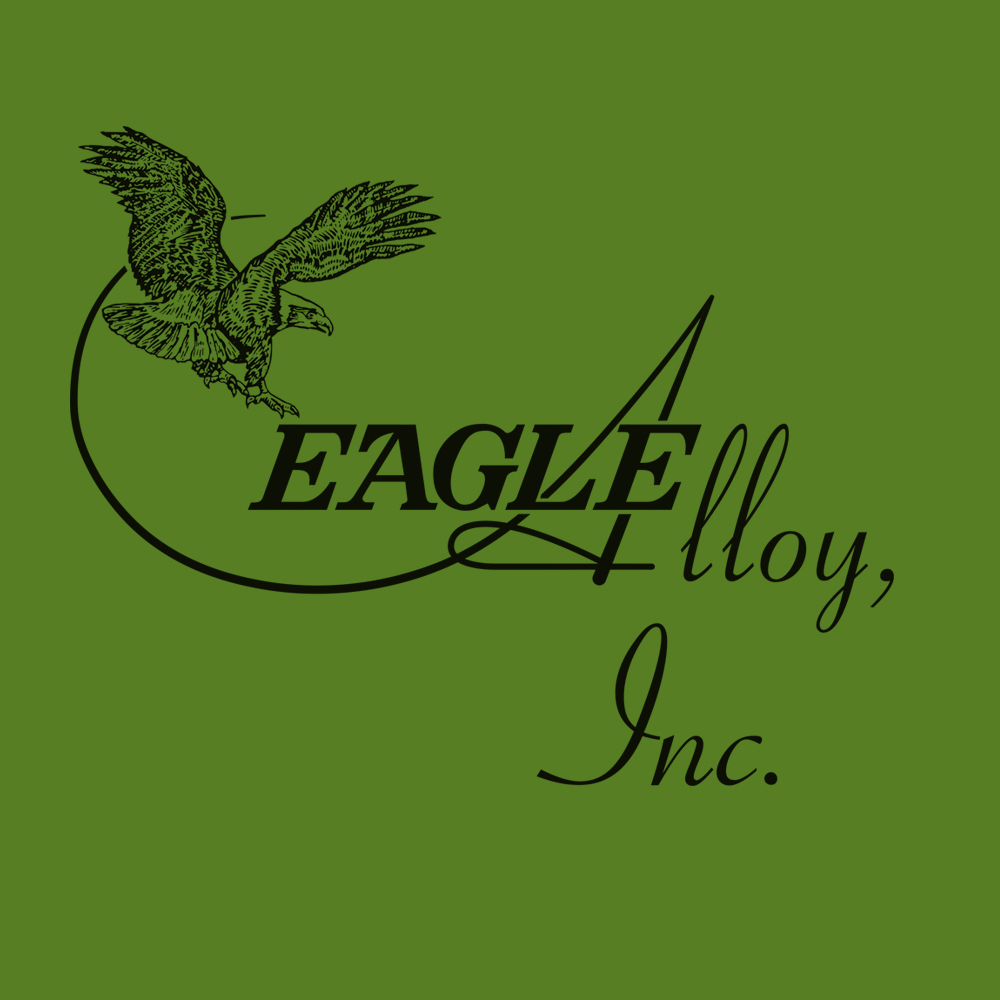
Written by Lisa Price
Lisa is Chief Human Resources Officer and Secretary at Eagle Alloy. She has been with the company since August of 2000.