Stories from the Lean Manufacturing Journey
Eagle Alloy has been practicing lean manufacturing for close to a decade. Beyond the benefits to productivity and efficiency imparted by lean tools, Eagle companies have come to see lean manufacturing as part of their company culture. The inclusiveness, creativity and quality improvement they’ve been able to foster has paid off dividends, both in workplace atmosphere and customer retention.
Lean implementation makes a more dependable supplier
Almost all the way back at the beginning of Eagle Alloy’s lean journey, about six months into their implementation of cellular manufacturing, the company was already seeing a noticeable productivity boost. They came into contact with a potential customer—we’ll call them Company A—who scheduled a shop tour at Eagle Alloy. Company A was already a successful manufacturer, but their casting supplier had recently gone bankrupt and they were looking for a replacement.
When Eagle Alloy reps met Company A reps, they talked a lot about lean manufacturing. Company A was farther along in their lean journey, and they understood the benefits a robust lean strategy could have for a mid-sized steel foundry like Eagle Alloy. Even though they were new to the game, Eagle staff had already seen some of those benefits in the Finishing Department, with nearly 20% gains in productivity in less than a year’s time.
Company A was impressed by Eagle Alloy’s readiness to embrace lean tools, but even more importantly, they knew that a company that successfully implements lean manufacturing would be dependable. Across industries, companies that employ lean tools often see gains in productivity, increases in quality and elevated on-time delivery rates. With a continued focus on lean, the bankruptcy that befell their previous supplier would be much less likely to knock on Eagle Alloy’s door.
Company A awarded Eagle Alloy the contract, and nearly a decade later they’re still a major Eagle Alloy customer. Both companies continue to integrate lean tools into their manufacturing processes, and continue to see gains on multiple fronts.
Takt Time: Building an inclusive planning process
According to Mark Fazakerley, co-founder of Eagle Alloy, “I’ve never seen a manufacturing process that’s so inclusive.” Lean manufacturing encourages organic collaboration between management and shop-floor operators, resulting in a culture of inclusiveness that strengthens the company.
One of the most successful lean tools for Eagle Alloy has been Takt Time. To begin the takt time process, they hang two big sheets of white paper on the wall. Next, they list all the steps required to produce a single part. After listing around 20 steps, everyone, from shop-floor operators up to C-level management, stands together and studies the sheets of paper. Operators can say exactly what they do first, second, third and on down the line. They can talk about variations in their work and areas where they experience bottlenecks. Managers are right there to learn from their employees and adjust the process to maximize efficiency. When managers implement changes, their employees know exactly why the changes are being made. More importantly, they can take ownership of the new process because they were directly involved in the planning phase.
“It’s not just the foremen walking into a department and saying how we’re doing this step, how we’re doing the next step and on down the line. It’s a lot of common sense. You don’t have to be an engineer when it comes to common sense,” Fazakerley continues. At Eagle Alloy, employees at all levels get a chance to offer their advice to improve processes. When everyone works together, the company feels more like a cohesive unit. The cooperation encouraged during the takt time process can have lasting effects, opening channels of communication that otherwise wouldn't exist.
Learn more about lean manufacturing: download the Eagle Group Lean Infographic, with a visual history of lean manufacturing and a run-down of key lean tools.
Tags: Lean Manufacturing, Efficiency, Company Culture
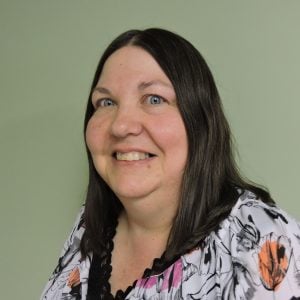
Written by Vikki Shonkwiler
Vikki is Sales Technician at Eagle Alloy, Inc. in Muskegon, MI. A Hoosier at heart, she grew up in Indiana and graduated from Indiana University with a double major in computer science and Spanish. She is a self-professed numbers geek—so much so that she actually enjoys doing tax preparation. When she’s not crunching numbers or managing sales teams, Vikki enjoys traveling and spending time with her children and grandchildren.