Improving Casting Production with In-House Robotics Expertise
In many ways Dakota Hanson (above) is a typical Young Millennial: he's an avid Tik Tok fan, spends his spare time playing Call of Duty, and has a job working with cutting-edge technology. However, unlike many members of his generation, Dakota's workplace is more than a laptop and a WIFI connection. As an Engineering Technician at Eagle Alloy (a shell molding facility in Muskegon, MI) Hanson specializes in programming robotic cells that play an integral role in the manufacturing process.
In fact, Eagle Alloy has a growing number of employees whose job descriptions include programming and operating robotic cells. Through a continuing education program led by robotics manufacturer ABB, Eagle Alloy has been able to provide its in-house team with manufacturing robotics expertise, further improving the company’s response time and resilience.
The Benefits of Robotics for Metalcasting
Eagle Alloy has long been an early adopter of new technologies. Automation is no exception: the company opened its first robotic grinding cell in 2018, and has already expanded to three cells with plans to add a fourth in 2022. Robotic cells provide three main benefits: improved safety, improved efficiency, and greater precision in grinding.
Improved Safety
Eagle Alloy has a stellar safety record (last year the company celebrated 500,000 Hours of No Lost Time; since then they’ve already surpassed 750,000) and the company seeks continuous improvement in this area. Robotic cells create an opportunity to reduce man-hours spent engaging with comparatively dangerous tasks. Traditional lean grinding cells require 3-4 operators per cell, while robotic cells can work with just one operator. Furthermore, the operator in a robotic grinding cell is not required to interact with grinding belts or wheels, which are the primary sources of safety hazards in grinding.
Improved Efficiency
Robotic cells can process parts significantly faster than manual cells, and the combination of speed and automation create a significant gain in production. All told, manual cells average 2,950 pounds per person per shift while robotic cells average 4,000 pounds per person per shift. Quite often operators achieve over 10,000 pounds in one shift on certain part numbers that maximize the potential of robot grinding.
According to Nic Tarzwell, Chief Technology Officer at Eagle Alloy, "If it makes the work easier for the guys on the floor, we have to do it. Our focus is on maximizing what our production employees are doing." With robotic grinding cells in place, operators who would usually be required for grinding can work other stations like molding, pouring, heat treat or quality control.
Greater Precision in Grinding
Eagle Alloy’s robotic cells make use of a laser vision system that evaluates the wear of the grinding surface and adjusts grinding time to match. The same system could be adapted to evaluate the surface of the part itself and allow for precise grinding to fit within a defined tolerance range. Additional machining process are often required when parts call for a high degree of surface uniformity, and finishing costs start to add up for larger runs. Robotics-facilitated precision grinding can result in significant savings for customers.
Learn more about the laser vision system and see an Eagle Alloy robotic grinding cell in action in this video:
Bringing Robotics Expertise In-House
Eagle Alloy utilizes ABB robotic arms in its grinding cells. In the past, the company relied on external consultants to troubleshoot and service the robotic machinery. However, high demand often led to long wait times and relatively simple problems were resulting in significant downtime. In order to fully take advantage of the benefits provided by ABB's robotics, Eagle Alloy elected to train an in-house team to troubleshoot and program the robotic cells.
ABB offers a robust training program called ABB University, where they train manufacturing professionals in dozens of countries around the globe to understand and use their products. Eagle Alloy Engineering Technician Dakota Hanson has already taken three courses through ABB University. "They have week-long classes in a school setting," he says. "Teachers are previous field technicians or programmers, so they have all the answers." Students also get their own training robot for the week that they can use to perform exercises, further solidifying their knowledge of programming and integration.
ABB University Robotics Course Guide, courtesy of ABB
Back at the Eagle Alloy facility, Hanson finds plenty of demand for his new skills. He works full-time getting new part numbers programmed into the robotic cells, along with ensuring that the existing parts are running smoothly. He and fellow Engineering Technician Dave Armstrong are available on a daily basis to respond to issues or answer operators' questions. While a simple part drop might have taken a cell offline for days (or more), issues can now be resolved in minutes. Hanson and Armstrong also work together to train new operators to use robotic cells, creating task diversity for Eagle Alloy's existing workforce.
As part of ABB's implementation and training systems, they provide virtual robot software. While COVID-19 continues to disrupt in-person education, students can learn remotely using a digital twin of their training robot. The virtual environment has real-world uses as well: if all of Eagle Alloy's robotic cells are in use, Hanson can test new part numbers using a digital mockup.
Eagle Alloy benefits from the added efficiency and safety made possible by the robotic cells, and customers also benefit from the company’s improved resilience. If any challenge arises, Hanson or Armstrong have the knowledge and the tools to get production back online as soon as possible. More uptime can lead to faster throughput and more consistent turnaround, both key benefits to casting customers managing complex supply chains.
The Future of Robotics at Eagle Alloy
Eagle Alloy CTO Nic Tarzwell has big plans for robotics. "Grinding is one of the biggest safety problems and biggest customer complaint areas, but we don't plan to stop there," he says. "We'll expand automation into other areas like gluing shell molds, water jet cutting, and different types of gating control." The shell department is another area with safety concerns, where automation could reduce heavy lifting performed by operators. The sand plant, which is also fairly automated, presents another potential use for a robotic arm.
Just as manufacturers like Eagle Alloy are always on the lookout for opportunities to automate their facilities, ABB is also working to push the envelope in terms of robotics and their capabilities for manufacturers. According to the company's website, "ABB is ranked among the top 100 most innovative companies in the world...Our businesses invest approximately $1.5 billion annually in R&D, carried out by some 9,000 scientists and engineers in more than 20 countries."
Eagle Alloy, and the Eagle Group as a whole, are part of a growing trend in American manufacturing that embraces technology not just for production efficiency, but also for the benefits it provides to the workforce. Safety, job satisfaction and upward mobility are also key markers of a successful company, and automation is helping the Eagle Group uphold those values.
Tags: Eagle Alloy, Capabilities, Technology, Robotics, grinding, Employees
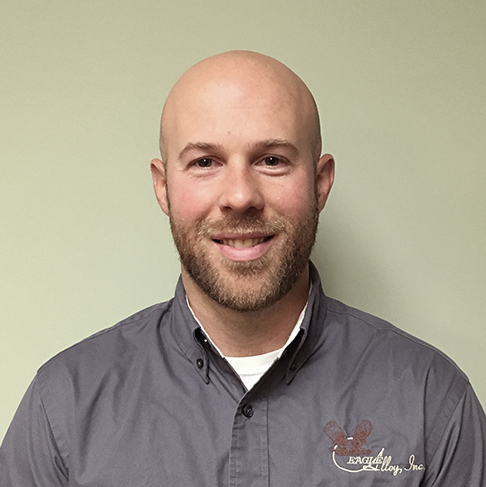
Written by Jason Klein
Jason Klein is Senior Process Engineer at Eagle Alloy. He has been with the company since 2010.